Трехсекционный бак для нагрева моющего раствора представляет собой прямоугольную емкость, внутри которой смонтирован змеевик подачи пара для нагрева моющего раствора. Температура моющего раствора в баке в случае парового или электрического нагрева контролируется независимыми регуляторами температуры. Для уменьшения тепловых потерь и предотвращения ожогов обслуживающего персонала бак снабжен теплоизолирующими экранами.
Автономная система подготовки моющего раствора (тип 1) состоит из трехсекционного бака для нагрева моющего раствора, высоконапорного электронасосного агрегата с насосом подпора, труб обвязки для подачи моющего раствора в форсунки камеры мойки и системы регенерации моющего раствора. Вода, скопившаяся в поддоне камеры мойки, по коллектору поступает в бак, который установлен ниже уровня пола участка.
Классификация видов способов очистки вагонов и их узлов
При ремонте вагонов используются следующие виды очистки:
Сухая очистка – используются специализированные вагоноуборочные машины, механические щетки, скребки, сжатый воздух, песко-дробеструйные и дробеметные установки .
|
|
Обмывка вагонов и их узлов, в том числе:
– водоструйная очистка без применения моющих растворов – используются водопроводные сети и брандспойты .
– гидродинамическая очистка с применением моющих растворов и без растворов – используются универсальные и специализированные вагономоечные машины и комплексы .
– пароводоструйная очистка с применением моющих растворов и без растворов – используются промывочно – пропарочные станции различных конструкций .
Выбор способа очистки зависит от вида загрязнений, степени воздействия очищающей среды на материал поверхности, размеров и формы изделий, наличия оборудования, санитарно-гигиенических, экологических, экономических и иных требований.
Способы очистки можно классифицировать следующим образом:
1. Механический способ – используют средства механического воздействия, а также силу струи сжатого воздуха, воды, пара, песка, дроби и т.п.
Механическая очистка может производиться ручным и механизированным методами.
При ручном методе очистку выполняют различными скребками, металлическими щетками, шлифовальными шкурками, ветошью и др.
При механизированном методе очистки используют переносные пневматические или электрические машинки, иногда с гибкими валами, и стационарные шлифовально-полировальные станки, где рабочим инструментом являются металлические дисковые и торцовые щетки, шарошки, шлифовальные круги и иглофрезы. Для очистки от окалины крупных деталей используют цепи, закрепленные на вращающихся валах очистных машин.
|
|
Дробеструйную (пневмоабразивную) очистку выполняют с помощью дробеструйных аппаратов. В этом случае поверхность обрабатывают металлической дробью или другими абразивными материалами. Для обработки применяют стальную или чугунную дробь с острыми гранями размером 0,8-2,5 мм в зависимости от диаметра насадки. Используют также металлический песок, измельченный гранит, зерна корунда, стеклянные шарики и др.
К механическому способу относятся:
— гидродинамическая очистка вагонов и их частей, которую выполняют водой под давлением (5 – 15 МПа) с помощью брандспойтов или мониторных (гидромониторных) универсальных и специализированных вагономоечных машин и комплексов. Пароводоструйную очистку поверхности выполняют парогидравлической струей температурой 90-100°С под давлением 0,5-2,0 МПа с помощью специальных установок.
— виброабразивная очистка – производится путем погружения деталей в жидкую среду в специальных установках, которым придаются колебательные движения. Очистка происходит под влиянием вибрации. Для этого метода очистки могут использоваться ультразвуковые установки .
— шлифование и полирование –поверхности крупных деталей очищают абразивными кругами на шлифовальных станках или механизированным переносным инструментом и пневматическими зубилами. Метод используется при подготовке поверхности детали, например под гальванические или лакокрасочные антикоррозионные покрытия. Шлифование выполняют эластичными войлочными или фетровыми кругами с нанесением на их рабочие поверхности шлифовальных порошков, а для полирования используют мягкие эластичные круги из тонкошерстного войлока, сукна, фланели и других мягких тканей с применением полировальных паст.
2. Физико-химический способ – основан на использовании активных моющих растворов и широко применяется в струйных и мониторных моечных машинах в сочетании с методомгидродинамической очистки. Может использоваться как самостоятельный метод очистки в погружных моечных машинах, выварочных и моечных ваннах, в ваннах с использованием ультразвука или электролита.
Устройства сухой очистки вагонов и их узлов
При подготовке вагонов и их узлов к ремонту проводят сухую очистку от остатков перевозимых грузов, мусора, отслоений лакокрасочных покрытий, пыли, грязи с использованием различного механического оборудования, скребков, устройств пневмообдувки, дробеструйной обработки и т.п.
Уборочная машина для сухой очистки внутренних поверхностей кузова от остатков перевозимых грузов показана на рисунке 1.
Заборное устройство машины выполнено в виде ковшового элеватора с подгребающим шнеком ленточного типа, а ходовая часть – в виде гусеничной тележки. Механизм подъема заборного устройства имеет гидравлический привод. Управляется машина дистанционно.
1 – горизонтальная щетка . 2 – вертикальная щетка . 3 – подгребной шнек .
4 – транспортер элеватора . 5 – фара . 6 – пульт управления . 7 – разгружающий бункер . 8 –редуктор . 9 – кабель . 10 – электродвигатель . 11 – гусеничная тележка . 12 – механизм подъёма щеток
Рисунок 4.2 – Уборочная машина
Работа уборочной машины осуществляется в определенной последовательности. С платформы (эстакады), уровень пола которой совпадает с уровнем пола крытого вагона, машина щетками вперед перемещается в дверной проем вагона и разворачивается в требуемую сторону. Приводной электрокабель с помощью натяжного устройства постоянно находится в подвешенном состоянии. Вначале очищаются стены и поверхность пола около стен.
Стены очищаются на высоте 1 м по мере передвижения машины поочередно правой и левой вертикальными щетками, а горизонтальная щетка при этом очищает пол и собирает остатки грузов к подгребному шнеку. Подгребной шнек подает груз через ковшовый элеватор в бункер машины. Наполненный бункер разгружается на продольный ленточный транспортер непосредственно или через направляющий бункер, соединенный с ленточным транспортером. Через систему транспортеров остатки груза передаются на транспортировочные средства и направляются на отведенные места.
|
|
Таблица 4.2 – Техническая характеристика уборочной машины
Наименование | Параметры |
Производительность, м3/ч | |
Вместимость бункера, м3 | 0,34 |
Ширина захвата за один проход, мм | |
Частота вращения ковшей элеватора, об/с | 0,5 |
Мощность электродвигателя привода щеток, кВт | 7,5 |
Скорость перемещения машины, м/мин | 3,8 |
Мощность двигателя электропривода перемещения машины, кВт | 1,1 |
Высота подъема заборного устройства, мм | |
Мощность двигателя гидропривода, кВт | 0,6 |
Род потребляемого тока | трехфазный переменный |
Напряжение, В — в цепи управления | |
Габаритные размеры, мм: (Д´Ш´В) | 2300´1800´1800 |
К сухой очистке можно отнести продувку сжатым воздухом вентиляционных каналов (воздуховодов) пассажирских вагонов для очистки их от пыли, которая скапливается на их внутренней поверхности при работе принудительной вентиляции. Для этого поочередно снимают вентиляционные решетки в служебном отделении и пассажирских помещениях (купе) и через отверстия в потолке с помощью шланга пылесоса или от воздушной сети вводят струю сжатого воздуха в канал при включенном вентиляторе.
