Шунгизит
Шунгизит получают вспучиванием при обжиге графитсодержащей сланцевой породы — шунгита. Шунгизитовый гравий получают по сухому способу. В сущности шунгизит — это разновидность керамзита, отличающаяся видом сырья.
Крошка со склада сырья, рассчитанного на работу линий в течение 15 сут, родается скиповыми подъемниками в расходные бункера, установленные над печами термоподготовки (2,5X20 м). В этих печах материал нагревается до 400°С примерно за 20 мин, а затем через перегрузочные камеры поступает в печи обжига (3,5X24 м), где находится в течение 12… 15 мин (производительность одной печи 12,5 м3/ч). Вращение печей термоподготовки и обжига с различной скоростью позволяет осуществлять ступенчатый режим термообработки шунгитовой крошки, вспучивающейся обычно при температуре 1120… 1150С. Узкий температурный интервал вспучивания (до 30°С, что значительно меньше требуемого при производстве керамзита) усложняет обжиг сырья. Во избежание образования спеков в печь перед зоной обжига вводят опудривающий порошок.
Охлаждение шунгизита производят в две стадии: сначала с 900 до 550°С в барабанном холодильнике (2,2X16 м) в течение 20 мин, а затем до 60… 80°С в аэрожелобе длиной 10 м в течение 2 мин. «Мягкий» режим охлаждения способствует снятию термических напряжений в материале и повышению прочности шунгизита.
Охлажденный шунгизит конвейером с погруженными скребками направляется на склад готовой продукции, где после сортировки хранится по фракциям в силосах (8 шт.).
Применяется шунгизит для теплоизоляционных и конструкционно-теплоизоляционных легких бетонов.
|
|
Вспученный перлит — материал, получаемый вспучиванием при эбжиге подготовленных зерен из вулканических водосодержащих юрод (перлит, обсидиан, витрофир и др.).
В перлите содержится около 1…2% (иногда больше) связанной воды. При обжиге (1000… 1250 °С) перлит размягчается и под давлением паров высвобождаемой воды сильно вспучивается. Коэффициент вспучивания — до 10… 12. Чем он больше, тем меньше расход сырья на единицу объема продукции. Поэтому многие предприятия, производящие легкий вспученный перлит, работают на привозном сырье с умеренной себестоимостью продукции. Однако если коэффициент вспучивания меньше, удельные затраты на перевозку сырья увеличиваются и себестоимость продукции возрастает.
В соответствии с ГОСТ «Песок и щебень перлитовые вспученные» предусматриваются марки но насыпной плотности для песка 75… 500, для щебня — 200… 500. Прочность щебня при сдавливании в цилиндре для указанных марок должна быть не менее 0,15… 0,9 МП а. Вспученный перлит отличается от других пористых заполнителей высоким водопоглощением, которое тем больше, чем больше степень вспучивания. В стандарте водопоглощение щебня ограничивается: для марки 500 — не более 30%, для марки 400—50%, для марки 300—75%, для марки 250—100%, для марки 200—125% по массе.
В отличие от других пористых заполнителей мелкие фракции вспученного перлита легче крупных. Это объясняется особенностями вспучивания стекловидных пород по сравнению, например, с глинистыми. Так, при производстве керамзита мелкие глиняные гранулы (до 5 мм) часто совсем не вспучиваются, так как еще до размягчения теряют все образующиеся при обжиге газы. Перлитовая же стекловидная порода удерживает газы, и чем лучше она прогревается в мелких гранулах, тем интенсивнее вспучивается.
Технология производства вспученного перлита включает дробление исходной породы (до 1… 2 мм при производстве песка и до 5… 10 мм при производстве щебня) и сортировку. Перед обжигом сырье в ряде случаев рекомендуется подвергать предварительной термической обработке в сушильном барабане или малой вращающейся печи при температуре 250… 450°С в течение нескольких минут. При этом удаляется свободная и слабосвязанная вода, в дальнейшем зерна породы могут при обжиге выдержать более высокую температуру, не растрескиваясь. Остаточной, трудноудаляемой воды в зернах вполне достаточно для бурного вспучивания при температуре до 1250°С.
Для получения вспученного перлита используют вертикальные (шахтные) и вращающиеся печи, а также печи кипящего слоя. Выбор конструкции печи определяется размером обжигаемых зерен, требуемыми свойствами заполнителя и запланированной производительностью.
При производстве вспученного перлитового песка применяют шахтные печи. Печь представляет собой вертикальный футерованный изнутри цилиндр с конической нижней частью. Поток горячих газов от сжигания топлива направляется снизу вверх. Поскольку площадь сечения конической части печи с подъемом увеличивается, скорость газового потока соответственно уменьшается. Через загрузочные отверстия в верхнюю цилиндрическую часть печи подается дробленая перлитовая порода и свободно падает вниз, пока в конической части не подхватывается восходящим потоком горячих газов. Зерна породы, витая в горячей газовой струе, вспучиваются. При этом парусность их резко увеличивается, и оии увлекаются газовым потоком вверх, выносятся из печи и затем Ьсаждаются в циклонах.
Технология производства вспученного перлитового щебня и песка предусматривает термическую обработку сырья во вращающихся печах. Легкие мелкие фракции песка вспучиваются в основном во взвешенном состоянии и уносятся из печи потоком отходящих газов (с последующим осаждением в циклонах). Более крупные фракции, не увлекаемые газовым потоком, вспучиваются на футеровке печи и выгружаются. Для ускорения нагрева материала используют принцип прямотока, т. е. факел горящего топлива и поток газов направляют не навстречу потоку обжигаемого материала (как при получении керамзита), а в том же направлении — по наклону печи.
