Металлами называют вещества, обладающие своеобразным металлическим блеском, пластичностью, высокой прочностью, электро- и теплопроводностью, ковкостью и свариваемостью, что обусловлено особой природой металлической связи. У металлов своеобразные не только физические, но и химические свойства: способность к окислению и восстановлению в реакциях.
Большинство химических элементов (82 из 109- 75%) относится к металлам.
Свойства сплавов обычно резко отличаются от свойств исходных металлов и их можно регулировать.
Содержание химических элементов в земной коре колеблется в больших пределах. Наиболее распространенными и ценными являются:
— алюминий – 9%
— железо – 55
— магний – 2%
— метан – 0,655
Содержание остальных металлов составляет около 2%. Ряд металлов (цинк, олово, свинец, кобальт, вольфрам, молибден, ванадий) содержатся в тысячных долях процента, но имеют большое значение для получения высококачественных сплавов.
Характерная особенность строения металлов – наличие металлической связи между атомами. Атомы металлов на внешней оболочке содержат небольшое количество слабосвязанных электронов. Электронные облака атомов перекрываются, поэтому внешние электроны могут свободно перемещаться и являются как бы общими, не связанными с отдельными атомами. Таким образом, общие электроны образуют электронный газ, который свободно перемещается между ионами и скрепляет их друг с другом. Эта особенность определяет стремление атомов металла располагаться как можно плотнее. Компактная упаковка атомов приводит к повышенной плотности металлов.
|
|
Металлы и сплавы в твердом состоянии имеют кристаллическое строение, которое характеризуется определенным, закономерным расположением атомов. Атомы в кристалле металла образуют пространственно кристаллическую решетку, состоящую из многократно повторяющихся ячеек, имеющих относительно простую форму.
В промышленных металлах наиболее распространены следующие кристаллические решетки (рис. 1): кубическая объемно-центрированная, кубическая гранецентрированная и гексагональная. В элементарной кубической объемно-центрированной решетке находится девять атомов (восемь в вершинах куба и один в центре).
Такую решетку имеют: железо при температуре до 910 °С и выше 1390 °С, хром, вольфрам, ванадий и др. В кубической гранецентрированной решетке 14 атомов (восемь в вершинах куба и по одному в центре каждой грани). Такую решетку имеют: железо при температуре 910-1390 °С, медь, никель, алюминий и др. В гексагональной решетке, имеющей форму шестигранной призмы, 17 атомов (12 в вершинах, два в центре оснований и три внутри призмы). Данная решетка имеется у магния, цинка и других металлов.
|
|
Возможны и другие формы кристаллических решеток. Атомы в решетке находятся на определенных расстояниях один от другого. Эти расстояния очень малы и вычисляются в нанометрах (1 нм = 10 м). Расположение атомов, межатомные расстояния, насыщенность атомами — все это влияет на качество металлов.
Размеры кристаллической решетки характеризуются параметрами (периодами) — расстояниями между центрами атомов, расположенных в узлах элементарной ячейки. Например, для железа эти параметры равны 28,4-36,3 нм.
![]() |
![]() |
![]() |
![]() |
Рис. 1. Основные виды элементарных ячеек кристаллических решеток металлов а — объемно-центрированная кубическая . б — гранецентрированная кубическая . в – гексагональная плотноупакованная
При этом плотность и степень упаковки атомов кристаллической решетки характеризуется отношением бесчисленного множества кристаллических образований, группирующихся в виде отдельных прочно связанных между собой зерен. Большинство их имеет кубическую объемно-центрированную (хром, ванадий, молибден, вольфрам и некоторые другие) и кубическую гранецентриро-ванную решетки (алюминий, медь, никель, свинец, золото и серебро). Железо может быть в нескольких кристаллических формах с различным расположе-нием атомов. Это явление называется аллотропией. Аллотропические превращения железа наблюдаются при изменении температуры. Железо из расплавленной массы кристаллизуется в форме решетки объемно центрированного куба (рис. 1, 1) — δ – модификация железа . при охлаждении до температуры 1390 °С она перекристаллизовывается в решетку гранецентрированного куба (рис. 1, 2) — γ — модификация железа, а при 898 °С снова образует решетку объемно центрированного куба β и α-модификации. Аллотропия железа имеет большое значение в процессах горячей механической и термической обработки чугуна и стали. Главную роль при этом играют α- и γ-модификации железа. Регулируя закалкой, отжигом и другими способами содержание этих модификаций в сталях, придают им заданные механические свойства.
