Вспомогательное оборудование в схемах вакуумных фильтровальных установок
В схемах фильтровальных установок используется следующее вспомогательное оборудование: ресиверы, гидравлические ловушки, вакуум-насосы, воздуходувки, клапаны и др.
Ресиверы используют для разделения водовоздушной смеси на жидкость и воздух. Применяются ресиверы с радиальным и тангенциальным вводами разделяемой смеси.
Радиальный ресивер представляет собой цилиндрический резервуар со сферическими крышками и днищами с патрубками ввода смеси, отвода воздуха и фильтрата. Внутри установлен отбойник. Имеется смотровой люк. Попадая в ресивер, поток водовоздушной смеси резко снижает скорость вследствие расширения объема, а также изменения направления движения. Наталкиваясь на установленный в ресивере отбойник-перегородку, газожидкостный поток разделяется: жидкость стекает вниз, а очищенный воздух устремляется вверх.
В последнее время все более широкое применение находят ресиверы с тангенциальным вводом водовоздушной смеси, разделение которой происходит в поле центробежных сил.
Вакуум-насосы. Для создания разрежения применяются поршневые или водокольцевые вакуум-насосы. Поршневые насосы (обычно ВН-120М) применяются на многих действующих горно-обогатительных комбинатах. Как показала практика, для поршневых насосов требуется тщательная очистка отсасываемого воздуха от воды и твердых частиц во избежание быстрого износа клапанов, колец и пр. Однако эти насосы обладают высоким к.п.д. (до 85%) и пониженной энергоемкостью. Поршневые насосы представляют собой одноступенчатые одноцилиндровые горизонтальные машины двойного действия, создающие разрежение до 100 кПа.
Водокольцевые вакуум-насосы ВВН-300 нашли применение на горно-обогатительных комбинатах большой производительности. Они не нуждаются в высокой степени очистки воздуха . кроме того в рабочей полости этих машин нет трущихся деталей, что обеспечивает их большую долговечность. Насос состоит из частично заполненного водой корпуса, в котором эксцентрично расположено рабочее колесо с изогнутыми лопатками. Недостаток водокольцевых насосов – их низкий коэффициент полезного действия, составляющий 35%.
Воздуходувки. Для создания давления воздуха при отдувке осадка в отделениях фильтрования широкое применение находят водокольцевые воздуходувки и турбовоздуходувки. Конструктивно водокольцевые воздуходувки типов ВВН и ГРМК не отличаются от водокольцевых вакуум-насосов, но комплектуются более мощными электродвигателями.
Турбовоздуходувки значительно производительней водокольцевых воздуходувок и потребляют меньше энергии на 1 м3 воздуха. Подача их достигает 200 м3/мин. Поэтому они рекомендуются к применению на фабриках высокой производительности.
Ловушки. Для предохранения вакуум-насосов от возможного попадания в них жидкости и конденсирующихся паров из ресивера, а также на случай аварийного состояния системы удаления фильтрата, применяют барометрические конденсаторы, называемые ловушками. Ловушку устанавливают между ресивером и вакуум-насосом выше ресивера. Внутри ловушки имеется отбойник-перегородка. Ловушка соединяется одной трубой с ресивером через его крышку, а другой трубой с вакуум-проводом, идущим к вакуум-насосу. Для стекания остатков фильтрата служит барометрическая труба длиной 10 м.
Гидрозатвор представляет собой приемник прямоугольного сечения объемом примерно 1 м3, заполненный водой, в которую опущена барометрическая труба. Фильтрат из гидрозатвора переливается в зумпф, откуда насосами перекачивается в определенное место технологической схемы фабрики. Во избежание заиливания гидрозатвора частицами твердого к нему подводится свежая вода для периодической промывки днища.
Характеристики основного и вспомогательного оборудования в отделениях фильтрования горно-обогатительных комбинатов приведены в литературе [5].
Фильтрование под действием избыточного давления применяется для труднофильтруемых пульп с тонкодисперсными частицами в тех случаях, когда вакуум-фильтры не дают хороших результатов. Главным преимуществом использования напорных фильтров является то, что достигается более высокая разность давлений по обеим сторонам фильтрующей перегородки (движущая сила фильтрования), в результате чего повышается степень фильтрации и снижается конечная влажность продукта. Давление в фильтр-прессах может достигать 2 МПа и, следовательно, эти фильтры могут быть использованы для получения кека с высоким удельным сопротивлением.
