Technical
specialist
Автор — разработчик
Разработано на основе Рекомендацийпо организации получения среднего общего образования в пределах освоенияобразовательных программ среднего профессионального образования на базеосновного общего образования с учетом требований Федеральных государственныхобразовательных стандартов и получаемой профессии или специальности среднегопрофессионального образования (ФГАУ «ФИРО», 25 февраля
2015 г.).
Разработчик:Антопуло Е.И – преподаватель высшей квалификационной категории КГБПОУ «АПТ»
1.Широкий спектр услуг
|
A wide range of services |
1.1.Режущий инструмент
|
Cutting Tool |
А. монолитный режущий инструмент В. Сборный режущий инструмент
|
A. Monolithic cutting tool B. Prefabricated cutting tool |
1.2.Воспомогательный инструмент 1.3 Измерительный инструмент 1.4 Шлифовальный интсрумент 1.5 Ручной инструмент
|
1.2.Auxiliary tool 1.3 Measuring instrument 1.4 Grinding equipment 1.5 Hand tools |
2.Инструментальная мебель
|
2.Tool furniture |
3.Инвентарь
|
3.Inventory |
4.Логистика
|
4.Logistics |
1.Широкий спектр услуг
эксперт
|
|
expert |
измерительный инструмент
|
|
measuring tool |
режущий инструмент
|
|
cutting tool |
воспомогательный инструмент
|
|
auxiliary tool |
динамометрический инструмент
|
|
dynamometer tool |
специалист
|
|
specialist |
оптимизация процессов
|
|
process optimization |
производство
|
|
production |
автоматическая система
|
|
automatic system |
затраты
|
|
cost |
заказ
|
|
order |
контроль |
|
control |
|
|
|
прозрачность процесса
|
|
transparency of the process |
калибровка
|
|
calibration |
проверка
|
|
check |
лаборатория
|
|
laboratory |
услуга
|
|
service |
поставка
|
|
shipment |
бесплатная доставка
|
|
free shipping |
экспресс-доставка
|
|
express delivery |
склад
|
|
warehouse |
единая база |
|
single database |
электронных чертежей |
|
electronic drawings |
моделирование
|
|
modeling |
рабочая зона
|
|
work area |
вычисление траекторий
|
|
calculating trajectories |
параметры
|
|
parameters |
эффективные решения |
|
Effective solution
|
снижение нагрузки |
|
Load reduction
|
максимальная экономия |
|
Maximum economy |
конфигурация |
|
configuration |
штрих-код |
|
Barcode |
каталог |
|
catalog
|
высококачественный инструмент |
|
Quality tool |
доступ |
|
access |
индивидуальные требования клиента |
|
Individual requirements of the client |
интеграция |
|
integration
|
использование |
|
usage |
состояние заказа |
|
Order status |
Text №1 Read andtranslate.
Machine operators mainly workwith heavy machinery. They assist with the installation of their equipment andhelp maintain it by performing periodic tests and repairs. Listings for thesepositions may also be found by searching for machinists or tool and die makers.
Machine operators may work with computer-operatedequipment or with mechanical equipment. They install their machines, operatethem to aid in plant processes, and perform routine maintenance checks. Theyare self-motivated team players who have an aptitude for computers andmechanics.
Machine operators install,maintain, and operate machinery. They must have a strong understanding of themachines they work with. In-depth training may be required in order to preparea machine operator for their daily duties.
Machine operators may work withmechanical or computer-operated equipment. They must be technically-inclinedand be able to properly utilize tools and machinery. Since problems withmachinery may arise, machine operators must be able to analyze situations andfind solutions.
Candidates for this positionshould be detail-oriented and willing to learn. Machine operators should beable to follow instructions, work with others, and help ensure that all safetyregulations are followed.
•
• Assist in the installation, maintenance, and repair of machinery.
• Operate tools in order to aid in the manufacturing process.
• Perform periodic checks on equipment and solve problems asdetected.
• Work with others in order to ensure that equipment is in properworking order. Observeand follow company safety rules and regulations.
•
• High School Diploma/GED.
• Combination of additional education and experience.
• Aptitude for math, problem-solving, computers, and mechanics.
• Attention to detail.
• Ability to work and communicate well with others.
• Proficiency with hand tools.
• Willing to perform repetitive tasks for extended periods.
Our company is searching for atalented and experienced CNC machine operator to oversee our computer numericcontrolled (CNC) machines. You will be responsible for ensuring our companyproduces quality parts and tools specific to engineering drawings and clientstandards.
As the machine operator, thesuccessful candidate will be a highly skilled professional, with excellentattention to detail and mechanical aptitude. In order to excel in this role,you will also have to possess in-depth knowledge of the latest equipment andtechniques emerging in the industry.
• Set-up and manage CNC machines to perform different jobsincluding drilling, grinding and milling.
• Translate engineering drawings and requirements into dimensionsfor production.
• Ensure the CNC machine operates in accordance with the guidelinesof the company.
• Oversee the machines while they execute the tasks and make thenecessary changes to produce improved results.
• Check machinery on a daily basis to guarantee functionality.
• Record all machine actions by completing production and qualitylogs.
• Provide timelines to clients.
• Communicate logistics issues that arise in the process ofcreating a part.
• Ensure that results of machining process align with clientexpectations.
• Conduct regular CNC machine assessments.
•
• High school diploma or equivalent qualification required.
• Certificate or diploma in engineering is an advantage. 3years’ experience as a CNC machine operator.
• Ability to translate mechanical documents and engineeringdrawings.
• Great attention to detail with a goal-driven attitude.
• Strong comprehension and analytical abilities. Goodcomputer and mathematical skills.
Our company is searching for atalented and experienced CNC machine operator to oversee our computer numericcontrolled (CNC) machines. You will be responsible for ensuring our companyproduces quality parts and tools specific to engineering drawings and client standards.
As the machine operator, the successful candidate willbe a highly skilled professional, with excellent attention to detail andmechanical aptitude. In order to excel in this role, you will also have topossess in-depth knowledge of the latest equipment and techniques emerging inthe industry.
• Set-up and manage CNC machines to perform different jobsincluding drilling, grinding and milling.
• Translate engineering drawings and requirements into dimensionsfor production.
• Ensure the CNC machine operates in accordance with the guidelinesof the company.
• Oversee the machines while they execute the tasks and make thenecessary changes to produce improved results.
• Check machinery on a daily basis to guarantee functionality.
• Record all machine actions by completing production and qualitylogs.
• Provide timelines to clients.
• Communicate logistics issues that arise in the process ofcreating a part.
• Ensure that results of machining process align with clientexpectations.
• Conduct regular CNC machine assessments.
•
• High school diploma or equivalent qualification required.
• Certificate or diploma in engineering is an advantage. 3years’ experience as a CNC machine operator.
• Ability to translate mechanical documents and engineeringdrawings.
• Great attention to detail with a goal-driven attitude.
• Strong comprehension and analytical abilities. Goodcomputer and mathematical skills.
_______________________________________________________________________
Тext №2 Readand translate.
Аnnouncement
CNC machine operators, or CNC machinists, manage
computer numeric controlled(CNC) equipment from setup to operation, producing parts and tools fromdifferent resources including metal and plastic. They’re tasked with monitoringmachinery, inspecting finished products, and leading test runs.
CNC Operator JobDescription Template:
Our company is searching for atalented and experienced CNC machine operator to oversee our computer numericcontrolled (CNC) machines. You will be responsible for ensuring our companyproduces quality parts and tools specific to engineering drawings and clientstandards.
As the machine operator, the successful candidate willbe a highly skilled professional, with excellent attention to detail andmechanical aptitude. In order to excel in this role, you will also have topossess in-depth knowledge of the latest equipment and techniques emerging inthe industry.
Responsibilities:
• Set-up and manage CNC machines to perform different jobsincluding drilling, grinding and milling.
• Translate engineering drawings and requirements into dimensionsfor production.
• Ensure the CNC machine operates in accordance with the guidelinesof the company.
• Oversee the machines while they execute the tasks and make thenecessary changes to produce improved results.
• Check machinery on a daily basis to guarantee functionality.
• Record all machine actions by completing production and qualitylogs.
• Provide timelines to clients.
• Communicate logistics issues that arise in the process ofcreating a part.
• Ensure that results of machining process align with clientexpectations. Conductregular CNC machine assessments.
Requirements:
• High school diploma or equivalent qualification required.
• Certificate or diploma in engineering is an advantage. 3years’ experience as a CNC machine operator.
• Ability to translate mechanical documents and engineeringdrawings.
• Great attention to detail with a goal-driven attitude.
• Strong comprehension and analytical abilities. Goodcomputer and mathematical skills.
_______________________________________________________________________
№3 Write down newwords in your notebook
· machine tools with PC -станки с ПУ (программное управление)
· machine-building and woodworking industries — машиностроительная идеревообрабатывающая промышленность
· drilling machines witha PC — сверлильные станки с ПУ
· printed circuit boards- печатные платы
· EDM machines — электроэрозионные станки, станки электроискровой обработки
· complicatedconfiguration — сложная конфигурация
· programmable machines -программируемые машины
· to push the buttons –нажимать на кнопки
· manufacturing technology — технологияпроизводства
· software — программноеобеспечение
· to monitor the quality- следить за качеством
· responsibilities -обязанности
· to check — проверять
· to fixe — исправлять
· to determine theoperating mode — определять режим работы
· to control machine -управлять машиной
· to monitor the quality- следить за качеством
· working conditions — рабочие условия
· well-lit room — хорошо освещенная комната
· physical loads -физические нагрузки
· mental work -умственная работа
· «feel the material» -«чувствовать материал
___________________________________________________________________________
№4 Read andtranslate.
Text A: Machineoperator with a PC
Today, machinetools with program control are used in both the machine-buildingand woodworking industries. There are drilling machineswith a PC for drilling printed circuit boards, there are EDMmachines — with their power you can cut a very complicatedconfiguration in metal, and the processing accuracy is amazing … Youcan’t list all types of machines with a PC. Almost any modern productionbasically has programmable machines and to work on them it is notenough just to be able to push the buttons. Thespecialist should have an idea of the manufacturing technology ofparts, the tools used, and know the appropriate software.
What does a machine tooloperator with a PC do? He has many responsibilities. He checksand fixes work pieces and tools on the machine, determinesthe operating mode, controls machine operation andprocess flow.
In the process, theoperator monitors the quality of products, makesmeasurements of parts with special instruments. Working conditionsfor the machine operator with a PC today to call quite comfortable — this iswork in a warm, clean, well-lit room. Physical loadsare insignificant. Most of the operator’s working time is occupied by mentalwork, but if, for example, the technologist at the given production isa theoretician in pure form, then the operator should “feel the material”,know, if you like, the features of his character. That is why the machineoperator with a PC must have knowledge — deep and specific.
_____________________________________________________________________________
№6 Answer the following questions on the text.
1. Where are machinetools with program control used?
2. What kind of machineswith a PC do you know?
3. What does a machinetool operator with a PC do?
4. What personalcharacteristics should the machine operator have?
5. What does workingcondition in which the machine operator works?
____________________________________________________________________________
№6 Guess the meaningof the following international words
machine program control industry configuration metal production specialist technology operator fix process instrument comfortable technology characterspecific element industry result
__________________________________________________________________________
№7 Matcheach word with the correct translation.
1) tool
2) check
3) control machine
4) monitor the quality 5)drilling machines
a) проверять
b) сверлильные станки
c) следить закачеством
d) инструмент
e) управлятьмашиной
___________________________________________________________________________
№ 8 Put the verbsgiven in brackets in the correct form.
1. The operator (to have) many responsibilities.
2. He (to check) and (to fix) work pieces and tools on the machine.
3. The operator (to monitor) the quality of products
4. The operator (to control) machine operation andprocess flow.
5. Instruments (to consist) of many elements.
6. Physical loads (to be) insignificant.
7. A bolt (to consist) of the head and the shank with the thread.
8. A shaft (to rotate) about its axis.
____________________________________________________________________________
№ 9 Study new wordsand word-combinations.
· property — свойство
· metallurgy — металлургия
· separation — разделение, отстояние
· dense — плотный
· arrangement — расположение
· regularly — регулярно, правильно
· to slide — скользить
· malleable — ковкий, податливый,способный деформироваться
· bent ppof bend — гнуть
· to fracture— ломать
· ductile — эластичный, ковкий
· to draw — волочить, тянуть
· wire — проволока
· lead — свинец
· iron — железо, чугун
· grain — зерно
· to depend — зависеть
· size — размер, величина
· shape — форма, формировать
· composition— состав
· coarse — грубый, крупный
· treatment — обработка
· quenching — закалка
__________________________________________________________________
№ 10 Read andtranslate.
A metal is an element, compound, or alloythat is good conductor of both electricity and heat. Metals are usuallymalleable and shiny.
Metals are materials most widelyused in industry because of their properties. The study of the production andproperties of metals is known as metallurgy.
The separation between the atoms inmetals is small, so most metals are dense. The atoms are arranged regularly andcan slide over each other. That is why metals are malleable (can be deformedand bent without fracture) and ductile (can be drawn into wire). Metals varygreatly in their properties. For example, lead is soft and can be bent by hand,while iron can only be worked by hammering at red heat.
The regular arrangement of atoms inmetals gives them a crystalline structure. Irregular crystals are calledgrains. The properties of the metals depend on the size, shape, orientation,and composition of these grains. In general, a metal with small grains will beharder and stronger than one with coarse grains.