Кристаллическая природа металлов обуславливает анизотропию их свойств, т.е. различие свойств металлов в зависимости от направления кристаллографических осей, образующих кристаллы металлов.
Процесс перегруппировки атомов в кристаллографической решетке происходит в твердом состоянии металла подобно процессу затвердевания жидкого сплава при определенных- температурах и сопровождается тепловым эффектом. Этот процесс образования новых кристаллов из кристаллов прежней модификации называется вторичной кристаллизацией.
Металлические сплавы, представляющие собой поликристаллические тела, в которых кристаллиты (кристаллические образования, которые при правильном внутреннем строении не сохранили в процессе роста правильную форму кристалла вследствие помех соседних кристаллов) различно ориентированы один относительного другого, обладают мнимой изотропностью (квазии-зотропны). Однако в результате технологической обработки сплава (прокатки, волочения, ковки и т.д.) происходит ориентировка кристаллов по направлению обработки, и металл становится анизотропным. Некоторые механические свойства металлических сплавов при технологической и термической обработках повышаются в направлении главных кристаллографических осей. Этим частопользуются при изготовлении некоторых деталей машин и металлических строительных изделий.
Процесс кристаллизации металлических сплавов начинается при охлаждении жидкого сплава и продолжается у многих сплавов до определенных температур в отвердевшем состоянии в виде перекристаллизации. На размер и форму образующихся кристаллов влияет скорость охлаждения жидкого сплава: при медленном охлаждении образуются крупные зерна, а при быстром — металлический сплав приобретает мелкозернистое строение.
|
|
В настоящее время измельчение зерна металла достигается не только за счет увеличения скорости охлаждения, но и за счет введения различных присадок, увеличивающих число центров кристаллизации при V=const и создающих условия для замедленного роста кристаллов. Этот метод измельчения зерна называется модифицированиеми применяется при выплавке специальных чугунов, сталей и некоторых цветных металлов.
Основными способами модифицирования структуры и свойств стали применяемыми в современной металлургии, являются:
— введением в расплавленный металл веществ образующих тугоплавкие соединения, являющиеся центрами кристаллизации (Ti, Al, Si, Mn) .
— введение лигирующих элементов, повышающих прочность кристаллических решоток феррита и ацетенита, замедляющих диффузионные процессы выделения углерода, карбидов и движение дислокаций .
— термическая и пормомеханическая обработка.
При затвердевании металлических слитков, болванок, заготовок образуются различные по крупности кристаллы: более мелкие у наружной поверхности, а более крупные внутри слитка. Кроме того, кристаллы ориентированны различно: внутри слитка они имеют более правильные формы, чем в наружных слоях, а чаще всего приобретают разветвленную древовидную форму. Такие скопления кристаллов в слитках называются дендритами. Возможно также образование кристаллов пластинчатой, игольчатой и других форм.
Затвердевание слитка по всему объему происходит не одновременно, поэтому и строение слитка неоднородно. В верхней части, у поверхности слитка, затвердевающего в первую очередь, образуются усадочные раковины, окруженные макро и микропорами.
При ускоренном охлаждении сплава внутри отливки могут образоваться полости — газовые пузыри — за счет газов, не успевших удалиться из металлов.
|
|
Подобная неоднородность отливок может привести к снижению их механических свойств.
Соответствующей механической обработкой отливки (давлением, прокаткой) с последующей термической обработкой можно придать волокнистое строение в направлении обработки и уменьшить размер зерен, что улучшает его механические свойства. В жидком состоянии большинство сплавов представляет собой однородный жидкий раствор. При переходе в твердое состояние однородность многих сплавов сохраняется за счет внедрения или замещения атомов в кристаллографической решетке растворителя атомами других более легких элементов.