На зарубежных обогатительных фабриках фильтр-прессы получили значительное распространение, поскольку позволяют получать осадок минимальной влажности. Их применяют на углеобогатительных фабриках, на гидрометаллургических заводах, при обезвоживании каолиновых, тальковых суспензий, а в последние годы достаточно широко для обезвоживания концентратов цветных металлов (медные, цинковые, свинцовые, оловянные, никелевые, кобальтовые концентраты), шламов. Фильтр-прессы как аппараты, допускающие большой перепад давлений, обладают высокими показателями обезвоживания и чистоты фильтрата.
По характеру работы фильтр-прессы подразделяются на аппараты периодического и непрерывного действия. По направлению перемещения фильтровальных плит подразделяются на горизонтальные и вертикальные фильтр-прессы. В зависимости от устройства фильтровальных камер различают горизонтальные, рамные, камерные, диафрагмовые (мембранные), а также непрерывно действующие ленточные фильтр-прессы. В зарубежной практике для обезвоживания тонкоизмельченных продуктов крупностью менее 30–40 мкм используются трубчатые фильтр-прессы, в которых давление фильтрования достигает 14·105 Па.
Принцип работы всех фильтр-прессов при всем многообразии конструкций одинаков. В фильтр-прессах фильтрование происходит в вертикальных или горизонтальных камерах, образуемых фильтровальными плитами, перфорированные, ребристые или рифленные стенки которых обтянуты фильтротканью. При сжатии плит в образующиеся камеры подают пульпу под давлением до полного заполнения камер, при этом жидкая фаза “отжимается” через фильтроткань и на ней формируется осадок. Во многих конструкциях фильтр-прессов предусмотрено диафрагменное сжатие осадка при подаче воды под давлением или сжатого воздуха в пространство над резиновой диафрагмой, установленной на одной из стенок камер. При необходимости осуществляется продувка осадка сжатым воздухом, а при разжиме плит происходит разгрузка осадка.
В более ранней ручной конструкции фильтр-прессы требовали интенсивного труда. Современные фильтр-прессы полностью автоматизированные.
Горизонтальные фильтр-прессы благодаря вертикальному расположению плит отличаются развитой фильтрующей поверхностью, относительно простой конструкцией и могут быть полностью механизированы и автоматизированы. Горизонтальный фильтр-пресс (рис. 4.22) состоит набора вертикально расположенных фильтровальных плит 1, размещенных между концевыми плитами: неподвижной упорной 2 и подвижной натяжной 4. Подвижные плиты экипированы фильтровальной перегородкой. При сжатии плит образуются камеры с каналами подачи фильтруемой суспензии, сжатого воздуха, промывной жидкости и отвода фильтрата.
Рис. 4.22. Схема устройства горизонтального фильтр-пресса
Фильтровальные плиты передвигаются на двух параллельно расположенных стяжных штангах 3, закрепленных в упорной плите 2 и в стойке 6 зажимного устройства 5. Усилия, возникающие при фильтровании под давлением, воспринимают концевые плиты 2 и 4.
Фильтр работает следующим образом. После зажима плит в образованные ими камеры под давлением подается суспензия. При полном заполнении камер на фильтровальной ткани формируется осадок. Фильтрат отводится по каналам наружу. Процесс фильтрования осадка продолжается до полного заполнения им всего объема камер. Затем при необходимости производится промывка и просушка его сжатым воздухом. После просушки осадка отодвигается нажимная плита, промежуточные плиты разжимаются поочередно. Осадок разгружается, после чего цикл повторяется.
![]() ![]() ![]() |
В рамных фильтр-прессах (рис. 4.23, а) осадок накапливается в пространстве между чередующимися плитами 1 и рамами 2. Фильтровальные плиты, экипированные фильтротканью, имеют дренажную поверхность. Для выхода фильтрата в них предусмотрены отверстия. Плиты и полые рамы расположены между опорной 3 и нажимной 4 плитами. Последовательность операций обезвоживания следующая: фильтрование, промывка, просушка, разжим плит, выгрузка осадка.