Для удаления пыли из вагона при продувке вентиляционного канала используют передвижные пылеотсасывающие установки (рисунок 2).
На тележке 1 смонтирована камера 2. Тележка оборудована электроприводом 13 для передвижения по рельсам вдоль вагона. На камере установлен вентилятор 6, а внутри камеры расположены два воздушных канала 3, соединенных раструбом 8 с выхлопным отверстием вентилятора. Нижние части 9каналов, обрамленные криволинейными направляющими 10, опущены в воду, которая налита в нижнюю часть камеры. Всасывающее отверстие вентилятора присоединено к воздухоприемнику 5. Внизу камеры имеются два бункера 11 с трубами 12 для удаления шлама. Вверху смонтированы лабиринтные каплеуловители (жалюзи) 7.
|
|
Установка подается к дверному проему очищаемого вагона. Воздухоприемник с помощью цепного механизма 5 плотно прижимается к дверному контуру. После включения вентилятора пыль отсасывается из вагона через воздухоприемник в раструб. Насыщенный пылью воздушный поток проходит через щель между криволинейными направляющими каналов и увлекает за собой воду, которая в виде завесы падает в зону очищенного воздуха, унося смоченную пыль.
1 – тележка, 2 – камера, 3 – два воздушных канала, 4 – крышка, 5 – цепной механизм,6 – вентилятор, 7 – лабиринтные каплеуловители (жалюзи), 8 –раструб, 9 – ижние частиканалов, 10 – криволинейные направляющие, 11 – два бункера,12 – трубыдля удаления шлама, 13 – электропривод
Рисунок 4.3 – Пылеотсасываюшая передвижная установка
Воздушный поток, очистившийся в водной среде от пыли, устремляется вверх и, пройдя через каплеуловители, выбрасывается в помещение производственного участка. Задержанная пыль оседает в виде илистой массы на дно бункера. Производительность установки 20000 м3/ч, габаритные размеры 3,0´1,7´3,5 м.
После продувки вагона внутреннее оборудование и мебель протирают влажной ветошью. Для очистки диванов и спинок мягких вагонов используют пылесосы.
В вагоноремонтном депо Гороблагодатская Свердловской железной дороги применяется сухой метод очистки осей колесной пары (рисунок 3).
Рисунок 4.4 – Установка для сухой очистки осей колесной пары в вагоноремонтном депо Гораблагодатская Свердловской железной дороги
Рисунок 4.5 – Установка сухой очистки колёсных пар «ОР-12590-НПП»
Таблица 4.3 – Технические характеристики ОР-12590-НПП
Наименование | Параметры |
Тип установки | Стационарный |
Цикл | Полуавтоматический |
Время очистки колесной пары, мин | 3 – 5 |
Рабочее давление в гидросистеме, мах МПа (кг/см2) | 8 (80) |
Суммарная мощность электродвигателей, КВт не более | |
Количество обслуживающего персонала, чел | |
Габаритные размеры установки (Д´Ш´В) | 3000´1700´2580 |
Масса, кг |
Установка для сухой зачистки оси колесной пары и центров 21ДК. 443141.005
Установка предназначена для сухой зачистки средней части оси колёсной пары и колесных центров, при ремонте в условиях депо. Основные технические характеристики приведены в таблице 1.
Таблица 4.4 – Технические характеристики
Наименование | Параметры |
Установленная мощность, кВт, не более. | |
Напряжение питающей сети, В. | |
Частота питающей сети, Гц. | |
Время одного цикла зачистки колесной пары, мин. | |
Тип привода щеток зачистки средней части оси | электромеханический |
Тип привода щеток зачистки колесных центров | пневматический |
Габаритные размеры, мм, не более: (Д´Ш´В) | 3360´2338´1953 |
Масса, кг, не более |
Установка представляет собой сборно-сварную металлоконструкцию, в состав которой входят: основание с рельсами, механизмы установки и снятия колесной пары, механизм вращения колесной пары, механизм зачистки оси и механизм зачистки колесных центров.
На основании изделия жестко закреплены два механизма установки и снятия колесной пары. Механизмы состоят из кронштейнов с ложементами для захвата колесной пары за ось, кронштейны перемещаются за счет системы зубчатых передач от электромеханического привода.
Механизм вращения колесной пары состоит из обрезиненных роликов на кронштейнах, шарнирно закрепленных на П-образной раме. Подвод механизма вращения осуществляется пневматическим цилиндром, один из двух роликов является приводным. Вращение приводного ролика осуществляет электродвигатель через клиноременную передачу.
Перемещение механизма вдоль оси, и вращение щеток осуществляется электромеханическим приводом через цепную передачу.
Механизм зачистки колесных центров состоит из системы рычагов закрепленных на основании установки. Перемещение рычагов и подвод щеток к поверхности колесного центра осуществляется пневматическими цилиндрами. Вращение щеток происходит за счет радиальных сил трения возникающих в момент касания щетки с колесным центром.
Установка для сухой зачистки средней части оси колесной пары и колесных центров работает в автоматическом и ручном режиме.
Порядок операций устанавливается программой заложенной в контроллер, который установлен в пульте управления изделия.
Алгоритм работы установки следующий:
При подаче электропитания на панели пульта управления загорается лампочка «СЕТЬ».
Нажатием кнопки «ПУСК» запускается автоматический процесс зачистки колесной пары, при этом загорается лампочка «РАБОТА/ПАУЗА»
Программа включает привод отвода приводных роликов в исходное положение.
Механизм установки устанавливает колесную пару буксовыми узлами в ложементы. Затем подводится механизм вращения и механизм зачистки к колесной паре. Программа включает плавный разгон вращения колесной пары, и механизм зачистки центральной части оси.
Далее включается механизм зачистки колесных центров. Пневматическими цилиндрами щетки поджимаются к колесным центрам и осуществляется перемещение щеток по поверхности колесного цента с внутренней и наружной стороны.
Все операции и конечные положения рабочих органов отслеживает система концевых выключателей и датчиков положения.
По истечению времени зачистки, которое можно изменить, механизм зачистки колесных центров устанавливается в исходное положение. Механизм вращение переключается в режим торможения.
После полной остановки колесной пары механизм зачистки оси и механизм вращения поднимается в исходное положение.
Механизм снятия колесной пары снимает колесную пару с ложементов и по наклонным плоскостям колёсная пара скатывается со стенда. Программа завершает работу, технологический цикл зачистки колесной пары закончен.
Автоматическая система управления предусматривает режим «Пауза», необходимый для осмотра установки, устранения мелких замечаний в процессе работы.
При появлении неисправности, в любой момент времени, автоматический режим переходит в положение «Стоп», при этом загорается лампочка «Неисправность».
Преимущества:
– Использование износостойких чистящих элементов
– Время очистки колёсной пары – 6 мин.