Heat treatment such as quenching,tempering, or annealing controls the nature of the grains and their size in themetal. Small amounts of other metals (less than 1 per cent) are often added toa pure metal. This is called alloying (легирование) and it changes the grainstructure and properties of metals.
All metals can be formed by drawing,rolling, hammering and extrusion, but some require hot-working. Metals aresubject to metal fatigue and to creep (the slow increase in length understress) causing deformation and failure. Both effects are taken into account byengineers when designing, for example, airplanes, gas-turbines, and pressurevessels for high-temperature chemical processes. Metals can be worked usingmachine-tools such as lathe, milling machine, shaper and grinder.
The ways of working a metal dependon its properties. Many metals can be melted and cast in moulds, but specialconditions are required for metals that react with air.
______________________________________________________________________
Задание № 11
Answer the followingquestions on the text.
1. Whatare metals and what do we call metallurgy?
2. Whyare most metals dense?
3. Whyare metals malleable?
4. Whatis malleability?
5. Whatare grains?
6. Whatis alloying?
7. Whatis crystalline structure?
8. Whatdo the properties of metals depend on?
9. Whatchanges the size of grains in metals?
10. What are the mainprocesses of metal forming?
11. How are metalsworked?
12. What is creeping?
_______________________________________________________________________
Задание № 12
Find the followingwords and word combinations in the text.
1. Свойства металлов
2. расстояние междуатомами
3. правильноерасположение
4. сильно отличаются посвоим свойствам
5. кристаллическаяструктура
6. размер зерен
7. форма зерен
8. закалка
9. отжиг
10.волочение
11.прокатка
12.ковка
13.экструзия
14. структура и свойствазерна
15. горячая обработка
16. усталость металла
17. ползучесть металла
18. плавка и отливка вформы
19. способы обработкиметаллов
|_____________________________________________________________________________
Задание № 13
Translate intoEnglish.
1. Металлы — плотные материалы потому, что между атомами в металлахмалое расстояние.
2. Металлы имеют кристаллическую структуру из-за правильногорасположения атомов.
3. Чем меньше зерна, тем тверже металл.
4. Закалка и отжиг изменяют форму и размер зерен в металлах.
5. Легирование изменяет структуру зерен и свойства металлов.
6. Металл деформируется и разрушается из-за усталости и ползучести.
______________________________________________________________________
Задание № 14
Complete the followingsentences.
1. Metals are…
2. Metallurgy is…
3. Most metals are…
4. The regulararrangement of atoms in metals…
5. Irregular crystals…
6. The properties of themetals depend…
7. Metals with smallgrains will be…
8….controls the nature of the grains in themetal.
9. Alloyingis…
10. All metals can beformed by…
11. Creep is…
12. Metals can be workedusing…
|_____________________________________________________________________
Задание № 15
Explain in Englishthe meaning of the following words.
1. malleability
2. crystalline structure
3. grains
4. heat treatment
5. alloying
6. creep
_____________________________________________________________________
Задание № 16
Study new words andword-combinations.
· electron – электрон
· oxygen – кислород
· cation – катион (ион сположительным электрическим зарядом)
· oxides – оксиды
· acidic – кислотный
· luster – блеск
· density – плотность
· to cleave –раскалывать
· thermal – теплый
· bond – связь
· ductility – тягучесть
· alloy – сплав
· solid – твердый
· brittle – ломкий
· resistant to corrosion– устойчивый к коррозии
· steel — сталь
· cast iron – чугун
· stainless steel – нержавеющая сталь
· alloy steel –легированная сталь
· chromium – хром
· nickel – никель
· molybdenum – молибден
· carbon steels –углеродистые стали
· aluminium – алюминий
· titanium – титан
· copper – медь
· magnesium – магний
· wiring — проводимость
1.1.Режущий инструмент
резание |
cutting |
спиральные сверла |
twist drill |
сверла для глубокого сверления |
drill for deep hole drilling |
машинные бестружечные метчики |
machine-made particle-free taps |
машинные развертки для станков |
machine reamers for machine tools |
развертки |
sweeps |
микрофорез |
micropores |
фреза |
Cutter, mill |
обдирочные фрезы |
Grinding mill |
концевые фрезы |
End mill |
резьбовые фрезы |
Thread milling cutters |
насадные фрезы |
Arbor-type cutters |
сверла |
drills |
монолитный режущий инструмент |
A monolithic cutting tool |
метчики |
taps |
плашки |
dies |
зенковки |
countersinks |
развертки |
sweeps |
ленточные пилы |
Band saw |
твердый сплав |
Hard alloy |
мягкий сплав |
Soft alloy |
фрезирование |
milling |
наклонные поверхности |
Inclined surface |
рассверливание |
drilling |
диаметр |
diameter
|
|||
средняя скорость |
Average speed |
|||
закаленная сталь |
Hardened steel |
|||
точение |
turning |
|||
пониженная мощность |
Reduced power |
|||
повышенная мощность |
Increased power |
|||
шпиндель |
spindle |
|||
нестабильные условия |
Unstable conditions |
|||
мощность |
power |
|||
шлифовать |
grind |
|||
центровочное сверло |
The centering drill |
|||
цилиндрический хвостик |
The cylindrical tail |
|||
короткие сверла |
Short drills |
|||
длинные сверла |
Long drill bits |
|||
короткие ступенчатые сверла |
Short step drills
|
|||
твердосплавные кольцевые сверла по металлу |
Carbide tipped annular drill bits for metal |
|||
сверхдлинные сверла |
Extra-long drills |
|||
спиральные сверла |
Twist drill |
|||
ленточное сверло |
Band drill |
|||
набор сверл |
A set of drill bits
|
|||
металлические листы |
Metal sheet
|
|||
стружечные канавки |
Chip grooves |
|||
удаление стружки |
Chip removal |
|||
большой кейс со сверлами |
Large case with drills |
|||
глубокое отверстие |
Deep hole |
|||
штифт |
pin |
|||
штифты-выталкиватели |
Ejector pins |
|||
переходники |
adapters |
|||
твердый сплав |
Hard alloy |
|||
нержавеющая сталь |
Stainless steel |
|||
резьба |
thread |
|||
Алюминевый сплав |
Aluminum alloy
|
|||
безопасность |
security |
|||
оснастка |
equipment |
|||
Система микросмазки |
Micro-lubrication system |
|||
Сквозное и глухое отверстие |
Through and blind hole
|
|||
Калибрирующая часть |
Calibrating part |
|||
самонаправление |
self-direction |
|||
Смазочные канавки |
Lubrication grooves |
|||
стружка |
chip |
|||
Внутренний подвод |
Internal supply
|
|||
покрытие |
cover |
|||
крутить |
twist |
|
|
|
смазка |
lubrication |
|
|
|
деформированность |
deformity |
|
|
|
оцинкованный |
galvanized |
|
|
|
отвинчивать |
unscrew |
|
|
|
Универсальное применение |
Universal application |
|
|
|
Круглая |
|
Round |
|
|
кромка |
|
Edge/ lip| hem| flange |
|
|
Трехзубая зенковка с рукояткой |
пластиковой |
Three-prong countersink handle |
with |
plastic |
зенковка |
|
countersink |
|
|
цековка |
|
counterbore |
|
|
стандарт |
|
standard |
|
|
развертки |
|
sweeps |
|
|
регулировать |
|
regulate |
|
|
Цилиндрический хвостик |
|
The cylindrical tail
|
|
|
Сьемный |
|
Removable |
|
|
Станки ЧПУ |
|
CNC machines |
|
|
Платины из кермета |
|
Platinum from kermet |
|
|
подача |
|
supply |
|
|
Комбинированное исполнение зубьев |
Combined design of teeth |
|
|
№1 Read andtranslate.
As we already know, to perform acertain operation we need different types of cutting tools.
Cutting tools can bechosen according to the:
1. JobMaterial
2. Whichtype of operation you are going to perform
It is used in metal cutting or forming to acquire thedesired shape, size, surface finish.
Types of CuttingTools:
Different types ofcutting tools are used in different types of machine, according to the usage ofthe cutting tool, we can divide it into 7-types, and those are:
• According to the shape of the cutting tool.
• According to the types of cutting.
• Depending on types of operations.
• The material of the cutting tool.
• With respect to the number of the cutting tool used in one tool.
• According to the direction of the tool movement.
• According to the motion of the tool.
№2 Прочтите текст и выполните следующие за нимупражнения:
most commonly used machine-tool.It is used I for great variety о f meta1 operations, such as turning, drilling,screw cutting and many others.
2. The principal units of the lathe are the bed, the headstock, thetailstock and the carriage with the apron.
3. The bed is the base of any machine-tool and it is made of greyiron casting on which the saddle and the tailstock slide along special guideways. The headstock is also located and bolted on the bed.
4. The headstock contains the spindle and the speed gearbox. Thespindle is the part of the machine to which power is applied to rotate thework. The changing of the spindle speed is effected by levers.
5. The tailstock consists of a casting fitted to the bed. Thefunction of the tailstock is to support one end of the work turned betweencenters and to mount the tools.
6. The carriage of the lathe, which carries the tool, is made up oftwo principal parts: the saddle and the apron. The saddle travels along theguide ways of the bed. The apron represents the front wall of the carriage. Onthe front of the apron are mounted the handles and levers by which the actionsof the tool are controlled.
4. Переведите на русский язык в письменной форме абзацы 3,4 и 5.
5. Найдите соответствующие ответы на вопросы и напишите их в тойпоследовательности, в которой заданы вопросы:
Вопросы
1. Whatoperations are the engine lathe used for?
2. Whatare the principal units of the lathe?
3. Whatunits are located on the bed?
4. Whatis the function of the tailstock?
5. Whereare the handles and levers mounted?
Ответы
a. To support oneend of the work turned between centers.
b. On the front of theapron.
с. For turning, drilling, screwcutting and others.
d. The headstock, thesaddle and the tailstock.
e. The bed, theheadstock, the tai1stock and the carriage with the apron.
6. Закончите предложения, выбрав соответствующий вариантокончания:
1. Theunit that contains the spindle and the gearbox is called….
1. Theunit that supports one end of the work turned between centers is called …
1. Theunit which carries the tool is called….
a) the carriage
b) the headstock
c) the tailstock
1. Theunits, by which the actions of the tool are controlled, are called…. a)guide ways
b) the saddle and theapron
c) levers andhandles
А. монолитный режущийинструмент
Спираль,ступенчатые икольцевые Spiral, step and ring drills made of fastсверла из быстро- режущейстали cutting steel
Сверла из монолитного твердого сплава Drills made ofmonolithic hard alloy
Метчики ирезьбовые фрезы Taps and threaded cutters Плашки,наборы резьбонарезного Tapsand threaded cutters инструмента, держатели
зенковка countersink
развертки scans
Ленточные и дисковые пилы по металлу Band and discsaws for metal
Насадныефрезы HSS и VHM HSS and VHM attachment cutters Концевые фрезы из быстрорежущейHigh-speed steel end mills стали
Концевые фрезы из монолитного End mills made of monolithic hard alloy твердого сплава
Для всех инструментовдля обработки For all cutting tools резанием
Твердосплавная концевая фреза Carbideend mill (long, extra long)
(длинная,сверхдлинная)
Цветоваямаркировка Color marking Профиль фрезы Milling cutter profile
стандарт standard
Хвостовик ( цилиндрический) Shank(cylindrical)
угол corner
подточка sharpeningрезьба carving
допуск allowance
Центровочное сверло Centeringdrill
Сверхдлинные центровочные сверла Extra-longcentering drills
Короткие сверла ShortDrills
Идеально длясверления с небольшой Ideal for drilling with a shallow depth глубиной
Сверла для металлических листов Drills formetal sheets
Сверло используется без центрования The drill isused without centering
Набор коротких сверл Aset of short drills
Спиральные сверла SpiralDrills
Стружечные канавки Chipgrooves
Особенно высокая прочность Especiallyhigh strength
Сверхдлинные спиральные сверла Ultra-longspiral drills
Конические сверла ConicalDrills
зенкер zenker
Короткие ступенчатые сверла ShortStep Drills
Для винтов с потайной головкий |
For countersunk head screws |
Презиционные конические сверла |
Positional Conical Drills |
Листовые материалы |
Sheet materials |
Кольцевые сверла |
Ring Drills |
Штифты-выталкиватели |
Ejector pins |
Устройства кругового резания |
Circular cutting devices |
Для вырезания колец |
For cutting rings |
Твердосплавное микросверло НРС |
Carbide micro drill |
Высокопроизводительные сверла |
High-performance drills |
Монолитный твердый сплав |
Monolithic hard alloy |
Короткое ступенчате сверло |
Short step drill |
Система микросмазки |
Micro-lubrication system |
Ручные метчики |
Manual taps |
Метчик машинный для сквозных отверстий |
Machine tap for through holes |
№1 Translate the text andcompose questions about the text.
Forced rotation turning appearsto be an effective machining method due to higher tool life, time efficiencyand acceptable quality. Several studies have been carried out to investigatethe basic characteristics of forced rotation machining. So far, tools are usedwhose design included several components. However, such tools may generatevibrations, which are undesirable in the process. In engineering practice, mostvibration problems are solved by reducing the cutting parameters (cutting speedand feed rate), which reduces machining productivity. For this reason, a newtype of monolithic rotary tool has been designed that eliminates the designcomplexity and high assembly accuracy requirements of current rotary tools.Based on the performed experimental research, it is possible to define theinfluence of cutting parameters on the cutting force. Next, the equation of thecutting force and the resulting roughness of the machined surface wasdetermined. In the introduction, the results of the analysis of machiningparameters with a rotary tool were added. The presented solution fundamentallyvalidates the new monolithic tool for forced rotation technology and definesits application for different machining materials.