В камерных фильтр-прессах (рис. 4.23, б) осадок накапливается в камерах, образующихся между двумя соседними плитами вследствие имеющихся в них углублений. Камерный фильтр-пресс состоит из фильтровальных плит 1 одинаковой конструкции, между которыми в два слоя 2 и 3 уложена фильтровальная ткань. При сближении плит она служит уплотнением образующихся камер. По каналу 5 подается фильтруемая суспензия. Фильтрат собирается на рифленой поверхности плит и удаляется по каналам 4 и 6. Жидкость для промывки подается по каналу 5. Последовательность операций обезвоживания на камерном фильтре аналогична рамному.
Мембранные или диафрагмовые фильтр-прессы для отжима осадка снабжены эластичными (резиновыми или резинотканевыми) мембранами или диафрагмами. Обезвоживание осадка осуществляется под давлением воды или воздуха, подаваемыми под диафрагмы. Схема одной из разновидностей мембранного фильтр-пресса показана на рис. 4.22, в. Между фильтровальными плитами, экипированными фильтротканью 3, расположены отжимные плиты 2, снабженные диафрагмами 4. Фильтровальные и отжимные плиты находятся между нажимной 7 и упорной 9 плитами, суспензия подается по каналу 8, сжатый воздух – по каналу 6. Фильтрат отводится через отверстия в перфорированных листах 5 и каналы 10.
Применение диафрагм позволяет сформировать осадок равномерной толщины, сократить расход сжатого воздуха, снизить влажность осадка. Наиболее целесообразно использование мембранных фильтр-прессов при обезвоживании сжимаемых осадков.
Заводом «Прогресс» серийно выпускаются: рамный фильтр-пресс ФПГ-140 с общей площадью фильтрования 140 м2, ФРАМ‑200 с общей площадью фильтрования 200 м2, камерный диафрагмовый фильтр-пресс ФПАВ-300 с площадью фильтрования 300 м2, камерный бездиафрагмовый фильтр-пресс ФКМ-600 с площадью фильтрования 600 м2.
Заводом «Прогресс» изготавливаются фильтр-прессы ФКМ с верхней подвеской плит на базе европейских плит LENSER: размером 1200´1200 мм (типоразмерный ряд 25–160 м2) и 1500´1500 мм (100–500 м2). Условное обозначение: Ф – фильтр-пресс, К – камерный с вертикальными плитами, М – механизированный зажим.
Фильтр-пресс состоит из комплекта фильтровальных плит, подвешенных с помощью специальных кронштейнов на верхней балке (включающей в себя механизм перемещения плит), нажимной плиты, передней и задней опор, механизма зажима (электромеханического или гидравлического), устройства для регенерации фильтроткани, гидроуправляемых поддона и технологической запорной арматуры. Суспензия через центральный коллектор подается в фильтровальные камеры сжатого комплекта плит. Жидкая фаза проходит через фильтрующую салфетку и отводится в коллектор. При необходимости возможна промывка осадка. По окончании цикла фильтрования подается воздух для просушки осадка. Осадок из межплиточного пространства саморазгружается в процессе перемещения плит к отодвинутой нажимной плите. Толщина осадка 30 мм. Отличительными особенностями фильтр-прессов ФКМ являются:
· высокое рабочее давление (до 1,5 МПа) обеспечивает фильтрацию труднофильтруемых суспензий и значительно более высокую производительность .
· полипропиленовые плиты более долговечны и дают возможность работы с агрессивными средами .
· верхняя подвеска плит позволяет снизить энергозатраты и обеспечивает высокую скорость выгрузки осадка .
· проще в техническом обслуживании и ремонте .
· не нуждаются в специальном фундаменте.
Вертикальные фильтр-прессы. Наиболее распространенными являются автоматические камерные фильтр-прессы типа ФПАКМ, выпускаемые Бердичевским заводом «Прогресс».