– Возможность использования установки в составе поточной линии
Рисунок 4.6 – Установка для сухой зачистки средней части оси колесной пары и колесных центров
К способу сухой очистки можно отнести пескоструйную или дробеструйную очистку металлоконструкций для нанесения антикоррозионных лакокрасочных покрытий.
Для примера рассмотрим работу мобильного производственного участка дробеструйной обработки кузовов вагонов (рисунок 4.7).
Участок организован в составе поточной линии, которая смонтирована в сервисном центре антикоррозионной защиты металлоконструкций и подвижного состава ООО «ВЫСО» (далее — Центр АКЗ). Центр АКЗ размещен в локомотивном депо Каменск-Уральский Свердловской железной дороги. Аналогичные участки несложно организовать в крупных вагонных депо по ремонту пассажирских и грузовых вагонов.
На участке применяется современное оборудование германской фирмы «Кiess», которая является одной из ведущих в мире фирм по производству оборудования для дробеструйных работ.
Дробеструйная камера (с решетчатым полом, отверстиями для подачи свежего воздуха, резиновой защитой, вибротранспортером), компрессор, охладитель – осушитель воздуха, ресивер воздуха, абразивно-струйный котел, фильтровальная установка, вертикальный элеватор, очиститель абразива, система освещения, щиты управления и электропитания.
Рисунок 4.7 – Участок дробеструйной обработки кузовов вагонов ООО «ВЫСО»
Металлическая поверхность, подлежащая антикоррозийной защите, очищается от ржавчины, старого разрушившегося лакокрасочного покрытия, наплывов, потеков, утолщений дробеметным и дробеструйным способом.
Участок имеет длину 39 м и состоит из двух рабочих зон – дробеметного портала (на рисунке 4. не показан) и камеры дробеструйной обработки.
Размеры зоны дробеметного портала, мм (Д´Ш´В) – 6000×6000×6000.
Размеры дробеструйной камеры, мм (Д´Ш´В) – 33000×6000×6000.
Вагон или тележка с металлоконструкциями, например с элементами резервуаров, продвигается на входе через дробеметный портал, где очищается вчерне.
Окончательная очистка производится в дробеструйной камере 4 дробеструйщиками.
Каркас дробеструйной камеры выполнен из стальных конструкций. Обшивка стенок и потолка выполнена пористой резиной толщиной 100 мм, предохраняющей конструкции камеры от абразивного износа и выполняющей роль дополнительной шумоизоляции. В торцах стен камеры смонтированы ворота, открывающиеся вверх. В боковых стенах предусмотрены двери для обслуживания.
Камера снабжена:
– вибротранспортерной системой сбора абразива .
– вентиляционной системой .
– системой освещения .
– щитами управления и электропитания .
В Омском государственном университете путей сообщения разработана технология обработки поверхностей деталей подвижного состава гранулами двуокиси углерода, которая в кристаллическом состоянии представляет собой «сухой лёд». Если эти гранулы направить струёй на загрязнённую поверхность, то они под воздействием кинетических ударов получают дополнительную энергию, позволяющую им переходить в газообразное состояние.
Рисунок 4.8 – «Сухой лёд» удаляет ржавчину и остатки смазки с деталей и
механизмов без всякой пыли
Поскольку объём образующегося газа в 800 раз превосходит гранулированную форму, то на обрабатываемой детали происходит серия микровзрывов. Температура плавления сухого льда минус 78 градусов, поэтому загрязнённая поверхность испытывает при его воздействии сильный «термический шок». В результате микровзрывов и «шоковой терапии» все прилипшие частицы, остатки смазки, а также ржавчина и окалина легко удаляются с поверхности деталей и механизмов. Низкая температура «сухого льда» гарантирует его полный распад во время очистки.
Получившийся в результате углекислый газ удаляется вентиляцией, не оставляя в отличие от пескоструйных установок никакой пыли. «Сухой лёд» нетоксичен, доступен по цене и в сжиженном состоянии может храниться длительное время. В процессе очистки этот материал не повреждает обрабатываемые детали, поскольку он относительно мягок и мгновенно испаряется. В НТЦ «Транспорт» ОмГУПСа уже создано оборудование для очистки машин и механизмов гранулами двуокиси углерода как в ручном, так и в автоматическом режиме. После его испытания в условиях реальной эксплуатации учёные планируют внедрить новую технологию на ремонтных предприятиях отрасли.
Машины для водоструйной очистки вагонов и их узлов
Для очистки вагонов, их сборочных единиц и отдельных деталей применяют специализированные моечные машины струйного типа.
Существуют разнообразные конструкции специализированных струйных машин и комплексов для мойки пассажирских и грузовых вагонов, вагонных тележек, колесных пар, корпусов букс, роликовых буксовых подшипников, аккумуляторных батарей, холодильных агрегатов и т. п.
Устройство и принцип действия машин для водоструйной очистки вагонов и их деталей, идентичны для всех машин, несмотря на их большое разнообразие по конструкции, моделям, изготовителям и назначению.
Эти машины оснащены системой гидрантов (рамп), оборудованных струйными насадками (соплами).
Основным базовым элементом этих машин является гидромонитор (водомет) – насосный агрегат для создания гидравлических струй и управления ими с помощью ствола со специальными насадками (соплами), создающими плоскую веерную или другой формы струю.
Машины, как правило, включают:
— камеру мойки .
— устройства подачи вагонов или их узлов (на входе и выходе камеры) .
— систему подготовки и подачи моющего раствора (гидросистемы высокого и низкого давления) .
— систему регенерации (очистки) моющего раствора .
— систему автоматического управления
Струйные моечные машины бывают тупиковыми и проходными, одно-и многокамерными, одно- и двухзонными, с сушильными отсеками и без них, универсальными и специализированными.
Специализированные моечные машины для водоструйной очистки
грузовых вагонов.
Для водоструйной очистки грузовых вагонов применяются различные специализированные вагономоечные установки струйного типа, которые размещаются в ангарах или специальных зданиях.
В установках использован общий принцип работы, при котором поверхность вагона обмывается струей воды под давлением, остатки груза и мусор стекают в отстойники, откуда удаляются по мере накопления.
В зависимости от климатических условий установки монтируются в отапливаемых ангарах или на открытом воздухе.
Температуру моющих жидкостей в вагономоечных установках и машинах поддерживают в пределах 70 – 90°С. Давление струй моющего раствора 0,5 – 1,6 МПа, ополаскивающей воды 0,3 – 0,5 МПа.
При мойке чистой водой давление значительно повышается и доходит до 4 МПа.
Крытые грузовые вагоны, полувагоны и платформы очищают в специализированных моечных установках с многократным использованием моющих жидкостей.
На рисунке 5 представлен общий вид агрегата для обмывки грузовых вагонов различных типов. На тяговый конвейер установки подается одновременно сцеп из нескольких вагонов, и процесс обмывки происходит непрерывно.
На фундаменте 18, вдоль которого уложен рельсовый путь 17, установлен моющий агрегат.