№2 Translatecombinations of words, transcribe.Make sentences from these combinations ofwords
1.Основные виды обработки сприменением твердосплавных монолитных фрез
The main types ofprocessing with the use of carbide monolithic cutters.
Торцовое фрезерование-
Обработка паза — Боковое фрезерование- Объемноефрезерование-
Врезание под углом — Врезание по спирали- Трохоидальноефрезерование- Послойное боковое фрезерование- Послойное торцовое фрезерование-
Врезное фрезерование-
Сверление- 2.Типы концевыхтвердосплавных монолитных фрез. Types of end carbide monolithic millingcutters.
ЦИЛИНДРИЧЕСКИЕ —
КОНИЧЕСКИЕ — С ПЛОСКИМ ТОРЦЕМ — С УГЛОВЫМ РАДИУСОМ — СОСФЕРИЧЕСКИМ ТОРЦЕМ —
3.Боковая режущая кромка.Side cutting edge
Тип зуба Tooth Type |
Перевод |
Характеристики и область применения
|
Обычный ordinary |
|
Фрезы с неизменяющейся геометрией зуба, наиболее широко используется при черновом и чистовом фрезеровании контуров, обработке пазов и уступов
|
Конический conical |
|
Фрезы с угловым зубом применяются при обработке наклонных поверхностей, таких как литейные и штамповочное уклоны, после предварительной обработки цилиндрической фрезой
|
Черновой draft |
|
фрез чернового типа режущая кромка имеет зубчатую форму, что позволяет дробить стружку на мелкие части.
|
Фасонный shaped |
|
Данный тип фрез применяется для обработки поверхностей со |
|
|
сложным профилем.
|
№4 Translate the text as fully as possible.Write downthe most difficult vocabulary and transcribe it.
Инструментальныевставки
Traditionally, most cuttingtools are usually formed from a single piece and the cutting edge is ground tothe required geometry. These single piece tools, also referred to as monolithictools (Schey, 1987), are generally made from high-speed steels or carbonsteels. When the cutting edge wears beyond being useful, they can be reground.However, even when suitable replacement tools are available, tool changing istime-consuming and can add considerably to the processing time. In order toaddress this problem, cutting tool inserts or tips were developed. These aredisposable cutting tools and usually have a number of cutting edges. The numberof cutting edges will depend on the insert shape and whether a negative rakeangle has been incorporated into the tool holder, which allows both sides ofthe insert to be used for example, a square insert will have eight cuttingedges (Amstead et al., 1987). The inserts are usually clamped into atool holder, a typical example of which is shown in Fig. 5.34. Inserts may alsobe brazed into the tool holder. However, clamping is generally the preferredmethod as this allows the insert to be rotated or indexed to the next cuttingedge (Kalpakjian, 1995). There are a number of ISO standards that have beendeveloped to help in the selection of both tool inserts and holders for variousmachining processes.
Translate the text as fully as
possible.Write downthe most difficult vocabulary and transcribe it
A.Abrasive grains are blunt compared toconventional cutting tools. Effective rake angles are highly negative whichleads to a large compressive plastic zone ahead of and under the grain followedby a shallower tensile zone behind the grain.
It was shown in Chapter 14 thatthe depths of grain penetration are usually very small. This has implicationsfor the geometry of the grain contact. The grain can be considered as anextremely blunt cutting tool. Many of the grain contacts will not produce achip but will merely rub against the workpiece. The forces and frictioninvolved in grinding can be explained by considering the different types ofcontact involved in grinding. The following discussion outlines some basicmodels of abrasion. A useful test of a modelis whether it can explain values of force ratio experienced in rubbing,ploughing, and cutting.
C.Unexpectedly rapidincreases in urbanization throughout the world, especially since World War II,have brought many problems, including congestion, air pollution, loss of scarcesurface area for vehicular ways, and major traffic disruption during theirconstruction. Some cities relying principally on auto transport have even foundthat nearly two-thirds of their central land area is devoted to vehicularservice (freeways, streets, and parking facilities), leaving only onethird ofthe surface space for productive or recreational use.
D.Machine tool, anystationary power-driven machine that is used to shape or form parts made ofmetal or other materials. The shaping is accomplished in four general ways: (1)by cutting excess material in the form of chips from the part; (2) by shearingthe material; (3) by squeezing metallic parts to the desired shape; and (4) byapplying electricity, ultrasound, or corrosive chemicals to the material. Thefourth category covers modern machine tools and processes for machiningultrahard metals not machinable by older methods.
E. Hundreds of varietiesof metal machine tools, ranging in size from small machines mounted onworkbenches to huge production machines weighing several hundred tons, are usedin modern industry. They retain the basic characteristics of their 19th- andearly 20th-century ancestors and are still classed as one of the following: (1)turning machines (lathes and boring mills), (2) shapers and planers, (3)drilling machines, (4) milling machines, (5) grinding machines, (6) power saws,and (7) presses. The engine lathe, as the horizontal metal-turning machine iscommonly called, is the most important of all the machine tools.
№5 Сonsider a picturewith a monolithic cutting tool.Complete the translation.
№6.Торцовая режущая кромка Endcutting edge
Тип зуба
Tooth Type |
|
перевод |
Характеристики и область применения
Characteristics and scope of application |
Плоский торец центровым отверстием
Flat end with center hole |
с |
|
Вертикальное врезание невозможно. Наличие центрового отверстия служит для обеспечения повышенной точности при заточке инструмента
|
Плоский торец с режущим центром
Flat end with cutting center
|
|
|
Возможность вертикального врезания. |
№7 Хвостовик и шейка .Shank and neck
Type |
translation |
Characteristics and scope of application |
Standard(Straight shank) |
|
The most common type. |
Long shank |
|
It is used for milling stepped deep pockets and ledges |
Long neck |
|
It is used for milling deep pockets and ledges. |
Conical neck
|
|
It is used for milling deep grooves, foundry slopes. |
№8 Translate!
А.Монолитный инструмент
Монолитный инструмент изготовляют двумя способами.Первый способ заключается в том, что нужная форма инструмента в окончательномвиде формируется в специальной прессформе. Исходным материалом являетсямелкозернистый порошок с химическим составом, соответствующим определенной маркетвердого сплава. Затем полуфабрикаты подвергают двукратному спеканию. Еслиполученный инструмент имеет форму коронок, то его припаивают к державкам, азатем затачивают. Если инструмент насадной, то его затачивают и надевают насоответствующие оправки.
B.Конструктивно монолитные инструменты
Конструктивно монолитные инструменты выполняются в двухвариантах: цельными — из заготовки, получаемой методами порошковой металлургии( прямым прессованием и спеканием или окончательным спеканием обрабатываемой впластифицированном состоянии заготовки), и составными — когда цельнойизготовляется только коронка или головка, припаиваемая затем или механическизакрепляемая на державке.
Обработка монолитнымиинструментами осуществляется при обильной подаче смазочно-охлаждающихжидкостей ( СОЖ) или вовсе без них. Недостаточная подача СОЖ или перерывы в ееподаче могут значительно ухудшить работоспособность фрез и другого инструмента.Обработка пластмасс производится всухую или с воздуш -: ным охлаждением. Принарезании резьбы вручную хорошо зарекомендовала себя смесь парафина с солидоломв соотношении 1: 1, а при машинном нарезании — смесь его с маслом в той жевесовой пропорции
В. Сборный режущий инструмент
Торцевые фрезы |
End mills |
Концевые фрезы |
End mills |
Копирные фрезы |
Copier cutters |
Циркулярные фрезы |
Circular milling cutters |
Фрезы для уступов и пазов |
Cutters for ledges and grooves |
Дисковые фрезы |
Disc cutters |
Сборные сверла |
Prefabricated drills |
Инструмент из быстрорежущей стали |
High-speed steel tool |
Расточные головки |
Boring heads |
Токраные инструменты |
Current tools |
Инструмент для тонкого точения |
Fine turning tool |
Нарезание резьбы |
Threading |
Точение канавок под стопорные кольца |
Turning grooves for locking rings |
отрезание |
cutting |
Накатные инструменты Представленная информация была полезной? ДА 60.88% НЕТ 39.12% Проголосовало: 1544 |
Rolling |
прошивки |
Firmware Tools |
Заготовки резцов |
Blanks of incisors |
Токарные резцы |
Turning tools |
Навигатор для выбора режима резания |
Navigator for selecting the cutting mode |
сталь |
steel |
Серый чугун |
Grey cast iron |
Чмсло зубьев |
Chmslo teeth |
Фрезы для изготовление фасок |
Milling cutters for chamfering |
Угол установки |
Installation angle |
графит |
graphite |
Врезные фрезы |
Mortise cutters |
Большая пластина |
Large plate |
Малая пластина |
Small plate |
Черезвычайно износостойкий сорт |
Extremely wear-resistant grade |
Многослойное покрытие |
Multi-layer coating |
Инструментальные материалы для фрезирования |
Tool materials for milling |
Копирные и торцевые фрезы |
Carbon and end mills |
Затяжной винт |
Tightening screw |
Стопорный винт |
Locking screw |
Презиционная фреза с тороидальным торцом |
Composite milling cutter with a toroidal end face |
Сборные торцевые фрезы |
Prefabricated end mills |
Низкая глубина резания |
Low cutting depth |
Высочайшая скорость резания |
Highest cutting speed |
Короткое время обработки |
Short processing time |
Высокопроизводительная тангенциальная насадная фреза |
High-performance tangential attachment milling cutter |
С большим шагом зубьев |
With a large pitch of teeth |
С малым шагом зубьев |
With a small tooth pitch |
Оптимальная сила резания |
Optimal cutting force |
Максимальные обьемы обработки |
Maximum processing volumes |
Концевая фреза |
End mill |
Фреза для фаски |
Milling cutter for chamfering |
Циркулярная фрезерная система |
Circular milling system |
Режущие головки |
Cutting heads |
Дисковая фреза с буртиком |
Disk milling cutter with collar |
Трехсторонее резание |
Three-way cutting |
Сила зажатия при нагреве |
Clamping force when heated |
Центровочные сверла для станков |
Centering drills for machine tools |
Для гравирования |
For engraving |
Не для гравирования |
Not for engraving |
Надежность и точность без перезаточки |
Reliability and accuracy without rewinding |
Сверлильные коронки |
Drilling crowns |
Шаровая форсунка |
Ball nozzle |
Ступенчатое резание |
Step cutting |
Двузубая расточноая головка |
Two — pronged boring head |
Сборное сверло |
Prefabricated Drill bit |
Система микрометрических расточных головок |
System of micrometric boring heads |
переходники |
adapters |
Отправки с разьемом |
Dispatches with razem |
Отрезные инструменты |
Cutting tools |
Наружная резбьбовая державка |
External threaded holder |
Навинчиваемые резьбовые резцы |
Screw-on threaded cutters |
Держатель расточного резца |
Boring Cutter Holder |
Расточные резцы |
Boring cutters |
Расточная державка |
Boring holder |
Токарная державка |
Turning holder |
Копирное точение,растачивание |
Carbon turning,boring |
Снятие фасок |
Chamfering |
Канавочные резцы |
Groove cutters |
Резбовые резцы |
Chisel cutters |
№1 Translate it!
• 3. Зенкеры 4. Развертки 5. Метчики
• 7. Фрезы
№2 Perform thetranslation! Write down all the verbs from the text.Put them in 3 forms. Sortthe selected sentence by parts of speech. And write down all thetechnical vocabulary of the text.
The results of calculating the stress-strain state inreplaceable cutting inserts of assembly tools are presented, using the finiteelement method. In the calculation, the mechanical characteristics of the toolhard alloy were specified, the conditions for the interaction of thereplaceable cutting inserts with the drill body, the fastener elements, the forceloading was replaced by the specification of the boundary conditions. As aresult, a number of basic sizes of replaceable cutting inserts were built, withdifferent geometric parameters. A system of equations for the calculation ofcutting forces for drilling with prefabricated drills of different types hasbeen developed. To determine the influence of the shape of the plates on thestressed state, replaceable cutting inserts of different shapes were studied:trihedral, rhombic, square. A new form of replaceable high-strength cuttinginserts with an enlarged angle has been developed. To improve performance,the auxiliary cutting edge of the replaceable cutting insert is made in theform of an arc inscribed in a quarter of the length of the side of the polyhedron,while the radius of the curved cutting edge is equal to half the length of theside of the polyhedron.
№3 Translate thetext.Make up questions to the text. And write down all the technicalvocabulary of the text.
In the context of machining, a cutting tool or cutter istypically a hardened metal tool that is used to cut, shape, and remove materialfrom a workpiece by means of machining tools as well as abrasive tools by wayof shear deformation. The majority of these tools are designed exclusively formetals. There are several different types of single edge cutting tools that aremade from a variety of hardened metal alloys that are ground to a specificshape in order to perform a specific part of the turning process resulting in afinished machined part. Single edge cutting tools are used mainly in theturning operations performed by a lathe in which they vary in size as well asalloy composition depending on the size and the type of material being turned.These cutting tools are held stationary by what is known as a tool post whichis what manipulates the tools to cut the material into the desired shape.Single edge cutting tools are also the means of cutting material performed bymetal shaping machines and metal planing machines which removes material bymeans of one cuttingedge. Milling and drilling tools are often multipoint tools. Drilling isexclusively used to make holes in a workpiece. All drill bits have two cuttingedges that are ground into two equally tapered angles which cuts through thematerial by applying downward rotational force. Endmills or milling bits, whichalso cut material by rotational force. Although these tools are not made to putholes in a workpiece. They cut by horizontal shear deformation in which theworkpiece is brought into the tool as its rotating. This is known as the toolpath which is determined by the axis of the table that is holding the workpiecein place. This table is designed to accept a variety of vises and clampingtools so that it can move into the cutter at various angles and directionswhile the workpiece remains still. There are several different types ofendmills that perform a certain type of milling action.