Структура реальных сплавов в значительной степени отличается от идеального строения кристаллов. В реальном металле всегда имеются нарушения макро- и микроскопического характера (поры, газовые и неметаллические включения, микротрещины и пр.), а также дефекты кристаллического строения, связанные с нарушением правильного расположения атомов в самой кристаллической решетке. Все эти виды нарушений заметно влияют на свойства, причем наиболее велика роль несовершенства кристаллического строения, так называемых дислокаций. Из-за присутствия в металле дислокаций теоретическая прочность не реализуется. Прочность реальных кристаллов обычно составляет не более 1-5% от теоретической, рассчитанной по силам связи между атомами. В конструкции же, когда на эксплуатационные характеристики металла оказывают такие факторы, как наличие надрезов, напряженное состояние, температурные условия эксплуатации, агрессивность окружающей среды, используется только от 40 до 80% прочности исходного металла.
Член – корреспондент АНСССР И. А. Одинг еще в конце 40х годов прошлого столетия, сформулировал основные закономерности изменения прочности кристаллических тел в зависимости от от плотности дислокаций, благодаря им получили интенсивное развитие:
1. получение металлов с кристаллическим строением близким к совершенству (создание бездислакационных кристаллов с прочностью приближающейся к теоретической), и разработка на этой основе высокопрочных композиционных материалов .
2. создание в уже имеющихся материалах повышенной или высокой плотности дислокаций, что при условии равномерного или периодического распределения в объеме металла позволяет в несколько раз повысить его прочность .
Во втором пути повышения прочности металлов используются два основных метода:
— пластическая деформация (механическая энергия) для достижения необходимой плотности дислокаций .
— термическое воздействие (тепловая энергия).
Наиболее эффективно повышает прочность комбинация этих двух способов с названием термомеханическая обработка (ТМО).
Влияние структурных составляющих на свойства железоуглеродистых сплавов
Основными структурными составляющими железоуглеродистых сплавов является графит, феррит, цементит, аустенит, ледебурит и перлит, обладающие различными свойствами . поэтому количественное содержание их сильно влияет на свойства железоуглеродистых сплавов.
Графит — мягок, его истинная плотность 2,25 г/см3, он нарушает сплошность металла, понижая сопротивление растяжению и вязкость, увеличивает хрупкость тем больше, чем крупнее его частицы. Графит характеризует микроструктуру литейных чугунов.
Феррит — твердый раствор углерода в aFe, мягкий, вязкий, хорошо куется и сваривается. Чем больше в металле феррита, тем металл мягче, более ковок и тем больше дает удлинение при растяжении.
Цементит — карбид железа Fe3C. С увеличением его содержания сначала возрастают твердость и прочность металла (наибольший предел прочности при растяжении — при содержании углерода 1,2%) . с дальнейшим увеличением количества цементита сопротивление падает, вязкость уменьшается, а твердость и хрупкость возрастает.
Аустенит — твердый раствор углерода в γ Fе . содержит до 2% углерода. В обыкновенных сталях аустенит устойчив только при температуре выше 723°С В легированных сталях, содержащих в своем составе некоторое количество Мп, Cr, Ni и других элементов, аустенит может быть устойчивым и при обычной, и даже низкой температуре. Механические свойства аустенита зависят от содержания в нем углерода. С уменьшением количества углерода аустенит становится более мягким и вязким . с увеличением — более твердым и хрупким.
Ледебурит — эвтетика (цементит + аустенит), очень тверд и хрупок, присутствует в белых чугунах. Образуется при температуре 1130 °С и содержит углерода С=4,3% — эвтектический чугун.
Перлит — эвтектоид (феррит + цементит), обладает сравнительно высокой прочностью, достаточно вязок, имеет зернистое или пластинчатое строение. Образуется в процессе распада аустенита при температуре723°C и содержанием углерода 00,83%, примеси Si, Мпспособствуют образованию перлита и при меньшем содержании углерода.
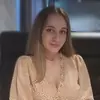