1 – натяжной блок . 2 – два толкателя . 3 – направляющие . 4 – приводная станция . 5 – резервуары . 6 – камнеловушка .7 – транспортер . 8 – ящик . 9 – сточные канавы . 10 – два гидранта . 11 – утепленный ангар . 12 – портал . 13 – насосная станция (в насосной станции установлены баки для осветленного моющего раствора и очищенной воды, водоподогреватели, гидроциклоны, флотатор и насосы) . 4 – тельфер . 15 – бункеры . 16 – узкоколейный путь . 17 – рельсовый путь . 18 – фундамент
Рисунок 4.9 – Общий вид агрегата для обмывки грузовых вагонов различных типов
Гидрант для внутренней обмывки открытого подвижного состава и крыш вагонов оборудован качающимися струйными насадками и смонтирован на подъемной раме в портале 12 перед утепленным ангаром 11. Внутри ангара размещены два гидранта также с качающимися насадками для обмывки ходовых частей, рам и кузовов, а на выходе из ангара установлены два гидранта 10 с неподвижными насадками для ополаскивания чистой водой.
По сточным канавам 9 загрязненный моющий раствор и вода стекают в соответствующие резервуары 5. Куски твердых включений сбрасываются в камнеловушку 6, откуда транспортером 7 подаются в ящик 8. В насосной станции 13 установлены баки для осветленных жидкостей (моющего раствора и воды), водоподогреватели, гидроциклоны, флотатор и насосы. Грязь из-под циклонов собирается в бункеры 15, которые перемещаются по узкоколейному пути 16 за пределы здания и с помощью тельфера 14 разгружаются в автосамосвалы.
Конвейер для подачи вагонов состоит из приводной станции 4, направляющих 3, натяжного блока 1, двух толкателей 2.
При подходе полувагона в зону действия гидранта последний опускается к полу, и по мере продвижения полувагона происходит мойка его внутренних поверхностей. По окончании мойки гидрант возвращается в исходное верхнее положение. Если обрабатываются крытые вагоны, то гидрант остается наверху и моет крыши. Затем вагоны попадают в ангар, в зоны действия обмывочных и ополаскивающих гидрантов. Общая продолжительность обработки одного вагона составляет 12 – 15 мин.
1,3 – электроприводы дл перемещения тележки и поворота консолей . 2 – шланги . 4 – трубы . 5 — моющие приборы . 6 — поворотные консольные трубопроводы . 7 – стойки . 8 – тележка
Рисунок 4.10 – Машина моечная с поворотными консольными трубопроводами для внутренней промывки грузовых вагонов
Для внутренней промывки крытых грузовых вагонов применяют моечные машины, оборудованные поворотными консольными трубопроводами 6 (рисунок 4.10) с моющими приборами 5 на концах.
Трубопроводы смонтированы на стойках 7, которые установлены на тележке 8. Перемещение тележки и поворот консолей осуществляются с помощью электроприводов 3 и 1. Вода в консоли подается по трубам 4 с шлангами 2. Машину устанавливают вблизи от насосной станции и источника горячей воды вдоль пути промывки вагонов. Вагон подают к машине, но при необходимости ее можно передвинуть на некоторое расстояние относительно оси дверного проема. Затем консольные трубопроводы вводят внутрь кузова так, чтобы моющие приборы располагались на середине каждой его половины. После промывки вагона консоли выводят наружу, промытый вагон убирают и на его место подают следующий.
Таблица 4.5 – Техническая характеристика моечной машины
Наименование | Параметры |
Время ввода (вывода) моющих приборов, с | |
Давление промывочной воды, МПа | 1,5 – 2 |
Температура воды, °С | до 80 |
Время промывки одного вагона, мин | 2 – 3 |
Расход воды на один вагон, м3 | 2,5 – 3 |
Габаритные размеры, м | 6,0´2,5´2,0 |
Для очистки полувагонов используются моющая установка, конструкция которой разработана ПКБ ЦВ МПС и показана на рисунке 4.11.
1 – толкатели транспортного конвейера челночного типа, 2 – рампа наружной очистки, 3 – рампа внутренней обмывки, 4 – приводы и насосы душевых установок, 5 – ангар, 6 – скребковый транспортер, 7 – путь и направляющие тягового конвейера, 8 – рампа смыва остатков груза и мусора
Рисунок 4.11 – Установка для обмывки полувагонов
Установка состоит из рампы внутренней обмывки 3, рампы наружной очистки 2, рампы смыва 8 остатков груза и мусора, гидравлической системы, очистных устройств, ангара.
Таблица 4.6 – Техническая характеристика установки для обмывки полувагонов
Наименование | Параметры |
Время полной обмывки, мин | |
Скорость перемещения полувагона, м/мин | 1,2 |
Рабочий объем бака для воды, л | |
Расход воды на полувагон, л | |
Расход пара при давлении 0,3 МПа (3 кгс/см2), т/ч | |
Тип насоса для перекачки загрязненной (отработанной) воды | 4 НФ |
Тип насоса для подачи очищенной воды | 4Кб |
Общая мощность электродвигателей на установке, кВт | |
Потребная мощность при внутренней обмывке кузова, кВт | |
При наружной обмывке полувагона, кВт | |
Расход электроэнергии на обмывку одного полувагона, кВт-ч | |
Угол поворота направляющих качающихся сопел | 90° |
Объем бункера тележки для грязи, м3 | 1,4 |
Скорость перемещения скребков транспортера (для грязи), м/с | 0,1 |
Тяговое усилие на цепи транспортера для перемещения вагона, кН (тс) | 12 (1,2) |
Габарит прохода через устройство при открытых люках | 1-Т |
С помощью таких установок можно добиваться высокого качества очистки полувагонов при сравнительно незначительных затратах.
В зависимости от степени загрязнения обмывка полувагонов производится со всеми или с четырьмя – шестью открытыми люками. Открытие люков осуществляется при прохождении полувагона через специальное устройство. Полувагон захватывается толкателями 1 транспортного конвейера челночного типа и с установленной скоростью продвигается через установку. Одновременно с конвейером включаются приводы и насосы душевых установок 4. Вся площадь внутренней и наружной поверхности полувагона подвергается обмывке по мере прохождения через установку. Процесс обмывки сильно загрязненных вагонов может быть повторен.
Обслуживание устройства осуществляется двумя операторами. В обязанности операторов входит включение и выключение основных и вспомогательных механизмов, контроль за качеством обмывки, уход и наблюдение за работой насосов, гидроциклонов и скребкового транспортера, регулирование температуры воды в баках. Управление установкой осуществляется из кабины, обеспечивающей визуальное наблюдение при внутренней и наружной обмывке и наблюдение за работой агрегатов машинного отделения.
Ангар устройства 5 предназначается для сбора воды после обмывки, создания необходимого температурного режима в рабочей зоне установки. Металлический ангар устанавливается на бетонном основании-котловане, через который проложены путь и направляющие тягового конвейера 7. В нижней части котлована установлен скребковый транспортер 6 для сбора в бункер остатков груза и грязи. Устройство обеспечивает очистку от остатков грузов, внутреннюю и наружную обмывку 40 полувагонов в сутки.
Закрытие крышек люков полувагонов после прохождения обмывки является наиболее трудоемкой технологической операцией.