Grinding stones are tools thatcontain several different cutting edges which encompasses the entirety of thestone. Unlike metallic cutting tools, these grinding stones never go dull. Infact the formation of cutting edges of metallic cutting tools are achieved bythe use of grinding wheels and other hard abrasives. There are severaldifferent types of grinding stone wheels that are used to grind severaldifferent types of metals. Although these stones are not metal, they need to beharder than the metal that they grind. In contrast to the grinding stone, ifthe hardness of the metal exceeds that of the stone, the metal will cut thestone. This is not ideal. [1] Each grain of abrasivefunctions as a microscopic single-point cutting edge (although of high negativerake angle), and shears a tiny chip.
Cutting tool materials must be harder than the material which is to be cut, and thetool must be able to withstand the heat and force generated in themetal-cutting process. Also, the tool must have a specific geometry, with clearance angles designed so that thecutting edge can contact the workpiece without the rest of the tool dragging onthe workpiece surface. The angle of the cutting face is also important, as isthe flute width, number of flutes orteeth, and margin size. In order to have a long workinglife, all of the above must beoptimized, plus the speeds and feeds at which the tool is run.
№4 Translate! Andwrite down all the technical vocabulary of the text.
Linear cutting tools include toolbits (single-point cuttingtools) and broaches. Rotary cutting toolsinclude drill bits, countersinks and counterbores, tapsand dies, reamers, and coldsaw blades. Other cuttingtools, such as bandsaw blades, hacksaw blades, and fly cutters, combine aspects of linearand rotary motion.
________________________________________________________________________________________________________________________________
№5 Translate! Andwrite down all the technical vocabulary of the text.
Cutting is one of the oldest arts practised in the stoneage, but the cutting of metals was not found possible until the 18th century,and its detailed study started about a hundred years ago.
Now in every machine-shop youmay find many machines for working metal parts, these cutting machines aregenerally called machine-tools and are extensively used in many branches ofengineering. Fundamentally all machine-tools remove metal and can be dividedinto the following categories:
1. Turning machines (lathes). 4. Milling machines.
2. Drilling machines. 5. Grinding machines.
3. Boring machines.
Machining of large-volume production parts is bestaccomplished by screw machines.
These machines can do turning, threading, facing, boring
and many other operations. Machining can producesymmetrical shapes with smooth surfaces and dimensional accuracies not generallyattainable by most fabrication methods.
Screw-machined parts are made from bar stock or tubing fedintermittently and automatically through rapidly rotating hollow spindles. Thecutting tools are held on turrets and tool slides convenient to the cuttinglocations. Operations are controlled by cams or linkages that position thework, feed the tools, hold them in position for the proper time, and thenretract the tools. Finished pieces are automatically separated from the rawstock and dropped into a container.
Bushings, bearings, nuts, bolts, studs, shafts and manyother simple and complex shapes are among the thousands of products produced onscrew machines. Screw machining is also used to finish shapes produced by otherforming and shaping processes.
Most materials and their alloyscan be machined — some with ease, others with difficulty. Machinabilityinvolves three factors: 1. Ease of chip removal. 2. Ease of obtaining a goodsurface finish. 3. Ease of obtaining good tool life.
№6. Find an analogueof the translation of sentences from the previous text
1.Винтовые обрабатываемых деталей изготавливаются из прутков или трубок кормили между mittently и автоматически с помощью быстро вращающегося полого шпинделя.
2. Обрабатываемость включает в себя три фактора: 1. Легкостьудаления стружки. 2. Простота получения хорошего качества поверхности. 3.Простота получения хорошей жизни инструмента.
3. Втулки, подшипники, гайки, болты, шпильки, валы и многиедругие простые и сложные фигуры среди тысяч продуктов, произведенных на винтмашины.
4. Эти машины могут сделать поворот, резьбы, напротив, расточные и многие другие операции.
5. По сути все станки удаления металла и могут быть разделены наследующие категории:
1. Станки токарные(токарные станки). 4. Фрезерные станки.
2. Сверлильные станки.5. Шлифовальные станки.
3. Бурильные машины.
№7. Specify the wayof word formation of the following words and translate them intoRussian:Укажите способ словообразования следующих слов и переведите их нарусский язык:
division, divisional, divisor,subdivision, subdivisible, hardness, harden, hardenable, hardenability,hardener.
№ 8 . Translatethe following phrases and sentences with the word specific usingthe specified variants of its meaning:Переведите следующие словосочетания ипредложения со словом “specific”, используя указанные варианты егозначения:
Особый, точный, конкретный,определенный, удельный (физ.)
With no specific aim
Specific orders
Specific statement
Specific gravity (weight)
Specific heat
You say your factory is inEngland; Can you be a bit more specific?
She gave us very specificinstructions.
There is a specific tool foreach job.
The money is to be used for aspecific purpose.
№9 Translatethe following sentences, paying attention to the conjunction either…
or…”:Переведитеследующие предложения, обратив внимание на союз “either… or…”:
1. Either nickel or tungsten are used to make steel stronger andharder.
2. Cutting tools are made of either hardened and tempered steel oralloy metals.
3. British tools were exported to either Europe or to the UnitedStates in spite of prohibiting exports.
4. These operations can be performed on either turning or drillingmachines.
№10. Define thefunction of infinitives in the third sentence of the first paragraph andtranslate them together with the words related to them. Определите функциюинфинитивов в третьем предложении первого абзаца и переведите их вместе сотносящимися к ним словам.
№11. Find in thefirst paragraph a subordinate determinative sentence with an unconnectedconnection and translate it together with the noun being defined Найдите впервом абзаце придаточное определительное предложение с бессоюзной связью ипереведите его вместе с определяемым существительным.
№12 .Translate the following sentences, paying attention to the non-union definitionof the subordinate clause to the main one:Переведите следующие предложения,обращая внимание на бессоюзное определение придаточного предложения к главному:
1. In every machine shopthere are many machine tools we can use for working metals.
2. Metals one can applyfor industrial purposes are called engineering metals.
3. The carbon contentsteel may contain is confined to certain limits.
4. The temperature ametal melts at is called its melting point.
5. Grey iron is weak andwill not stand great shock it can be subjected to.
№13. Analyze thefourth sentence of the first paragraph, determine the type of subordinateconditional sentence and translate the sentence into Russian.Проанализируйтечетвертое предложение первого абзаца, определите тип придаточного условногопредложения и переведите предложение на русский язык.
№14 . Writeout the predicates in the passive voice from the first and second paragraphs,which include a modal verb, and translate them together with the subjectsrelated to them.Выпишите из первого и второго абзацев сказуемые в страдательномзалоге, в составе которых есть модальный глагол, и переведите их вместе сотносящимися к ним подлежащими.
№ 15. Write out theparticiple I from the text, determine their functions and translate intoRussian together with the words related to it.Выпишите из текста причастие I,определите их функции и переведите на русский язык вместе с относящимися к немусловами.
№16. Analyze the verbforms with the ending -ed in the first sentences of the second and fourthparagraphs and translate them into Russian together with the words related tothem Проанализируйте глагольные формы с окончанием -ed в первыхпредложениях второго и четвертого абзацев и переведите их на русский языквместе с относящимися к ним словами.
№17. Translate thefollowing sentences, paying attention to the functions of the participle andanalyzing verb forms with the ending -ed Переведите следующие предложения,обращая внимание на функции причастия и анализируя глагольные формы сокончанием -ed:
a. A heating device – a heated device; an increasing speed – anincreased speed; a supporting unit – a supported unit; an alloying element – analloyed steel
b. 1. The lathe is a machine tool used for machining the surfacesof a workpiece.
2. Even in the past people used the lathe for different machiningoperations.
3. The first computers used thousands of separate electricalcomponents connected together with wires.
4. Power is another term used in a special technical sense inspeaking of machines.
5. Computers are machines designed to process electronicallyspecially prepared pieces of information.
6. The second industrial revolution marked also by the growingimportance of science-based industries provided power for factories.
c. 1. The amount of metal removed depended on the qualityof the cutter used.
2. The lathes used differed in designs and sizes.
3. The speed obtained on the diameter of the workpiece beingmachined.
4. The speed influenced by the workpiece diameter ranged from 1500to 1800 rev/min.
5. The mechanism referred to in the paper performed the majority ofrequired handling operations automatically.
6. The leading of the workpiece followed by its clamping wasperformed automatically.
№18.Determine the function of the pronoun it” at the beginning of the firstsentence of the fourth paragraph and translate it together with the wordsrelated to it.Определите функцию местоимения “it” в начале первогопредложения четвертого абзаца и переведите вместе с относящимися к немусловами.
№19 Analyze the lastsentence of the fourth paragraph, determine the function of the word
after”and translate the sentence into Russian.Проанализируйте последнее предложениечетвертого абзаца, определите функцию слова “after” и переведите предложениена русский язык.
№20 .Translate the text taking into account the completed tasks. Translate the firstparagraph in writing.Переведите текст с учетом выполненных заданий. Первыйабзац переведите письменно.
1. The cutting tool is that part of a machine tool which serves forremoving material from a revolving work. Cutting tools being used for variousmetal cutting operations include quite a wide range of shapes. The shape of thetool is known to depend upon a large number of factors such as the specificoperation the material to be cut and the material the tool is made of. Ifeither incorrect or faulty cutting tools had been used for metal-cuttingoperations, the quality of work would have become poor and cost would have beenhigher. That is why careful attention should be given to the cutting tools inany metal-cutting operation.
2. Cutting tools are made of hardened steel or alloy metals. All thecutting tools are adapted to perform certain work in the most efficient mannerand, accordingly, they may be subdivided into turning tools, boring tools,milling tools, etc. These tools having one effective cutting edge along whichexcess material from the workpiece is removed are known as single-point cuttingtools.
3.Other tools removing excessmaterial on two or more cutting edges simultaneously are known as multipointcutting tools. Each cutting tool consists of a shank for holding the tool inthe machine and a cutting edge for removing chips from the work.
4. It is known that cuttingtools used for longitudinal turning and subdivided into roughing tools andfinishing tools. Ranging tools are applied for roughing or removing theexcessive metal from the work. Such tools usually have a long cutting edge.Finishing tools are used after the work has been turned with a roughing tool togive accurate size and clean surface to the work being machined.
№21. Make anannotation of the text.Составьте аннотацию текста.
___________________________________________________________________________
are used for such technical processing
operations as cutting and latheturning of parts and work pieces made of various materials (metals, wood etc).
Lathes are suitable for thefollowing part processing types:
• Turningи boring of contoured, conical and cylindrical surfaces
• Trimming
• Threadcutting
• Endworking
• Holemaking operations: hole enlarging, hole reaming, drilling
• Roughcut
• Chamfering
ENCE GmbH offers a lot ofturning equipment which widens greatly the technological capabilities of lathes.
ENCE GmbH offers the followingrange of lathe machines:
• BenchLathes
• CombinationLathes
• HeavyDuty Lathes
• Large-SizeLathes
• CNCHeavy Duty Lathes
• Turning-and-BoringLathes
• CNCTurning-and-Boring Lathes
• Vertical CNC Double Column Turning—and—Boring Lathe
______________________________________________________________
Small and medium size machineswith manual control
Application: repairshops, schools etc.
Design Features:
• Adjustable bench lathe
• Operated by AC electric motor
• Machine operations: facing, drilling, boring, thread cutting
• Easy to handle
Standard Setincludes:
• 5 three-jaw chuck 10
• Stationary center MT3
• Morse cone sleeve
• Replaceable gears
• V-Belt
• Oil gun
• Taper-shank drill
• Tool box
Options
• Four-jaw chuck 5 and spacing plate
• Traveling rest
• Rotating center
• Steady rest
• Quick change tool holder
• Threading dial
• Spraying protective housing
• *Completely closed jacket of spraying protective housing Machinebed
Small and medium size machineswith manual control
Application: at smallplants, repair shops, schools, as well as in some separate branches ofprocessing industry and individual small batch production
Design Features:
• The unit consists of two parts: bench lathe and milling/ drillingpart
• The unit is designed for machining of external and internalcylinder and conical surfaces, cutting of both metric and inch threads,drilling and boring, surface or groove milling, and other mechanical machining
Design Features:
• Heat treated and ground bed shears
• Shifting to other thread type without gear change
• Foot brake for quick stop
• Inch button for easy gear clutch and spindle inching start-up
• One-piece cast iron base
• Main pole with protection devices increases safety level atmachine operation
• Spindle bore diameter — 80 mm
• One-piece cast iron base
• Heat-treated and ground (main) drive mechanisms
• Head stock (gears) oil-mist lubrication from oil bath by a pump
• Delivery pinion overload coupling with skirt
• Removable gap piece for big diameter wokpiece machining
• Easy thread cutting without gear replacement
• Hardened and ground bedways
• Weight bearing tailstock
• Hardened and ground gears
• Emergency stop button
• Removable gap
Multi-function compacthorizontal Turning Machines
Application: Widely usedin tool workshops and repair shops. Used for machining of small and medium-sizeworkpieces: shafts, sleeves, discs. Cutting of metric, inch, module, anddiametral pitch threads is possible.
Design Features:
Rapid traverse — one actuatinglever. Hardened guides — high wear resistance.