Камерный автоматический фильтр-пресс типа ФПАК (рис. 4.24) состоит из верхней упорной 10, нижней нажимной 13 и ряда параллельных, горизонтально расположенных, фильтровальных плит 12, между которыми проходит бесконечная лента фильтроткани 6, огибающая ролики 4, где происходит съем осадка с нее ножами 5 в приемники. Натяжение фильтроткани производится с помощью устройства 7, промывка ее и зачистка скребками – в камере регенерации 2.
![]() |
Фильтровальные плиты могут передвигаться вверх и вниз вдоль плоских стяжек 11, которые служат направляющими для роликов плит. Зазор между плитами при их опускании 45 мм. Между плитами зигзагообразно в виде бесконечной ленты протянута фильтровальная ткань. Ткань приводится в движение приводным барабаном и прижимными роликами, установленными на прижимной плите.
Кек разгружается на обе стороны фильтра. После выхода из межплиточного пространства ткань проходит камеру регенерации и роликовые приспособления, поступая снова в межплиточное пространство.
При сжатии плиты образуют два коллектора, из которых один 8 служит для подачи исходной пульпы, промывной воды, сжатого воздуха, второй 9 – для отвода фильтрата, промывной воды и воздуха. Установка опирается на раму.
Фильтр-прессы ФПАКМ изготовляют в двух исполнениях: с диафрагмами для отжима и без диафрагм с просушкой осадка воздухом.
Фильтровальная плита (рис. 4.25) состоит из верхней и нижней рам. Верхняя рама перекрывается перфорированным листом, покрытым фильтротканью, и является камерой для отвода фильтрата. Нижняя рама при сжатии плит служит камерой фильтрования. Под днищем нижней рамы закреплена эластичная диафрагма, на которую подают воду под давлением 1,17 МПа для отжатия влаги из осадка.
![]() |
Фильтр-пресс работает периодически. Цикл фильтрования состоит из следующих основных операций:
1. При помощи электромеханического зажима фильтровальные плиты сжимаются вместе с фильтротканью с одновременным гидравлическим уплотнением образующихся камер.
2. Через коллектор под давлением (до 500 кПа) подается исходная суспензия в пространство, ограниченное диафрагмой и фильтротканью. Фильтрат проходит через ткань и перфорированное днище в камеру фильтрата и отводится по коллектору, а твердые частицы оседают на ткань, образуя осадок.
3. По истечении определенного времени подачу суспензии прекращают и при необходимости осадок промывается водой и просушивается сжатым воздухом (под давлением 400–500 кПа), подаваемыми через коллектор 8.
4. Для труднофильтруемых осадков в цикл фильтрования включается операция отжима влаги из осадка при помощи эластичной диафрагмы, расположенной над осадком. В полость над диафрагмой подается вода под давлением, диафрагма растягивается и выжимает воду из пор между частицами.
5. Плиты раздвигаются с образованием зазора и включается лентопротяжной механизм. Кек, образовавшийся на фильтроткани, при огибании ею направляющих роликов снимается ножами и сбрасывается на конвейер.
6. Плиты снова уплотняются и цикл повторяется.
Толщина кека может достигать 35 мм. Работа фильтр-пресса полностью автоматизирована. Период полного цикла фильтрования составляет 10–30 мин в зависимости от крупности фильтруемого материала и консистенции пульпы.
Преимущества фильтр-прессов: значительная площадь фильтрования . возможность использования больших (до 2 МПа) перепадов давления на фильтровальной перегородке . минимальное содержание твердого в фильтрате . низкая влажность получаемых осадков – 7–8 до 10%.
К недостаткам фильтр-прессов следует отнести то, что они остаются значительно более сложными и дорогими аппаратами по сравнению с вакуум-фильтрами.
На Среднеуральском медеплавильном заводе на фильтр-прессе ФПАКМ-25 при обезвоживании цинкового концентрата с содержанием твердого в питании 65% получен кек с влажностью 12%. В то время как на действующих дисковых вакуум-фильтрах ДУ 68-2,5 влажность осадка составляет 15,5–16,5%.
При фильтровании особо труднофильтруемых концентратов марганцевых шламов на фильтр-прессах по сравнению с вакуум-фильтрами получают осадок значительно меньшей влажности (до 26–28%).
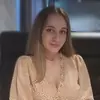