Для закрытия крышек люков используют специальные приспособления (рисунок 4.12), представляющие собой пневматические цилиндры 5, к поршням которых присоединены специальные захваты 7. Эти приспособления устанавливаются по обе стороны полувагона 1. В верхней части пневматические цилиндры присоединены к подвескам 3, которые могут перемещаться вдоль вагона по направляющим и опорным балкам 2. Опорные балки 2 подвешены к стойкам 4.
Пневматические цилиндры перемещают вдоль вагона и устанавливают их, совмещая поперечные оси цилиндров с захватом открытых крышек люков 6. После открытия рабочего крана сжатый воздух поступает в цилиндр и, перемещая поршень цилиндра, поднимает захват с крышкой люка до соприкосновения последнего с рамой полувагона. Крышка люка закрывается откидными запорами, после чего сжатый воздух из пневмоцилиндра выпускается в атмосферу, освобождая захват от крышки люка. Захват с пневматическим цилиндром перемещается к следующей открытой крышке люка и закрывает ее в аналогичной последовательности.
1 – полувагон, 2 – шланги, 3 – шток поршня пневматического цилиндра, 4 – стойка, 5 – рычаги-захваты, 6 – толкатель
Рисунок 4.12 – Комплект приспособлений для закрытия крышек люков
полувагонов
На рисунке 8 показана позиция для закрытия крышек люков после очистки полувагонов, подаваемых из моечной установки 1 толкателем 6. На позиции установлено четырнадцать стоек 4, внутри которых перемещаются рычаги-захваты 5. В верхней части рычаги-захваты соединены со штоками поршней пневматических цилиндров 3, закрепленных на стойках 4. Поршни цилиндров двустороннего действия. Сжатый воздух поступает по шлангам 2. Вагон с открытыми крышками люков устанавливается таким образом, чтобы рычаги-захваты находились по оси крышек люков. После этого в цилиндры 3 подается сжатый воздух. Рычаги вместе с поршнями цилиндров поднимаются, захватывают крышки люков и поднимают их до соприкосновения с плоскостью прилегания. Одновременно закидки запоров входят в зацепление с запорными угольниками крышек люков.
Сжатый воздух подается в цилиндр с обратной стороны поршня, одновременно сообщая ранее заполненную полость цилиндра с атмосферой.
Рычаги-захваты возвращаются в исходное положение. После этого проверяется правильность закрытия крышек люков, и вагоны поступают на вагоносборочный участок.
При деповском ремонте вагоны подвергаются наружной обмывке. Для этого применяются специальные моечные установки рамочного типа (рисунок 4.13). В таких установках в качестве моющего средства используют 3 % раствор каустической соды.
1 – емкость с моющим раствором . 2 – насос для подачи раствора . 3 – подающий трубопровод . 4 – нагнетательный коллектор . 5 – обмывочная рамка с соплами . 6 – вагон . 7 – желоб для сбора загрязненного моющего раствора . 8 – сливная воронка . 9 – сборник загрязненного моющего раствора . 10 – ограждение ангарного типа
Рисунок 4.13 – Схема моечной установки для наружной обмывки вагонов
При подготовке крытых цельнометаллических вагонов, крытых хопперов используется специализированная поточная линия, на первой позиции которой производят проверку водонепроницаемости кузова, протягивая вагон через обмывочную рампу со скоростью 1,2 м/с. Вода подается холодная под давлением до 0,1 МПа. При необходимости наружной обмывки подают горячую воду (60 – 80°С) под более высоким давлением – 0,4 – 0,6 МПа.
Специализированные машины для наружной обмывки пассажирских вагонов
Наружная обмывка пассажирских вагонов производится в специализированных вагономоечных установках с вращающимися щетками (рисунок 10).
В первой рабочей зоне установки осуществляются три моечные операции, во второй зоне – операция ополаскивания.
Гидрант 1 с качающимися насадками, расположенный в начале ангара, моет нижнюю часть вагона. Через неподвижные насадки гидранта 3 моющий раствор подается к капроновым щеткам 16, протирающим продольные стены вагона. Гидрант 4 двумя качающимися насадками моет крышу вагона.
1, 4 – гидранты с качающимися насадками, 2 – лотки фундамента, 3 – неподвижные насадки гидранта, 5 – подогреватель, 6, 7, 8 – насосы, 9 и 13 – отстойные резервуары, 10 – бак, 11 – трубопроводы для стока воды, 12 – фильтр, 14 и 16 – щетки с механизмами для вращения и прижатия их к поверхностям кузова, 15 – гидрант с неподвижными насадками
Рисунок 4.14 – Расположение оборудования установки для наружной обмывки
пассажирских вагонов
Гидрант 15 предназначен для ополаскивания крыши и кузова вагона чистой водой смонтирован в конце установки. Состоит из верхней горизонтальной и двух вертикальных труб с неподвижными насадками. Через вертикальные трубы подается вода к щеткам 14. Все щетки оборудованы механизмами для вращения и прижатия их к стенам кузова.
В процессе мойки и ополаскивания загрязненные моющий раствор и вода стекают по лоткам фундамента и трубопроводам 2 и 11 в отстойные резервуары 13 и 9. Из отстойного резервуара 13 через фильтр 12 осветленный отстаиванием раствор подается насосом 6 в моечные гидранты для повторного использования, проходя через подогреватель 5. Из резервуара 9 ополаскивающая вода перекачивается насосом 7 в бак 10, где подогревается с добавлением воды из водопровода. Затем насосом 8 снова подается в ополаскивающий гидрант. Торцовые стены моются из брандспойта, непосредственно подключаемого к трубопроводам подачи моющих жидкостей.
В процессе обмывки вагон непрерывно перемещается с помощью толкателя со скоростью 0,1 м/с. Расчетная производительность установки составляет 8 – 9 вагонов в смену. На обработку одного вагона предусматривается моющего раствора 0,5 м3, чистой воды – 2 м3. Габаритные размеры установки 20,0´5,2´6,3 м.
В настоящее время внедряются современные вагономоечные комплексы.
К примеру, в 2007 году введен в действие новый вагономоечный комплекс в вагонном депо на станции Екатеринбург-Пассажирский Свердловской железной дороги. На его создание ОАО «РЖД» направило порядка 100 млн.рублей. Пока комплекс рассчитан на обработку только пассажирских вагонов. Но при доукомплектовании комплекса дополнительным оборудованием можно будет очищать и электропоезда. Предусмотрено, что моющие щетки могут автоматически приспосабливаться к габаритным размерам корпусов пассажирских вагонов и электропоездов. В отличие от всех существующих, эти комплексы рассчитаны на обмывку не только боковых стен кузова, но и крыши, подвагонных тележек и оконных стекол.
Рисунок 4.15 – Общий вид вагономоечного комплекса на станции Екатеринбург-Пассажирский Свердловской железной дороги и комнаты операторов
Новый вагономоечный комплекс (рисунок 4.15) сооружен по проекту группы компаний «Чистые технологии» (Санкт-Петербург) и запущен в работу первым на сети дорог. В комплексе установлены современные датчики и другая микропроцессорная техника, позволяющая автоматизировать комплексную очистку кузовов пассажирских вагонов. Предусмотрен замкнутый водооборотный цикл очистки раствора, соблюдены все требования экологической безопасности. Применяемые современные моющие средства позволяют избавиться от значительных наслоений грязи, не нарушая лакокрасочного покрытия.