Design Features:
• Hardened and ground bedways
• Weight bearing tailstock
• Hardened and ground gears
• Emergency stop button Removablegap
Application:
The Turning Machines of thistype are one of the first ones in the equipment range of paper-andpulpindustry, glue roller production, technical service, rail way sphereapplication, molding machining, big valves, rollers used in the metallurgicalindustry etc.
Can be used both for rough andfinish machining of metal and non-metal workpieces, as well as end surface andinternal opening turning.
• Hardened and ground bed shears
• Auto feed on compound slides
• Hardened and ground gears
• Emergency stop button
• Major electrical components are Siemens
Application:
The Turning Machines of thistype are widely used in different areas of processing industry, such asbuilding-and-construction, consumer, textile, petrochemical industries, valveand roller manufacturing etc.
Design Features:
• High strength spindle assembly
• Increased speed and cutting capacity
Automatic high-accuracy machines
Application: processingof workpieces, iron-base alloys, non-ferrous metals, carbidic alloys andporcelain.
The machine makes both rough andfinish workpiece machining: cylindrical surface turning and boring, facing,bowing, grooving, thread cutting and drilling
Design Features:
• The main drive is driven by D. C motor through two stepsmechanism to reach speeds range for spindle. The spindle has an improved designand is supported by high-precise double-row short cylindrical rolling bearingswith adjustable radial clearance and has best supporting diameter and spanbecause of optimized design so as to improve its swiveling accuracy and staticand dynamic rigid
• Feed for CNC model is transmitted by A. C. servo motor.High-precise lead screw is adopted for transversal movement, toothed rack withhardened and ground spiral tooth. High-precision lead screw provides crossmovement, and the toothed rack with hardened and ground spiral teeth is incharge for carriage feed and quick movement. Ball screw is adopted forlongitudinal movement in 5000 mm, and by double pinion with allowanceeliminating-imported rack for over 5000 mm. For universal type, concentratedtransmission (by spindle) is adopted to get feed or threading
• CNC system: Siemens semi-closed loop control. Other CNC systemscan also be selected by customer’s requirements
According to customer’s demands,entire-closed loop control can be provided for the following: milling andboring, angle-dividing and feed for main spindle, grinding, cooling device aswell as the second carriage gearbox speed and its closed loop control device.
1.2.Воспомогательныйинструмент
Патроны |
Cartridges |
|
оправки |
mandrels |
|
Дополнительная оснастка |
Additional equipment |
|
Токарные патроны |
Turning chucks |
|
Быстросменные резцедержатели |
Quick-change tool holders |
|
VDI-держатели |
VDI holders |
|
Приводные головки |
Drive heads |
|
Токарные центры |
Turning centers |
|
цанги |
collet |
|
Резьбонарезные патроны |
Threaded cartridges |
|
Сверлильные патроны |
Drilling cartridges |
|
Переходные втулки |
Adapter bushings |
|
индикаторы |
indicators |
|
Приборы предварительной настройки и термозажима |
Pre-setting and thermal clamping devices |
|
Приборы для привязки |
Devices for binding |
|
Система базирования по нулевой точке |
Zero-point basing system |
|
Тиски для станков ЧПУ |
Vise for CNC machines |
|
Модульные тиски |
Modular vise |
|
Быстродействующие прижимы |
High-speed clamps |
|
Универсальные станочные приспособления |
Universal machine tools |
|
Плиты с постоянным магнитом |
Permanent Magnet Plates |
|
Короткие сверлильные патроны |
Short Drill chucks |
|
Быстросменный резьбонарезной патрон |
Quick-change threading chuck |
|
Универсальные тиски для станков с ЧПУ |
Universal vise for CNC machines |
|
Пары параллельных подкладок |
Pairs of parallel linings |
|
Балансировка воспомогательного инструмента |
Balancing the auxiliary tool |
|
Стандартная балансировка |
Standard balancing |
|
Без балансировки |
Without balancing |
|
Точная балансировка |
Precise balancing |
|
разбалансировка |
unbalancing |
|
Несимметричная форма патрона ( инструмента) |
Asymmetrical shape of the cartridge (tool) |
|
Центр тяжести ротора |
The center of gravity of the rotor |
|
Производственные допуски |
Production tolerances |
|
Цветовая маркировка |
Color marking |
|
Крепление инструмента |
Tool mounting |
|
Крепление заготовки |
Fixing the workpiece |
|
Многоцелевой обрабатывающий центр |
Multi-purpose processing center |
|
Токарный патрон |
Turning chuck |
|
Клино-реечный токарный патрон |
Wedge-rack turning chuck |
|
Специальные пренадлежности |
|
Special requirements |
Цанговый патрон |
|
Collet chuck |
Комбинированный оправки насадных фрез |
для |
Combined mandrels for attachment cutters |
Переходные втулки |
|
Adapter bushings |
Короткий сверлильный патрон |
|
Short Drill chuck |
Патрон с гидрозажимом |
|
Cartridge with hydraulic clamp |
Патрон с термохажимом |
|
Cartridge with thermal clamp |
удлинители |
|
extension cords |
№1 Translate thetext.Write down a list of technical words from the text.For the selected words,make a morphemic analysis of the word.
A chuck is a specialized type ofclamp used to hold an object with radial symmetry, especiallya cylinder. In a drill, a mill and a transmission, a chuck holds therotating tool; in a lathe, it holds the rotating workpiece.
Chucks commonly use jaws to holdthe tool or workpiece. The jaws (sometimes called dogs) are typicallyarranged in a radially symmetrical pattern like the points of a star. Jawed chucks may require a wrench—like device called a chuckkey to be tightened or loosened, but other jawed chucks may be tightened orloosened by hand force alone, offering convenience at theexpense of gripping force. Chucks on some lathes have jaws that moveindependently, allowing them to hold irregularly shaped objects. More complexdesigns might include specially shaped jaws, greater numbers of jaws, orquick-release mechanisms.
Instead of jaws, a chuck may usemagnetism, vacuum, or collets, which are flexible collars orsleeves that fit closely around the tool or workpiece and grip it whensqueezed.
№2 Translate the text.Make a list ofquestions for the text.Select and underline complex sentences
Aself-centering chuck, also known as a scroll
chuck,[1] uses dogs (usually called jaws),interconnected via a scroll gear (scroll plate), to hold onto a tool orworkpiece. Because they most often have three jaws, the term three-jaw chuckwithout other qualification is understood by machinists to mean aself-centering three-jaw chuck. The term universal chuck also refers tothis type. These chucks are best suited to grip circular or hexagonalcross-sections when very fast, reasonably accurate (±0.005 inch [0.125 mm] TIR) centering is desired.
Sometimes this type of chuck hasfour or six jaws instead of three. Four-jawed chucks are primarily useful forgripping square or octagon material, while six-jawed chucks hold thinwalledtubing and plastic materials with minimum distortion.
There are also independent-jaw(non-self-centering) chucks with three jaws, but they offer few advantages andare very rare.
There are hybrid self-centering chucks that haveadjustment screws that can be used to further improve the concentricity afterthe workpiece has been gripped by the scroll jaws. This feature is meant tocombine the speed and ease of the scroll plates self-centering with the run—out eliminating controllability of anindependent-jaw chuck. The most commonly used name for this type is a brandname, Set-Tru. To avoid undue genericization of that brand name,suggestions for a generic name have included exact-adjust.[citation needed]
Three-jaw chucks are often used on lathes and indexingheads.
№3 Put the verbs inbrackets in the required tense forms and translate the sentences into Russian.
1. Albert Einstein (to be) bomin Germany. When he was 12, he (to begin) his study mathematics and physics.Later he (to continue) his studies at the University. 2 Enstein (to present)his theory of relativity in 1905. His famous equation (to say) that energy (toequal) mass times the square of the speed of light. The great discovery (tosurprise) the scientists of the world. 3. The people of our great country (toproduce) many geniuses such as Lomonosov, Mendeleyev, Lobachevsky and others.Now our country (to have) a great number of brilliant scientists in all fieldsof science. Scientists (to make) researches in all fields of science ofknowledge. 4. Your experiment (not to give) good results until you (to change)the speed of die reaction. 5. Any square (to have) four right angles. 6. Thesquare of two (to be) four.
№4 Make up thesentences using the following Predicates.
1…. was boiling …, 2…. had beenlifted …, 3…. discovered…, 4. … will be delivered …, 5. … has beenworking …, 6. … has stopped….
№5 Translate thefollowing sentences, pay attention to the Predicates.
1. It takes the Earth 24 hours to rotate round itsaxis. 2. It takes 540 calories to change one gram of boiling water at 100 °Cinto steam at the same temperature. 3. It takes about 80 calories to change onegram of ice at 0 °C into water at the same temperature. 4. Nothing moves fasterthan light. It takes light only one second to move 300,000 kilometres. 5. Howlong does it take you to get home from the Institute? It took me 2 hours tomake the last experiment. 7. It will take you about 2 hours to go by air fromKiev to London.
№6 Translate!
Self-centering three-jaw chuckand key with one jaw removed and inverted showing the teeth that engage in thescroll plate. The scroll plate is rotated within the chuck body by the key, thescroll engages the teeth on the underside of the jaws which moves the threejaws in unison, to tighten or release the workpiece.
№7 Form nouns usingthe suffixes and translate them into Russian. -ity: equal, human, activ(e),relativ(e), productiv(e)
-ness: thick, black,great, rough -ancy: const(ant)
-ence: differ(ent),depend(ent), pres(ent)
-ency: effici(ent),depend(ent)
-age: us(e), pass, break,leak
№8 Translate thefollowing sentences, pay attention to the Predicates depending on the meaningof Subject.
1. New methods were developed asa result of this experimental work. 2. Very high speed developed when the jetengines appeared.3.New power plants without propellers were developed in orderto drive airplanes at sonic and supersonic speeds. 4. In this chapter equationsare developed for microscopic quantities. 5. Transistor oscillations can beused for the same purposes as vacuum tubes only frequency and temperaturelimitations are met. 6. Several general requirements should be met to match transistorstages in an amplifier.
№9 Translate the terms (Participle I + noun) intoRussian. Pattern: actuating mechanism механизм — какой? приводит вдействие
Русский термин: приводноймеханизм.
1. actuating pressure 5.reacting region
2. actuating cylinder 6.detecting element
3. translating system 7.adding element
4. halving circuit 8.alternating current
№10 Form theAdjectives using suffixes and translate them into Russian.
—ic: period, metr(e),atmospher(e)
—al: physic(s), natur(e),experiment, mathematics)
-able: valu(e), change,measur(e), compar(e)
-ant: import, resist
-ent: differ, insist
-ive: effect, act
-ful: help, wonder, use,power
-less: base, help, power, motion, weight.
№11 Translate thetext.Underline all simple sentences in the text.
A drill chuck is aspecialised self-centering, three-jaw chuck, usually with capacity of 0.5 in(13 mm) or less, and rarely greater than 1 in (25 mm), used to hold drill bits or other rotary tools. This type of chuck isused on tools ranging from professional equipment to inexpensive hand and powerdrills for domestic use.
Some high-precision chucks useball thrust bearings to reduce friction in the closing mechanism and maximizedrilling torque. One brand name for this type of chuck, which is oftengenericized in colloquial use although not in catalogs, is Super Chuck.
A pin chuck is aspecialized chuck designed to hold small drills (less than 1 mm (0.039 in) indiameter) that could not be held securely in a normal drill chuck. The drill isinserted into the pin chuck and tightened; the pin chuck has a shaft which isthen inserted into the larger drill chuck to hold the drill securely. Pinchucks are also used with high-speed rotary tools other than drills, such as die grinders and jig grinders.
Top: an assembled keyless chuck.This type of chuck is tightened by twisting the body using firm hand pressureonly. While convenient, this feature can cause the chuck to tighten too muchwhen high torque is applied. Bottom: the widely used keyedtype of drill chuck with its key. The arbor is shown separately to the right. Thesechucks require a toothed key to provide the necessary torque to tighten andloosen the jaws. When the key is turned its teeth mate with teeth on the chuck,turning an internal screw which in turn moves the threaded jaws in or out alonga tapered surface. The taper allows the jaws to clamp drillshanks of a range of diameters.The end view shows the three small jaws that slide within the body.
Two pin chucks. The top one isassembled, the lower one shows the body and nose cap assembled with the colletpiece below it.
№12 Translate thetext. Make up 5 questions to the text.
Independent four-jaw chuck, withthe jaws independently set. The key is used to adjust each jaw separately.
An older and larger 4 jaw chuck. Note how it is able togrip an irregularly cut piece of used metal. Though not found on small chucksit is common for larger chucks (the one in the second photo was made around1900 and is 24 in diameter) to have many of the features of a faceplate. The jaws are stepped on one side and fullheight for gripping on the other and are reversible. Generally the jaws areusable for holding either outside as shown here, or inside as in gripping theinside of a pipe.
On an independent-jaw chuck,each jaw can be moved independently. Because they most often have four jaws,the term four-jaw chuck without other qualification is understood bymachinists to mean a chuck with four independent jaws. The independence of thejaws makes these chucks ideal for (a) gripping non-circular cross sections and(b) gripping circular cross sections with extreme precision (when the last fewhundredths of a millimeter [or thousandths of an inch] of runout must bemanually eliminated). The non-self-centering action of the independent jawsmakes centering highly controllable (for an experienced user), but at theexpense of speed and ease. Four-jaw chucks are almost never used for toolholding. Four-jaw chucks can be found on lathes and indexing heads.
Self-centering chucks with fourjaws also can be obtained. Although these are often said to suffer from twodisadvantages: inability to hold hex stock, and poor gripping on stock which isoval, only the latter is true. Even with three jaw self centering chucks, workwhich is not of uniform section along the work (and which is not free of spiralor wind) should not be gripped, as the jaws can be strained and the accuracypermanently impaired.
Four-jaw chucks can easily holda workpiece eccentrically if eccentric features need to be machined.
№13Write out new words A spider is a simple,relatively inexpensive, limited-capability version of an independent-jaw chuck.It typically consists of a ring of metal with screw threads tapped radiallyinto it, in which screws (hex cap, socket hex cap, or set screws) serve asindependent jaws. Spiders can serve various purposes: Asauxiliary features that complement the main lathe chuck:
o To hold the bar or workpiece at the back end of the spindle boreand support it concentrically, so that it resists wobbling or whipping whilethe spindle is turning. Gun barrels and oil pipes are examples of workpiecesthat benefit.
o To hold the bar or workpiece at the tailstock end (thus servingas a steady rest) or following the tool(thus serving as a follower rest).
Inplace of the main lathe chuck (for particular workpieces that can benefit—forexample, in some gunsmithing work)
А) find the equivalentof a sentence from the text
Паук — это простая, относительнонедорогая версия патрона с ограниченными возможностями с независимой челюстью.
№14 . Translate thefollowing international words.
Radio, genius, human, priority,demonstrate, contribution, physical, chemical, university, laboratories,problem, electromagnetic, communication, operation, apparatus, progress,transmission, music, vision, signals, television, meeting, industry, period,centre, radar, telecontrol, telemetric systems, electronic microscopes.
№15 Translate thefollowing word combinations.
1.а deflecting pointer; 2. the deflection of rays; 3.to point the direction; 4. a point on the diagram; 5. a thermometer’s scale; 6.reading of the scale; 7. actual reading of the scale; 8. negative terminals; 9.connected with negative terminals; 10. to disturb the deception; 11. to disturbradio communication; 12. air disturbances; 13. a turning armature; 14. an ironarmature; 15. a magnetic coil; 16. through this distance; 17. through thefield; 18. turns of a coil.
№16 Make upsentences, using the following word groups: “for the most part” , “in excess of” , “ as a whole”.
№17 Forms the wordsusing the prefixes and translate them into Russian.
to construct, construction, to use, totake, to name, to create, to group, to equip, production
№18 Translate the text.Separate the selectedsentence into parts of speech.
Chuck with six jaws
1.For special purposes, chucksare available with six or eight jaws. These are usually of theselfcentering design, and may be built to very high standards of accuracy.However, it is a misconception that such chucks necessarily offer moreprecision in holding solid workpieces than conventional three-jawedself-centering chucks. Indeed, hot-rolled or other imperfectly round workpiecesmay teeter insecurely between opposing jaws of scroll chucks havingeven numbers of jaws, in the same manner that a four-legged stool teeters on arough floor while a three-legged stool never does. The primary purpose ofsix- and eight-jawed chucks is to hold thin-walled tubing with minimumdeformation. By having twice as many clamping points, a six-jaw chuckinduces less than half as much clamping distortion in a thin-walled workpiece,compared to a three-jawed chuck.
Two-jaw chucks areavailable and can be used with soft jaws (typically an aluminium alloy) that can bemachined to conform to a particular workpiece. It is a short conceptual leapfrom these to faceplates holding custom fixtures, wherein the part islocated against fixed stops and held there with toggle clamps or toe clamps.
2. Many chucks have
removable jaws (often the top part is removableleaving the base or master jaw assembled with the scroll), which allows theuser to replace them with new jaws, specialised jaws, or soft jaws. Soft jawsare made of soft materials such as soft (unhardened) metal, plastic, or wood.They can be machined as needed for particular setups. The typical interfacebetween the master jaw and the removable jaw is a matching pair of serratedsurfaces, which, once clamped by the mounting screws, cannot allow relative slippingbetween the two parts.
№19 Translate thefollowing sentences, pay attention to the different functions would”.
1.If the temperature of the liquid should beraised, a large supply of more swiftly moving molecules is provided. 2.Obviously, a flying machine should be stable. 3. It is necessary thatfuel lines should be protected against heat. 4. The thermonuclear reaction shouldnot be confused with the nuclear reaction such as takes place in the atombomb. 5. It should be noted that a multiple-step rocket always has agreater take-off mass than a single-step rocket. 6. A molecule of water is thesmallest possible particle of water. If we should divide the molecule weno longer have water.
№20 Translatethe following sentences, pay attention to the different functions“should.
1.Heat would be absorbed untilthe temperature of the absorbing body attains that of the heat. 2. Probably theearly users of telephones never dreamed that there would be a wirelesstelephone. 3. It would be useful to remember that the greater the vacuum, themore efficient the rocket becomes. 4. If the Earth stayed in one place of itsorbit, day and night would not change in length. 5. If a “short-circuit” occursat any place in a circuit, a very large current is caused to flow, and thiswould heat up the connecting wires. 6. The earliest experiments in flight withheavier-than-air machines were all based upon the conception, that result wouldbe obtained by imitating the motions of bird.
№21 Translate. Writeout and transcribe the new vocabulary according to the text.Make a crosswordpuzzle out of new words.
A collet, one type of chuck, is a sleevewith a (normally)
cylindrical inner surface and a conical outer surface. The colletcan be squeezed against a matching taper such that its inner surface contractsto a slightly smaller diameter, squeezing the tool or workpiece whose secureholding is desired. Most often this is achieved with a spring collet, made of springsteel, with one or more kerf cuts along its length to allow it to expand and contract. Analternative collet design is one that has several tapered steel blocks(essentially tapered gauge blocks) held in circular position (like the pointsof a star, or indeed the jaws of a jawed chuck) by a flexible binding medium(typically synthetic or natural rubber). The Jacobs Rubber-Flex brand is aname that most machinists would recognize for this type of collet chucksystem.
Regardless of the collet design,the operating principle is the same: squeeze the collet radially against thetool or workpiece to be held, resulting in high staticfriction. Under correct conditions,it holds quite securely. Almost all collet chucks achieve the radial squeezingmotion via moving one or more male-female pairs of tapered (conical) surfacesaxially, which produces the radial squeezing in a highly concentric manner.Depending on the collet design, it can be either pulled (via a threaded section at the rear of the collet) or pushed(via a threaded cap with a second taper) into a matching conical socket toachieve the clamping action. As the collet is forced into the tapered socket,the collet will contract, gripping the contents of the inner cylinder. (Theaxial movement of cones is not mandatory, however; a split bushing squeezedradially with a linear force—e.g., set screw, solenoid, spring clamp, pneumaticor hydraulic cylinder— achieves the same principle without the cones; butconcentricity can only be had to the extent that the bushings diameters areperfect for the particular object being held. Thus only in toolroom contexts,such as machine tool tooling creation and setup, is this common.)
One of the corollaries of theconical action is that collets may draw the work axially a slight amount asthey close. Collet chuck systems that make no provision to prevent this draw-inare often called draw-in collet chucks, in contrast to systems which circumventthis movement, usually by pushing the tapered closing ring toward the colletrather than pulling the collet into the ring. Such non-draw-in types are oftencalled dead-length or non-draw-in collet chucks.Draw-in is not always a problem, but avoiding it can be helpful on some workwhere failing to account for it might result in inaccuracy on part overalllength, shoulder lengths, etc.
Collets are most commonly foundon milling machines, lathes, woodrouters, precision grinders, and certain handheld power tools such as diegrinders and rotarytools. There are many differentsystems, common examples being the ER, 5C, and R8 systems.Collets can also be obtained to fit Morse or Brown and Sharpe taper sockets.
Typically collets offer higherlevels of precision and accuracy than self-centering chucks, and have ashorter setting up time than independent-jaw chucks. The penalty is that mostcollets can only accommodate a single size of workpiece. An exception is the ERcollet which typically has a working range of 1 mm (about 0.04 in).
Collets usually are made to hold cylindrical work, butare available to hold square, hexagonal or octagonal workpieces. While mostcollets are hardened, emergency collets are available that can bemachined to special sizes or shapes by the user. These collets can be obtainedin steel, brass, or nylon. Step collets are available that are machinable toallow holding of short workpieces that are larger than the capacity of normalcollets.
№22 Translate thefollowing sentences, pay attention to the different meanings: because— потому что, ибо ”, “because of — через, благодаря тому что, из-за”.
1. Because our sense of temperature is not veryreliable temperature measurements of our body must be made with accuratethermometers. 2. The energy, which an object has its motion because iscalled kinetic energy. 3. Because of the relative complexity of plasmaaccelerator configurations, experiments are needed to determine the design ofsuitable plasma drive devices.
4. The problem of powergeneration from fusion reactors is very difficult because of hedifficulty of containing plasma. 5. Because the neutron is neutral the positivecharge on the nucleus does not affect it.
№23 Translate.Compose questions to the text
Developed by Bosch in 1975 for hammer drills, the SDS Systemuses an SDS Shank which is a cylindricalshank with indentations to be held by the chuck.[2] A tool is inserted intothe chuck by pressing in, and is locked in place until a separate lock releaseis used. The rotary force is supplied through wedges that fit into two or threeopen grooves. The hammer action actually moves the bit up and down within thechuck since the bit is free to move a short distance. Two sprung balls fit intoclosed grooves, allowing movement whilst retaining the bit. SDS relies on atool having the same shank diameter as the chuck; there are four standardsizes:
SDS Quick
A 6 mm shank with two open grooves held by thedriving wedges and two closed grooves held by locking balls. This is the newestsize for the Bosch Uneo series and takes concrete drill up to 10 mm.[3]
SDS-Plus
A 10 mm shank with two open grooves held by thedriving wedges and two closed grooves held by locking balls. This is the mostcommon size and takes a hammer up to 4 kg. The wedges grip an area of 75 mm2(0.116 sq in) and the shank is inserted 40 mm into the chuck.
SDS-top
A 14 mm shank similar to SDS-plus, designed forhammers from 2 to 5 kg. The grip area is increased to 212 mm2 (0.329sq in) and the shank is inserted 70 mm. This size is uncommon.[4]
SDS-max
An 18 mm shank with three open grooves and lockingsegments rather than balls. It is designed for hammers over 5 kg. The wedgesgrip an area of 389 mm2 (0.603 sq in) and the shank is inserted 90mm.[5]
Many SDS drills have a rotation offsetting, which allows the drill to be used for chiselling. The name SDS comesfrom the German steck, dreh, sitzt (insert, twist, fits).German-speaking countries may use Spannen durch System (ClampingSystem), though Bosch uses Special Direct System for internationalpurposes.[6]
№24 Translate the following words, pay attention to themeaning ■ of prefixes “over-, inter-, under- ”. over- inter- under- to overestimate to intercharge tounderestimate to overcharge to interact to undercharge to overvalue to intermixto undervalue to overheat international to undergo to overcool interstellar tounderstand to overload the interchange
underground to overpay interconnection
№25 Translate thefollowing sentences, pay attention to the functions “to have, to be ”.
1. All modem direct-current dynamos have more than twopoles. 2. A number of ingenious methods have been devised for observing atomiccollisions. 3. In a actual gas not all atoms have the same speed, some travelmore slowly and others more rapidly than the average. 4. After bullet has cometo rest in the block, both block and bullet have the common velocity V. 5. Whenaircraft are in flight they have of course from time to time to report theirposition. 6. The Earth is supposed to have a shape similar to the shape of aball.
№26
Commercial production machiningnow makes use of increasingly advanced chucks which have not only indexablepositioning but also indexable clamping.[7] Both functions aretypically hydraulically controlled. The clamping is oftendone with each pair of jaws consisting of one fixed jaw and one movable jaw(hydraulically actuated), thematically similar to advanced milling vises. This method of clamping brings the high precision andrepeatability of such vises to a chucking application. Such chucks offer thecentering precision of traditional independent-jaw chucks with the chuckingspeed and ease of traditional three-jaw self-centering scroll chucks. They haveexpensive initial cost (compared with traditional chucks), but such initialcost pays for itself and then lowers ongoing marginal costs in commercialproduction-run environments.
It is also possible nowadays to build CNC chucks inwhich the position and clamping pressure of each jaw can be preciselycontrolled with CNC, via closed-loop positioning and load monitoring. Inessence, each jaw is one independent CNC axis, a machine slide with a leadscrew, and all four or six of them can act inconcert with each other. Although this idea is conceptually interesting, thesimpler chucking systems mentioned in the previous paragraph are probably amarketplace winner over this alternative for most applications, because theysupply the same capabilities via a simpler, less expensive solution.
Used for holding ferromagnetic workpieces, a magnetic chuck consistsof an accurately centred permanent magnet face. Electromagnets or permanent magnets are brought into contactwith fixed ferrous plates, or pole pieces, contained within a housing.These pole pieces are usually flush with the housing surface. The part(workpiece) to be held forms the closing of the magnetic loop or path, ontothose fixed plates, providing a secure anchor for the workpiece.
Commonly used for holding silicon wafersduring
lithography processes, an electrostatic chuck comprisesa metal base-plate and a thin dielectric layer; the metal base-plate ismaintained at a high-voltage relative to the wafer, and so an electrostaticforce clamps the wafer to it. Electrostatic chucks may have pins, or mesas, theheight of which is included in the reported dielectric thickness; a design by Sandia National Laboratory uses a patternedsilicon-dioxide dielectric to form the pins.[8]
A vacuum chuck is primarily used onnon-ferrous
materials, such as copper, bronze, aluminium,titanium, plastics, and stone. In a vacuum chuck, air is pumped from a cavitybehind the workpiece, and atmospheric pressure provides the holding force.Vacuum produces a hold down pressure of 14.7 psi (101 kPa) at sea level,decreasing at higher elevations where the atmospheric pressure is lower. Thedecrease in holding pressure is roughly 0.5 psi per 1000 above sea level.[citation needed]
№27 Translate thefollowing stable expressions into Russian.