Проектная мощность вагономоечного комплекса предусматривает помывку 24 составов в сутки. Для сравнения – за сутки на станции Екатеринбург-Пассажирский формируется от 13 до 15 составов.
Технологический процесс предусматривает четыре этапа: смачивание поверхностей моющим раствором, мойка щеточными механизмами, ополаскивание и сушка. Поезд на скорости 1,5 километра в час заходит в крытое помещение комплекса и движется сквозь строй щеток. На обработку одного состава отводится 20 минут. С учетом времени подачи состава из парка и его уборки после мытья общее время – примерно 40 минут.
Оборудование для промывки котлов цистерн
Требования, предъявляемые при подготовке цистерн под налив, зависят от продукта, который был слит из цистерны, и наименования продукта, подлежащего наливу. Для возможных комбинаций слитого и наливаемого продукта необходимо выполнять следующие технологические операции по очистке котлов.
1. Зачистка – удаление остатков слитого продукта. Для цистерн с нижним сливом – слив, для цистерн без нижнего слива – отсос с помощью вакуум-насосов или пароэжекторных установок. При удалении из котлов остатков продуктов с высокой вязкостью (гудрон, полугудрон, битумы жидкие) для придания им большей текучести производят предварительно пропарку котлов (подогрев паром).
2. Пропарка – обработка котла внутри паром под давлением 0,08 – 0,1 МПа для очистки внутренней поверхности от остатков слитого продукта, с периодическим удалением конденсата и остатков груза.
3. Промывка – обработка внутренней поверхности котла водой температурой 80 – 90 °С под давлением до 2 МПа для очистки от остатков слитого продукта. Добавляют растворители: керосин, бензин и поверхностно-активные вещества, например МЛ-2 (0,3 – 0,5 %).
4. Дегазация и сушка котлов – удаление из котла паров перевозимого продукта и остатков воды после промывки.
5. Протирка безворсовым материалом (хлопчатобумажная ткань), удаление с внутренней поверхности котла остатков груза и воды.
6. Проверка на взрывобезопасность (анализ проб воздуха из котла на содержание паров, образующих взрывчатые смеси).
7. Заправка клапанов сливных приборов – проверка исправности и плотности прилегания клапанов.
8. Наружная очистка котлов перед плановым ремонтом, в процессе которой выполняют следующие операции:
— предварительная обмывка водой температурой 60 – 70 °С, давлением 0,3 – 0,4 МПа в течение 1 – 2 мин .
— обмывка 6 – 8 %-ным раствором каустической соды (температура 60 – 70°С, давление 0,4 МПа) .
— обмывка 1 – 2 %-ным раствором ортофосфорной кислоты при температуре 30 – 40 °С с целью нейтрализации раствора каустической соды.
В соответствии с ГОСТ 1510–76 «Нефть и нефтепродукты» в зависимости от наименования слитого продукта и наименования продукта, который будут наливать, установлено семь видов (групп) подготовки, обозначаемых цифрами:
0 – налив запрещен, например, из-под гудрона под бензин .
1 – удалить остаток, промыть или пропарить и просушить, например, из-под дизельного топлива под бензин .
2 – удалить остаток и просушить или протереть, например, из-под дизельного топлива под автомобильный бензин .
3 – удалить остаток, например, из-под бензина авиационного этилированного под такой же бензин .
4 и 5 – зачистка не требуется, например, из-под гудрона под мазут или нефть .
6 – удалить остаток, промыть или пропарить и протереть, например, из-под нафтила под керосин.
Для подготовки цистерн из-под этилированного бензина выделяются отдельные пути, ввиду того, что продукт ядовит.
На промывочных эстакадах установлены монорельсы с электроталями для подъема и опускания в котел механизированного промывочного прибора. К промывочному прибору с помощью шлангов подведены пар, горячая вода и сжатый воздух.
Имеются автоматизированные системы промывки, работающие по трем вариантам:
– пропарка – промывка – дегазация .
– пропарка – дегазация .
– промывка – дегазация.
Установку режима производят на пульте управления.
Для выполнения экологических требований на ППС должны быть мощные очистные сооружения для сбора остатков нефтепродуктов из промывочной воды.
На рисунке 4.16 приведена схема вакуумной установки для удаления из цистерн остатков груза и конденсата. В цистерны с верхним сливом для удаления остатка груза и конденсата опускают вакуумные рукава.
Вакуумная установка состоит из вакуум-насоса 1, трубопроводов 2 и 3 и вакуум-сборника 4. Перед пуском насоса вентиль А закрывается и открывается вентиль Б. При достижении разрежения воздуха до 0,06 – 0,07 МПа, не прекращая работы установки, открывают вентиль А и остатки неслитого нефтепродукта засасываются концом шланга в вакуум-сборник. После заполнения вакуум-сборника на 75 % нефтепродукты сливают через вентиль В в лоток 5.
На ППС предъявляются повышенные требования к пожаробезопасности.
1 – вакуум-насос, 2 и 3 – трубопроводы, 4 – вакуум-сборник, 5 – лоток,
А и Б – вентили
Рисунок 4.16 – Схема вакуумной установки для удаления из цистерн остатков
нефтепродуктов
После пропарки и промывки горячей водой котел цистерны должен быть охлажден и дегазирован с открытой крышкой люка.
Камера для наружной очистки длиной 39 м имеет три-четыре зоны, в каждой из которых установлена П-образная рампа из трубы с насадками для подачи раствора на цистерну по описанной выше технологии. Время на очистку 30 – 50 мин в зависимости от загрязнения, расход воды около 60 м3 и пара около 1500 кг на одну цистерну.
Наиболее производительными и современными промывочными станциями для отмывки, зачистки, обезжиривания механизмов, деталей, узлов, поверхностей от нефтепродуктов, жиров, масел и смазок, с использованием технологии замкнутого цикла отмыва, являются универсальные мобильные станции серии СПУМ, автоматизированные промывочные машины серии МАП, с применением локальных очистных устройств и комплексов оборудования для обезвреживания и утилизации нефтеотходов и шламов.
Данное оборудование поставляется Санкт-Петербургской холдинговой компанией «Чистые технологии», которая работает с 1999 года в сфере производства и реализации средств моющих технических порошкообразных средств (СМТП) нового поколения серии «О-БИС». На сети российских железных дорог действует более 30 универсальных промывочных станций нового типа различных версий и производительности для цистерн.
Наиболее полно проработаны ресурсосберегающие бессточные рециркуляционные технологии отмывки железнодорожных цистерн.
Технологический процесс отмывки железнодорожных цистерн при незначительных затратах энергоресурсов позволяет в сжатые сроки (до 20 минут на цистерну) экономично и качественно (с оформлением акта ВУ-19) выполнять операцию отмыва, максимально соблюдая при этом требования экологической чистоты и охраны труда. Применяются универсальные мобильные промывочные станции УМПС-02, с использованием моющих средств нового поколения О-БИС, О-БИСМ
1 – цистерна . 2 – моечная машинка . 3 – универсальная мобильная промывочная станция (УМПС) в составе: 31 – мембранный откачивающий насос . 32 – сепаратор — сборник моющего раствора . 33 – напорный насос . 34 – многозаходный паровой теплообменник . 4 – сборник отсепарированных нефтепродуктов
Рисунок 4.17 – Принципиальная схема отмывки железнодорожных цистерн
посредством УМПС и «О-БИС»
В сравнении с традиционной ППС данная технология требует:
– потребления воды в 6 раз меньше,
– пара – в 2,7 раз меньше.