And there we go …
The idea of it…
The case stands …
More to the point…
By all means…
None any too …
Can I help you …
This is it…
Certain as the rising sun …
№28 Read it.Make atext plan.Translate the text. Sort the highlighted sentences by composition.
He original forms of workholding on lathes werebetween-centers holding and ad hoc fastenings to the headstock spindle.The spike-style centers still used on wood lathes represent an ancient method.Ad hoc fastening methods in centuries past included anything from pinning withclenching or wedging; nailing; lashing with cords of leather or fiber; doggingdown (again involving pinning/wedging/clenching); or other types. Faceplateshave probably been around at least since the era of medieval clock-makers.
The Jacobs typechuck, with three converging splines or jaws, is perhaps the most usual design.This one is tightened with a key, but some types may be sufficiently tightenedby hand Tooling similar to todays chucks seems likely to have evolved fromfaceplate work, as workers using faceplates for repetitive work began toenvision types of clamps or dogs for the faceplate that could be opened andclosed in more convenient ways than repeated total disassembly and reassembly.A chock was originally just a lump of wood. However, by 1703 it could be… Chocks, belonging to the Screw-Mandrel. By 1807 the word hadchanged to the more familiar chuck: On the end of the spindle …is screwed … a universal Chuck for holding any kind of work.
In late 1818 or early 1819 the Society for theEncouragement of Arts, Manufactures and Commerce awarded its silver medal and10 guineas (£10.50 – equivalent to £814 in 2020[11]) to Mr. Alexander Bell fora three jaw lathe chuck:
The instrument can be screwedinto … the mandrel of a lathe, and has three studs projecting from its flatsurface, forming an equi-lateral triangle, and are capable of being movedequably to, or from, its centre.
It is not clear how they weremoved equably whether by a scroll or some other means. Later in1819 the same body awarded a further silver medal to Mr. T. Hack for a four jawchuck. In the United States SimonFairman (1792–1857) developed arecognisable modern scroll chuck as used on lathes.The patent refers to thetechnicalities of assembly, he does not claim invention of the scroll(convolute grooves). His son-in-law AustinF. Cushman (1830–1914) developed theideas and sold chucks through his business, Cushman Industries.
№ 29. Translatethe following words with the prefixes: semi-, trans-, non-.
semiconductor n semicircle n semimonocoque adjsemiautomatic adj non-conductor n non-essential adj non-standard adj nondurable adj transatlantic adj transoceanic adj transcontinental alj
30. Translate thefollowing word combinations and make up the sentences using them.
Industrial purposes, theapplication of electrical energy, the invention of electronic devices,considerably enlarged, has, it possible to solve, currents, the problem of obtaininghighfrequency, are the basis, of radioengineering, television, and otherbranches, of modem engineering.
№31 Translate thesentence.Fill in the table with the words from the sentence. The Jacobstype chuck, with three converging splines or jaws, is perhaps the most usualdesign. This one is tightened with a key, but some types may be sufficientlytightened by hand.
сходиться |
|
конструкция |
|
затягивать |
|
ключ |
|
№ 32 Insert wordsinto sentences.
Arthur Irving Jacobs (1858–1918)
At the ____of the 20th century, ArthurIrving Jacobs _______the modern drill chuck. _____bruising his knuckles on oneof the old-fashioned spanner adjusted drill chucks, he developed a chuck inwhich the jaws moved axially in inclined slots. His patent of 1902 details the mechanism.[ Theterm_____ clearly did not originate with him, but his new type of drill chucklong ago displaced any earlier types that lacked the angled jaw movement andouter sleeve now found on all common____ chucks. Start, developed, аfter,drillchuck, drill №33 Translate!
Lathe is still the most important machine-tool. Itproduces parts of circular cross-section by turning the workpiece on its axisand cutting its surface with a sharp stationary tool. The tool may be movedsideways to produce a cylindrical part and moved towards the workpiece tocontrol the depth of cut. Nowadays all lathes are power-driven by electricmotors. That allows continuous rotation of the workpiece at a variety ofspeeds. The modern lathe is driven by means of a headstock supporting a hollowspindle on accurate bearings and carrying or a faceplate either a chuck, towhich the workpiece is clamped. The movement of the tool, both along the lathebed and at right angle to it, can be accurately controlled, so enabling a partto be machined to close tolerances. Modern lathes are often under numericalcontrol.
Пояснения к тексту:
circular cross-section – круглое сечение a cylindrical part –цилиндрическая часть continuous rotation — непрерывное вращение
1. Найдите соответствующие ответы на вопрос и напишите их в тойпоследовательности, в которой заданы вопросы:
1. What parts can bemade with lathes?
2. How can the cuttingtool be moved on a lathe?
3. How is the workpiececlamped in a lathe?
4. Can we change thespeeds of workpiece rotation in a lathe?
5. What is numericalcontrol of machine tools used for?
А) The tool may be movedsideways
Б) It produces parts of circularcross-section
В) Driven by electric motorsallows continuous rotation of the workpiece at a variety of speeds
Г) А faceplate either a chuck,to which the workpiece is clamped.
Д) Сan be accurately controlled,so enabling a part to be machined to close tolerances.
2. Закончитепредложения, выбрав соответствующие варианты
1. Lathe is…
А) driven by means
Б) often under numerical control
С) the most important machine-tool
2. It produces…
А) parts of circularcross-section
Б) The movement of the tool
С) The tool may be moved sideways
3. Modern lathes are…
А) the most important machine-tool
Б) often under numerical control
С) driven by means of a headstock
3. Найдите в правой колонке русский эквиваленты английских слов и словосочетаний
1. the depth of cut |
А. поворачивать деталь вокруг ее оси |
2. circular cross-section |
Б. современный токарный станок |
3. Modern lathe |
С. цифровое управление |
4. numerical control |
Д. глубина резания |
5. turning the workpiece on its axis |
Е. детали круглого сечения |
№34 Translate!
Quenching is in a heat treatmentwhen metal at a high temperature is rapidly cooled by immersion water or oil.Quenching makes steel harder and more brittle, with small grains structure.
Tempering is a heat treatmentapplied to steel and certain alloys. Hardened steel after quenching from a hightemperature is too hard and brittle for many applications and is also brittle.Tempering, that is re-heating to an intermediate temperature and coolingslowly, reduces this hardness and brittleness. Tempering temperatures depend onthe composition of the steel but are frequently between 100 and 650 °C. Highertemperatures usually give a softer, tougher product. The colour of the oxidefilm produced on the surface of the heated metal often serves as the indicatorof its temperature.
Annealing is a heat treatment inwhich a material at high temperature is cooled slowly. After cooling the metalagain becomes malleable and ductile (capable of being bent many times withoutcracking).
All these methods of steel heat treatment are used toobtain steels with certain mechanical properties for certain needs. •
Пояснения к тексту: annealing — обжигание • steel heattreatment — стальная термическая обработка ductile — гибкий
1. Найдите соответствующие ответы на вопрос и напишите их в тойпоследовательности, в которой заданы вопросы:
What can be done toobtain harder steel?
А) Tempering is a heat treatmentapplied to steel and certain alloy
Б) Quenching makes steel harderand more brittle, with small grains structure
В) Higher temperatures usually give asofter, tougher product What makes steel more soft and tough?
А) Higher temperatures usuallygive a softer, tougher product
Б) Quenching makes steel harderand more brittle, with small grains structure
В). Annealing is a heat treatment inwhich a material at high temperature is cooled slowly What makes steel moremalleable and ductile?
А) Annealing is a heat treatmentin which a material at high temperature is cooled slowly
Б) Higher temperatures usuallygive a softer, tougher productс)
В) Quenching makes steel harderand more brittle, with small grains structure
What can serve as theindicator of metal temperature while heating it?
А) Tempering is a heat treatmentapplied to steel and certain alloys
Б) . Hardened steel afterquenching from a high temperature is too hard and brittle for many applicationsand is also brittle
В) The colour of the oxide filmproduced on the surface of the heated metal often serves as the indicator ofits temperature.
What are the methodsof steel heat treatment used for?
А) All these methods of steelheat treatment are used to obtain steels with certain mechanical properties forcertain needs. •
Б) Annealing is a heat treatmentin which a material at high temperature is cooled slowly
В) Higher temperatures usuallygive a softer, tougher product
2. Закончитепредложения, выбрав соответствующие варианты
Quenching is…
А) rapidly cooled by immersion
Б) a heat treatment when metalat a high temperature is rapidly cooled by immersion in water or oil.
С) a heat treatment in which a material at hightemperature is cooled slowly
Tempering is…
А) a heat treatment in which amaterial at high temperature is cooled slowly
Б) re-heating to an intermediatetemperature and cooling slowly, reduces this hardness and brittleness.
В) a heat treatment applied to steel and certain alloys
Annealing is…
А) too hard and brittle for manyapplications and is also brittle
Б) a heat treatment in which amaterial at high temperature is cooled slowly
В) rapidly cooled by immersion water or oil.
3.Найдите в правой колонке русский эквиваленты английских слов и
словосочетаний
1. высокая температура |
А. small grains structure |
2. индикатор температуры |
Б. cooling |
3 .охлаждение |
С high temperature |
4.мелкозернистая структура |
Д. indicator of temperature. |
5. обработка |
Е. treatment |
№35 Insert themissing word combinations.Translate!
__________standards are used tostandardize the definitions, requirements, and test methods used for theperformance evaluation of chucks. Selection of the standard to be used is anagreement between the supplier and the user and has some significance in_____________.In the United States, ASME has developed the B5.60Standard entitled Workholding Chucks: JawType Chucks, which establishesrequirements and methods for specifying and testing the performance____________used primarily in turning operations.
National andinternational
of workholdingchucks the design of the chuck
№36 Fill in thesentences with the words from the box
elatives son daughter wifehusband parents brother-in-law,sister-in-law nephew niece grandsongranddaughter
All the people here are _________.
2. Luke is Dave and Maggie’s _______.
3. Karen is Dave and Maggie’s ________.
4. Maggie is Dave’s ________. 5. Dave is Maggie’s ________.
6.
Elsie and Alf are Maggie’s_______.
7. Daveis Paul’s _______.
8. Jane is Maggie’s _______. 9. James is Maggie’s _______. 10. Karenis P aul’s ______.
11. Luke is Elsie’s______.
12. Jessica is Elsie’s_____
1.3Измерительный инструмент
Штангельциркуль цеховой |
Caliper shop |
Штангельциркуль цеховой облегченная конструкция |
Caliper workshop lightweight design |
микрометр |
micrometer |
Микрометр с цифровым индикаторм |
Micrometer with digital indicator |
Микрометрвнутромер с цифровым отсчетным устройством |
Micrometer with digital readout device |
Керамическая презиционная измерительная стойка |
Ceramic Positional measuring stand |
Штангенрейсмус |
Shtangenreysmas |
Цифровые штангенрейсмусы |
Digital shtangenreysmas |
Рейсмас |
Reysmas |
рулетка |
roulette |
Рулетка с магнитом |
Roulette with a magnet |
Лазерные дальномеры |
Laser rangefinders |
Ручной светодиодный стробоскоп |
Manual LED Strobe Light |
Индикатор напряжения |
Voltage indicator |
Цифровой динамометрический прибор |
Digital dynamometer device |
Набор для контроля штангенциркулей |
Caliper Control Kit |
Лупа с подсветкой |
Magnifier with backlight |
Mantisс гибким штативом |
Mantis with flexible tripod |
Светодиод Lynx |
Lynx LED |
Измерительный видиомикроскоп CNC |
Measuring video Microscope CNC |
Цифровой увеличительный прибор |
Digital magnifying device |
Магнитный сферический стол |
Magnetic Spherical table |
Гибкий эндоскоп |
Flexible Endoscope |
Ультразвуковой измерительный прибор |
Ultrasonic measuring device |
высотомер |
altimeter |
Штангинглубинометры |
Shtangenglubinometers |
Поверочные плиты |
Calibration plates |
призма |
prism |
стенд |
stand |
угольник |
square |
углометр |
angle meter |
Разметочный инструмент |
Marking tool |
уровень |
level |
рулетка |
roulette |
дальномер |
rangefinder |
хронометр |
chronometer |
весы |
scales |
тахометр |
tachometer |
Индикатор напряжения |
Voltage indicator |
№1 Translate the textinto Russian.Write down the main information in the text.Compose questions tothe text.
Micrometers (otherwise known asmicrometer screw gauges) are essential measurement tools used by mechanicalengineers, machinists and workers in other technical trades. They enableworkers to take extremely fine measurements, which may be displayed in eitherimperial or metric formats.
Micrometers allow for a greaterdegree of measuring accuracy than alternative tools, such as dial calipers andvernier calipers. They are available in digital, dial, and vernier styles. Theterm micrometer can be traced back to neoclassical Greece and literallytranslates as ‘small measure.’
Different types of micrometershave measuring ranges of between 25mm and 1 inch. This translates to theincremental metric measurements of 0-25mm, 25-50mm, 50-75mm and so on. Theimperial versions are equal to 0-1 inches, 1-2 inches, 2-3 inches etc. Boxed micrometersets can also be used for the purpose of taking micrometer readings across awide range of sizes.
In order to understand how amicrometer works, you should first consider the key components of the tool.Analysis of the components should also further your understanding of how toread a micrometer.