– общая себестоимость промывки снижена в 2,2 раза .
– время промывки уменьшено в 2 раза .
– содержание воды в отмытом из цистерн нефтепродукте снижается в 5,3 раза (с 8 до 1,5%) и он может быть возвращен по назначению,
– на поверхности железнодорожных цистерн остается антикоррозионная «защитная пленка».
Рисунок 4.18 – Внешний вид УМПС, установленной в вагонном депо «Псков» Октябрьской железной дороги
В вагонных депо, специализирующихся на ремонте цистерн, организуется отделение ремонта сливных приборов и отделение ремонта предохранительно-впускных клапанов.
Здесь рекомендовано к применению следующее оборудование:
— Стенд для ремонта сливных приборов типа Т1300 ПКБ ЦВ .
— диагностическое и испытательное оборудование, в том числе .
— Стенд для испытания сливных приборов типа Т1262 ПКБ ЦВ .
— Оснастка для гидравлического испытания котла .
— Стенд для пневматического испытания котла .
— Стол для демонтажа и монтажа впускных клапанов типа Т1249.03М ПКБ ЦВ .
— Стол для регулировки и испытания клапанов типа Т1236 ПКБ ЦВ.
Устройства тепловой очистки бункерных вагонов
Для очистки бункерных битумных полувагонов выделяются отдельные пути, т.к. используется способ очистки, отличный от очистки цистерн.
Битумы различают по температуре размягчения на твердые (60 – 90оС), полутвердые (25 – 50оС) и жидкие.
При очистке бункерных вагонов для перевозки твердого битума впускают пар в паровую рубашку.
В случае повреждения внутренней обшивки бункера и заполнения паровой рубашки битумом разрешается вырезать отверстие для слива и приваривать штуцер для паропровода. В отдельных случаях, когда повреждена внутренняя обшивка бункера, применяется разогрев снятого бункера, с подачей его в специальную камеру тепловой обработки. В помещении, примыкающем к камере, смонтирована мазутная топка. Разогрев в камере производится горячими газами – продукт горения мазута. Съем бункера с вагона и установка его на тележку для подачи в камеру производится с помощью козлового крана.
Устройства для очистки воды и моющих растворов
Гидравлические системы вагономоечных установок и машин предусматривают очистные устройства, восстанавливающие моющие растворы.
Пассивная очистка моющих жидкостей происходит путем отстаивания их в специальных резервуарах-отстойниках.
Активная очистка моющих жидкостей производится с помощью комплексной гидросистемы, состоящей из гидроциклонов, флотаторов, различных фильтров и других устройств.
Гидроциклоны – это цилиндрические баки, оканчивающиеся внизу конусной частью.
При вводе в верхнюю часть гидроциклона струи загрязненной жидкости, которая направляется по касательной к образующей, грязевые частицы за счет центробежной силы устремляются к стенкам циклона и сползают вниз, откуда отбираются затем в грязеприемник.
Гидроциклоны обеспечивают осветление раствора на 70 – 80%. Они компактны, но нуждаются в уходе и регулировке.
Во флотаторных установках осуществляется тонкая фаза очистки. Принцип флотационной очистки (флотация – от французского «плавать по поверхности») заключается в насыщении загрязненной жидкости пузырьками воздуха, которые, поднимаясь на поверхность, увлекают с собой прилипающие к ним частицы грязи и масел, образуя на поверхности грязевую пену.
Рисунок 4.19 – Гидроциклон системы регенерации раствора
Качество и скорость очистки значительно повышаются при добавлении в загрязненную жидкость коагулянтов–химических соединений, которые, воздействуя на частицы веществ, находящихся в мелкодисперсном взвешенном состоянии (суспензии, эмульсии), укрупняют их и последние в виде хлопьев, плотность которых становится выше плотности моющего раствора, быстро опускаются на дно, образуя коагулят. Легкие хлопья с пузырьками воздуха поднимаются на поверхность.
В качестве коагулянтов употребляют сернокислый алюминий, сернокислое или хлористое железо, полиакриламид.
Иногда вводят деэмульгаторы (например, соли кальция и магния), разрушающие эмульсии. В этом случае эмульгированная нефть выходит из дисперсного состояния, превращается в капельки и, всплывая на поверхность, образует нефтяную пленку, которая затем легко удаляется.
Схема гидросистемы с многократным использованием моющего раствора показана на рисунке 4.20.
Эти установки работают в автоматическом цикле.
Обрабатываемый вагон помещают под гидрант 24, в который подается моющий раствор.
После мойки вагона загрязненный раствор через устройство грубой очистки 1 стекает в сточный резервуар 2, который оборудован гряземешалкой 3. Из этого резервуара насосом 4 раствор перекачивается по трубопроводу 6 в устройство тонкой очистки 7 – гидроциклон, затем, после отделения грязи по трубопроводу 8 поступает во флотационное устройство 9.
Из флотатора, где происходит очистка от нефтепродуктов и мелкодисперсных твердых частиц, раствор попадает в бак очищенного раствора 21, из которого насосом 22 через теплообменник 23 снова подается в обмывочный гидрант.
Осветленный раствор может перетекать из гидроциклона по трубопроводу 20 непосредственно в резервуар, минуя флотатор. Очистительные устройства снабжены баками 5 к 11 для грязи, а около флотатора дополнительно имеется сборник 12 для грязной пены.
1 – устройство грубой очистки, 2 – сточный резервуар, 3 – гряземешалка, 4 – насос, 5 – бак для грязи, 6 – трубопровод, 7 – устройство тонкой очистки — гидроциклон, 8 – трубопровод, 9 – флотационное устройство, в т.ч. флотатор (круглый бак с коническим бункерообразным днищем), 10 – сливная труба, 11 – бак для грязи, 12 – сборник для грязной пены 13 – воздухораспределительный трубопровод для барботажа раствора, 14 — цилиндрической обечайка, 15 – приемник, 16 – скребковое устройство с электроприводом, 17 и 18 – баки для растворов коагулянта и деэмульгатора, 19 — переливной желоб, 20 –трубопровод, 21 – бак очищенного раствора, 22 – насос, 23 — теплообменник, 24 – обмывочный гидрант, камнеловушка: 25 – транспортер, 26 – приемный лоток, 27 — лопасти колеса, 28 – шнековый барабан, 29 – уловитель, 30 – корпус, 31 – труба
Рисунок 4.20 – Схема гидросистемы моечной установки с многократным
использованием моющего раствора
В качестве устройства грубой очистки применяют сетчатый фильтр или камнеловушку. Камнеловушку используют при большом количестве твердых включений. Она представляет собой шнековый барабан 28 из листовой стали, расположенный в полуцилиндрическом днище корпуса 30.
Отработанный раствор попадает по трубе 31 в нижнюю часть ловушки. Куски твердых включений захватываются лопастями шнека, попадают на лопасти колеса 27 и поднимаются на приемный лоток 26, откуда сбрасываются на транспортер 25 и далее на площадку накопления.
Плавающие включения задерживаются уловителем 29 и выталкиваются наружу.
Очищенный раствор через горловину ловушки, закрытую сеткой, сливается в резервуар загрязненного раствора.
Флотаторсостоит из круглого бака с коническим бункерообразным днищем, внутрь бака вставлена цилиндрическая обечайка 14. Внизу обечайки находится воздухораспределительный трубопровод 13 для барботажа раствора. В верхней части смонтировано скребковое устройство 16 с электроприводом для сбрасывания пены в приемник 15 и далее в сборник 12. В верхней части бака по периметру расположен переливной желоб 19, из которого отбирается очищенный моющий раствор. Внизу бака предусмотрена сливная труба 10 для удаления осадка. Баки 17 и 18 служат для растворов коагулянта и деэмульгатора.
В некоторых депо эксплуатируются флотационные установки типа ЦНИИ-5.
Установка представляет собой комплект в составе гидроциклона и флотатора, но может работать без гидроциклона, если сточные воды имеют небольшое количество взмученных примесей.
Достаточно хорошая очистка растворов достигается в отстойниках, но для этого требуются значительные площади и много времени. Операции по очистке отстойников очень трудоемки, с применением тяжелого ручного труда.
Рассмотрим для примера оборудование для подготовки и очистки моющих растворов, производства ООО «ИРТРАНС»
Системы подготовки моющего раствора предназначены для комплектования машин для мойки агрегатов, узлов и деталей подвижного состава.
Разработаны и изготавливаются две группы таких систем:
— встроенные в соответствующие моечные машины .
— автономные – соединенные с моечными машинами системой трубопроводов.
Встроенные системы подготовки моющего раствора применяются, как правило, в машинах, используемых для мойки сравнительно небольших узлов и деталей подвижного состава (корпусов букс, подшипников, тормозного оборудования, деталей буксового узла и т.д.). Встроенные системы подробно были рассмотрены в предыдущей лекции. Они включают бак с обогревом (пар и электронагреватели) и электронасосом, подающим моющий раствор в режиме рециркуляции на промываемые узлы. Камера мойки располагается на крышке бака.
Автономные системы подготовки моющего раствора применяются для мойки крупногабаритных узлов (колесные пары, тележки, редукторы и т.д.). В этом случае требуются значительно большие энергозатраты на нагрев моющего раствора и баки необходимо оснащать дополнительными устройствами для очистки циркулирующего моющего раствора.
ООО «ИРТРАНС» изготавливает два типа автономных систем нагрева:
— тип 1 – для крупногабаритных узлов, при мойке которых в моющий раствор попадает большое количество твердых частиц грязи (тележки, колесные пары, которые очищаются в процессе мойки вращающимися щетками и т.д.) .
— тип 2 – для узлов, при мойке которых в моющий раствор попадает большое количество смазки (корпуса редукторов и т.д.).
1 – камера мойки, 2 – насос подпора, 3 – бак, 4 – гидроциклон, 5 – высоконапорный насосный агрегат, 6 – насос системы регенерации, 7 – пульт управления электронагревом
Рисунок 4.21 – Автономная система подготовки моющего раствора (тип 1)
1 – промежуточная емкость, 2 – гидрозатвор, 3 – насос перкачки, 4 – датчик реле уровня, 5 – вентиль для стравливания воздуха, 6 – заборная труба, 7 – труба, 8 – регулировочный кран, 9 – вентиль, 10 – сливной коллектор, 11 – нагнетательный трубопровод
Рисунок 4.22 – Система подачи моющего раствора из поддона камеры мойки в обогреваемый бак.
Моющий раствор из поддона камеры мойки, поступает в первую секцию трехсекционного бака. Внутри бака находятся перегородки, которые создают зигзагообразный поток моющего раствора и способствуют осаждению твердой фазы из моющего раствора в первой секции бака. Далее моющий раствор нагревается в баке до заданной температуры. Насос подпора забирает нагретый моющий раствор из третьей секции бака и подает его на вход высоконапорного насосного агрегата, обеспечивая необходимый подпор на входе в насос.
Рисунок 4.23 – Бак системы подготовки моющего раствора (вариант с паровым нагревом)
Высоконапорный насосный агрегат по трубопроводу подает моющий раствор в форсунки камеры мойки. Устанавливается на полу участка рядом с камерой мойки.
Система регенерации за счет использования гидроциклона очищает циркулирующий моющий раствор от механических взвесей, включает насос, гидроциклон, специальную тележку для сбора сгущенного осадка, имеет направляющие для выкатки тележки.Насос системы регенерации забирает грязную воду с взвесями из первой секции бака и подает ее в гидроциклон. Пройдя гидроциклон очищенная вода сливается в первую секцию бака, а сгущенный осадок из гидроциклона сливается в тележку, установленную под гидроциклоном. Поверхностный слой из тележки через перелив возвращается в первую секцию бака.
Система автоматического управления обеспечивает регулирование температуры моющего раствора, ее визуальный контроль, включение и отключение высоконапорного насосного агрегата, насоса подпора и насоса системы регенерации.
Таблица 4.7 – Техническая характеристика
Наименование | Параметры |
Емкость бака для моющего раствора, м³ | 5,5 |
Температура моющего раствора, °С | от 40 до 90 |
Высоконапорный электронасосный агрегат: | |
Вариант 1: | |
— тип | ЦНСгА38-176 |
— подача, м³/час | |
— напор, м. вод. ст. | |
— мощность электродвигателя, кВт | |
Вариант 2: | |
— тип | ЦНСгА 60-165 |
— подача, м³/час | |
— напор, МПа м. вод. ст. | |
— мощность электродвигателя, кВт | |
Насос подпора: | |
Вариант 1: | |
— подача, м³/час | |
— напор, м. вод. ст. | |
— мощность электродвигателя, кВт | 4,0 |
Вариант 2: | |
— подача, м³/час | |
— давление, МПа (кгс/см²) | 0,18 (1,8) |
— мощность электродвигателя, кВт | 11,0 |
Насос системы регенерации: | |
— подача, м³/час | |
— напор, м. вод. ст. | |
— мощность электродвигателя, кВт | 3,0 |
Нагрев моющего раствора | паром или ТЭНами |
Давление водяного пара, МПа | 0,3 |
Расход водяного пара, кг/час | |
Мощность электронагрева, кВт | |
Установленная электрическая мощность, кВт: | |
Вариант 1: | |
— при паровом обогреве | |
— при электронагреве | |
Вариант 2: | |
— при паровом обогреве | |
— при электронагреве | |
Габаритные размеры бака (Д х Ш х В) | 2580 ´ 1580 ´ 1700 |
Масса бака, кг |
Машины для водоструйной очистки вагонов и их узлов.
Специализированные моечные машины для водоструйной очистки сборочных единиц и отдельных деталей вагонов.
Рассмотрим подробнее конструкцию и принцип действия специализированных моечных машин для водоструйной очистки сборочных единиц
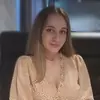