Micrometer frames are c-shapedand ensure the optimum positioning of the anvil and barrel. Frames may take avariety of shapes and sizes, allowing for desirable functionality of themicrometer. The hub-shaped frame is ideal for taking highly accuratemeasurements in confined spaces.
The micrometer anvil should be noticeably shiny. Itshould ensure that the spindle gravitates towards the object, which is firmlysecured. The anvil will be kept in consistent contact with the part and maychip unless a high level of care is taken. Quality models typically comecomplete with carbide-tipped micrometer anvils, which allow for an extendedtool-life.
The round micrometer sleeve orbarrel is kept securely in place and features the linear scale. It is alsoquite common for vernier markings to be found on this part of the micrometer.This scale allows highly accurate measurements to be taken in degrees of .0001.
The spindle micrometer lockingnut is a particularly helpful feature when it comes to maintaining awareness ofthe measurement and securing the spindle for small lot gauging. Somemicrometers come complete with lock nuts, while others have locking levers.Where possible, it is advisable to choose the locking lever variety due to therelative ease of use and maintenance.
Situated next to the measuring faces, the micrometerspindle is projected towards the anvil as a direct result of contact with thethimble.
You should gently apply pressure from the thumb in orderto turn the micrometer thimble. This part features graduated markings, whichshould be easy to read.
The micrometer ratchet stop can be found on the end of thehandle and it restricts the amount of pressure by enabling movement at acalibrated torque.
Micrometers feature a calibratedscrew, or thread, which is located within the spindle and allows for thedevices exceptional levels of measuring accuracy. The screw within themicrometer is used for the conversion of particularly small distances for measurement.The spindle can be moved by turning the ratchet knob or thimble until there islight contact between the spindle and anvil. Each 360-degree turn of thespindle has the effect of adjusting the space between the measuring displays by0.05 in metric and 0.025 inches in imperial.
The thread pitch of the needlehas a direct bearing on the level of measuring precision. The spindle ismachine-screwed to a very high level of accuracy, with the object beingmeasured positioned directly between the spindle and anvil. Some micrometersfeature differential screws, which allow for particularly great levels ofmeasuring accuracy.
It is highly important tomaintain the stability of any object that you are measuring with a micrometer.The object should be kept parallel to the anvils and a consistent level ofpressure should be applied when taking the measurement.
The integrated ratchet thimblewill ensure a high level of measuring accuracy, with this key part functioningas an integrated torque wrench. The process should continue with the turning ofthe ratchet handle until a repeated clicking is heard. This will provide theassurance of taking the measurement with a consistent level of torque.
Digital micrometers featureelectrical circuits, which allow for digital measurement and exceptionallyaccurate readings. The measurement will be displayed clearly on the LCD screen.
Micrometers are speciallydesigned for the measurement of very small objects. They allow for the highlyprecise measurement of any item that fits between the anvil and spindle.Standard types of micrometers can be used for the fine measurement of itemsunder one inch in length, depth, and thickness. However, there are someadvanced models that allow more precise measurements to be taken. There is alsothe option of investing in anvil micrometers for the measurement of diverselyshaped and sized objects. Portability, ease of use, and measuring consistencyare just a few of the key micrometer advantages.
There are various different types
of micrometer available, eachsuited to varying uses and applications. Outside micrometers are one of themost widely used varieties, but inside and depth micrometers are alternativeswhich may be more appropriate for use in certain scenarios. Below are some ofthe most common types of micrometers:
Ball micrometers havespherical anvils. They are used for purposes such as measuring the thickness ofwalls and establishing the distances between holes and edges. As opposed totube micrometers, the ball variety can be used to correctly identify themeasurement of alternative rounded surfaces.
Integrated with decoders for theeffective identification of distance, these micrometers present measurements ina digital format.
This type of micrometer comescomplete with matching narrow tips, or blades.They are particularly helpfulwhen it comes to the measurement of specifically shaped objects, such as thosewith O-ring grooves.
Designed to measure the thickness of tubes, tubemicrometers feature cylindrical anvils which are located perpendicular to thespindle. They allow for quick and accurate measurements when compared withalternative tools.
These come complete with interchangeable anvils, whichmay be flat, spherical, spline, disk, blade, point, or knife edge. You may beexpected to use universal micrometers featuring modular components, which allowfor outside, mic depth, or alternative functionality.
Otherwise known as the thread mic, this tool features aspecially designed set of thread-shaped tips for successful identification ofthe screw thread diameter.
Particularly well suited to measuring the
thickness of tubes, micrometerlimit mics come complete with two anvils and two spindles, functioning aseffective snap gauges. The gaps correspond directly to the upper and lowertolerance levels.
Commonly featuring a three-anvilhead in combination with a solid base, bore micrometers are ideally suited tothe accurate measurement of inside diameters. They are particularly helpfulwhen it comes to the measurement of objects situated around machine fluids andcoolants.
Bench micrometers offerextremely high levels of accuracy and are typically used during workplaceinspections. They allow for measurement up to somewhere in the region of 20millionths of an inch, with a repeatability of around a quarter of amillimetre.
Purpose-made for external measurement, V
micrometers come complete withsmall V-blocks for the anvil. They are ideally suited to the measurement ofcircle diameter, with equidistant separation of three points. This allows forthe effective measurement of three-flute end-mills and twist drills.
Micrometers are the ideal toolfor the measurement of cylindrical and spherical shaped objects. In order touse a micrometer, you should follow these steps:
1. Taketime to acquaint yourself with the main technical terms
2. Cleanthe micrometer, using a soft cloth to remove any marks and debris from betweenthe anvil and spindle
3. Beginby positioning the item being measured next to the anvil. It is important tokeep the object stable and avoid any scratching. You may control the micrometerwith your free hand, or alternatively, there is the option of using astationary vise, leaving both of your hands free for control of the micrometer
4. Spinthe ratchet anti-clockwise, ensuring that the 0 mark on the thimble ispositioned in accordance with the sleeve scale. Keep twisting until the spindleis within close contact of the object; three clicks is a good guide
5. Thethimble lock should be applied while the micrometer is within close proximityof the object. It should be possible to adjust the spindle as required. Onceyou are confident that the micrometer has fulfilled its function you can removethe object, taking care to avoid scratching the anvil and spindle surfaces
6. Finally,record the reading, ensuring that the spindle is kept stable
The following sections will giveyou more information on how to read specific types of micrometers:
When using a metric micrometer, It is necessary toacquaint yourself with the number scales that are displayed on the micrometerthimbles. It is common for the top line of the sleeve to feature millimetres,with the line below that featuring half millimetres.
The reading of the metricmicrometer should begin with recording the number of millimetres. An initialreading of 7 would correspond to 7mm. Each half mark on the thimble should betaken into account. This means carefully reading the lower bar and correctlyidentifying the corresponding number of 0.01mm.
Using a micrometer integratedwith the vernier scale, the reading should be taken from the sleeve index line.This allows for precise readings, within 0.001mm. The initial reading should betaken from the sleeve. The measurements are likely to be featured in intervalsof 0.25 millimetres or 0.025 inches.
The next step is to take thereading from the thimble. These measurements are likely to be featured in 0.1millimetre or 0.01-inch intervals. The final reading should be taken from thevernier scale, which you will find on the sleeve, directly adjacent to thefirst set of graduations.
The vernier micrometer readingis displayed in the format of 0.001 mm or 0.0001 inches, establishing the sizeof the object with extreme accuracy.
You should be aware thatfluctuations in temperature are likely to adversely affect the micrometerreading. Remember not to keep your micrometer in your pocket or within aworking environment with excessive heat levels.
The spindle of an imperial micrometer features graduated levelsof 40 threads per inch. Each turn results in movement of the spindle around anaxis of 0.0025 inches, which equates to the area between adjacent graduationson the sleeve.
There are 25 graduations on the thimble, meaning that themeasurements can be divided the corresponding number of times. The visiblereading corresponds directly to the number of whole divisions that are featuredon the sleeve scale, multiplied by 25. This means that the resulting diameteris displayed in thousandths of an inch.
This section details how toconvert your micrometer result into another measurement unit.
The quickest and easiest way toconvert micrometers (um) to millimetres is to divide by 1000. An alternativemethod is to move the decimal point three units to the left of the originalfigure.
There are 25,400 micrometers toevery inch, with 1 metre being equivalent to 1,000,000 micrometers. You shouldalso be aware that each micrometer equals 3.9×10e-5 (with e meaning to thepower of).
1um is equivalent to 0.0001cm (otherwise writtenas10e-4).
To make sure that your micrometer returns accurate data,you will need to ensure that your tool is kept calibrated.
Standard one-inch micrometershave readout divisions of 0.001 inch and an accuracy level of ±0.0001 inch.However, you must ensure that both the micrometer and the object being measuredare at room temperature for this high level of accuracy.
The micrometer reading test willinvolve the measurement of guide blocks in order to ascertain the desirableaccuracy. If such a gauge block is known to be 0.75000 ±0.00005inch then themicrometer should give a reading of 0.7500 inch. If the correspondingmeasurement is 0.7503 or more, then the micrometer will be deemed to be out ofcalibration.
If you want to avoid such calibration issues then youmust take an exceptional level of care, carefully cleaning, using, and storingthe micrometer for continued use. It might be necessary to perform micrometeradjustment and recalibration in some instances. However, adjustment won’t besufficient when it comes to correcting issues such as the micrometer beingmisshapen or of the incorrect size. Repair will be necessary for suchinstances.
The following steps explain howto calibrate a micrometer and adjust it to zero.
• Before proceeding to calibration, it is necessary to ensure thatthe tool is working effectively and that there aren’t any binding or relatedissues. You should clean the anvils and make sure that the reading is set tozero
• The next step will be to check the micrometer at a range of testpoints using gauge blocks or alternative standards with high levels ofaccuracy. A variety of readings should be taken at each test point. Thetolerance level of the particular micrometer should be taken into account whenwriting down the readings
• It is highly likely that your micrometer features a small pinspanner. This should allow for the turning of the sleeve in relation to thebarrel, ensuring the optimum repositioning of the zero line in relation to thethimble markings
• You can expect to find a small hole in the sleeve, designed foracceptance of the spanner’s pin. In following this calibration process, youwill have the assurance of avoiding the non-zero error, which may otherwiseoccur when the jaws are shut. You are advised to repeat the zeroing process afew times for the assurance of micrometer accuracy
If the zero mark on the thimble does not correspond withthe datum line on the main scale then there will be a zero error. The readingon the main scale should also equal zero.
The micron is a measurement of one-millionth of a metre,while the micrometer is a measuring tool featuring a calibrated screw.
Micrometer accuracy may be considered in relation to twokey factors — the accuracy of the screw thread (or digital scale), and anyprocess errors. The expected accuracy of a micrometer as established using theVernier scale is 0.01mm.
Micrometers and Vernier calipers are both commonly used toestablish the sizes of different objects. However, there is some contrastbetween the efficiency and usage of each of these tools. Calipers might be usedto establish physical dimensions, interior measurements, exterior measurementsand depths. However, micrometers are generally used for more specific purposessuch as measuring exterior or inside dimensions. The expected accuracy ofVernier calipers is typically between ±0.001, with the accuracy of micrometersgenerally being ±0.00005. For more information, check out our complete guide to calipers.
The least count of a manually operated micrometer is0.01mm. The least count of a digital micrometer is 0.001mm.
The micrometer symbol as used by the InternationalBureau of Weights and Measures is μm. The micrometer is an SI derived unit oflength which equals 1×10−6 metre (SI standard prefix micro- =10−6), equivalent to one-millionth of a metre or one-thousandth of amillimetre.
1 micro is equivalent to 1,000nanos.
1.4.Шлифовальный интсрумент
Слесарные напильники |
|
Специальные напильники |
special files |
Напильники для заточки пил |
saw doctor |
рашпили |
|
напильный |
filed |
рифленый |
fluted |
Алмазные напильники |
Diamond files |
Ручки для напильников |
File handles |
Твердосплавные HSS-борфрезы |
Carbide HSS burrs |
Гравировальные борфрезы |
Engraving burrs |
Алмазная головка |
Diamond head |
Шлифовальная головка |
grinding head |
Полировочная головка |
polishing head |
Абразивные ленты |
Abrasive belts |
наконечники |
tips |
Нетканные материалы |
Nonwovens |
бруски |
bars |
холст |
canvas |
Обдирочные круги |
Roughing wheels |
Алмазные круги |
diamond circles |
Волокнистые круги |
fibrous circles |
Лепестковые круги |
petal circles |
Шлифовальные круги |
grinding wheels |
Полировочный инструмент |
polishing tool |
Технические машинные кордщетки |
Technical machine brushes |
Ручные полотна |
Handmade canvases |
Ножовочные полотна |
Hacksaw blades |
Сабельные полотна |
Saber blades |
Коронки по металлу |
Crowns for metal |
Дисковые пилы по дереву |
Circular saws for wood |
Ручные пилы |
Hand saws |
Набор напильников универсальный |
Universal file set |
Абразивная шкурка с расширенным диапазоном размеров зерна |
Abrasive paper with extended grit size range |
Керамическое зерно |
ceramic grain |
Шлифовальные тарелки |
Sanding pads |
Цилиндрическая щетка для удаления заусенцев из проволоки |
Cylindrical wire deburring brush |
Трубные щетки с хвостиком |
Tube brushes with tail |
Алмазный отрезной диск |
Diamond cutting disc |
Малогабаритное борфрезы |
Small-sized burrs |
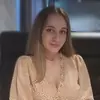