Для получения вспученного перлита с зернами размером до 10 мм, в основном крупного песка, обжиг целесообразно производить в двухзонных печах кипящего слоя.
Применяют вспученный перлит в качестве теплоизоляционного материала и заполнителя для особо легких теплоизоляционных и конструкционно-теплоизоляционных, а также жаростойких бетонов.
В ряде случаев перлитовый песок используют как мелкий заполнитель в других видах легкого бетона: керамзитоперлитобетоне, шлакопемзоперлитобетоне и других, в которых крупный заполнитель — керамзит, шлаковая пемза, а мелкий — вспученный перлит. Опыт показал, что при этом насыпная плотность перлитового песка должна соответствовать М 200 или более, а содержание в нем фракции мельче 0,16 мм не должно превышать 10% по объему.
В связи с большим водопоглощением вспученного перлита и замедленной влагоотдачей представляет интерес его гидрофобизация растворами ГКЖ-10 и ГКЖ-11, при которой значительно уменьшается водопоглощение и создаются условия для более эффективного использования вспученного перлита. Представляет интерес также баротермальный способ получения вспученного перлита, предложенный Г. И. Еворенко. При этом перлит сначала нагревается до температуры размягчения под давлени- -ем в паровой среде, а затем при сбросе давления вспучивается. Этим способом можно получить очень легкий материал со сравнительно высокой прочностью и малым водопоглощением.
|
|
|
|
Вспученный вермикулит
Вермикулит — разновидность слюды, магниево-железистый гидроалюмосиликат с содержанием связанной воды 8… 18%. Это сравнительно мягкая горная порода золотистого цвета с перламутровым блеском.
Месторождения вермикулита встречаются на Урале, в Мурманской области, Якутии, в ряде районов Сибири и Дальнего Востока.
При температуре 1000… 1200°С вермикулит вспучивается, увеличиваясь в объеме в 15…20 раз и более. Получается пористый материал в виде песка и щебня с насыпной плотностью 80… 300 кг/м3. Из вспученного вермикулита можно получать особо легкие бетоны небольшой прочности для теплоизоляции. В крупнопанельном домостроении вермикулитобетон используется для утепления панелей наружных стен и совмещенных кровельных покрытий.
Автоклавные силикатные материалы: сырье, особенности производства, изделия. Автоклавными силикатными изделиями называют изделия, изгот. из смеси извести и мелкозернистых материалов процесс твердения которых происходит в автоклавах под давлением пара 8-12 ат. Вместо извести в произв-ве силикатных изделий могут быть примен. нефелиновое вяжущее, известково-шлаковые и извест-ково-песчаные цементы. Иногда к известково-песчаным смесям, предназначенным для высокопроч. автоклавных бетонов, добавляют в небольших количествах цемент.
|
|
В состав силикатных масс могут входить легкие заполнители: шлак, керамзит, вспученный перлит, опилки. Такие добавки повышают трещиностойкость изделий.
Автоклавным способом можно получить неармированные и армированные изделия плотной, ячеистой и пористой структур способами виброформования, литья, проката. Эти изделия имеют плотность 300-2000 кг/м3, предел прочности при сжатии (5-1000)*105н/м2, водопоглощение 15-80%, температуростойкость 500-600° С, морозостойкость 5-100 циклов, коэфф. линейного расширения 0,000005-0,000008. При этом расход извести или другого местного вяжущего на 1 м3 изделия равен 150-200 кг, что значительно ниже потребности в цементе для получения обычного бетона такой же прочности.
К числу автоклавных силикатных изделий отн. Силик. кирпич, крупные силик. блоки разного назначения, панели и другие виды изделий. плотность силикатного кирпича 1750-1900 кг/м3, коэфф теплопровод 0,7-0,87 вт/м град. Применяют силикатный кирпич в строительстве наряду с глиняным, но с некоторыми ограничениями — не допускается без специальных защитных мер кладка из силикатного кирпича зданий с влажным режимом при эксплуатации, кладка печей и труб. Последнее ограничение вызвано тем, что при длительном воздействии температур выше 500° С возможно разрушение образовавшихся в кирпиче силикатов. Разновидностью силикатного является битуминизированный кирпич, применяемый для устройства дорожных покрытий, кладки фундаментов и облицовки в сырых местах. Из бетона изготовляют пустотелые стеновые блоки плотностью 1400-1500 кг/м3, полнотелые блоки для фундаментов (обработанные битумными материалами), блоки внутренних несущих стен, колонны, балки, панели перекрытий, лестничные марши и площадки, подоконные доски, трубы. Такие изделия изготовляют из плотного силикатного бетона марки не ниже 150. Элементы, работающие на изгиб, армируют. При изготовлении стеновых элементов с целью понижения массы возможна добавка легких заполнителей. При добавке 80-100 кг цемента на 1 м3 массы можно изготовлять сборные элементы для фундаментов без обработки битумом и т. д.
Крупногабаритные изделия изготовляют литьем в формах из пластичных масс либо виброформованием с пригрузом из жестких масс. Так, при виброформовании с пригрузом изготовляют прочные тяжелые конструктивные изделия с объемной массой 2000 кг/м3, при литье — облегченные и легкие.
Кровельные и гидроизоляционные материалы на основе органических вяжущих веществ Органические вяжущие включают в себя битумные и дегтевые вяжущие, полимеры и органические клеи. На основе этих вяжущих производят: асфальтовые бетоны и растворы, рулонные кровельные и гидроизоляционные материалы, мастики, пасты, эмульсиии некоторые лаки. Кровельные рулонные материалы. Удобный вид кровельного материала для плоских (угол наклона 3-6º) кровель. В качестве основы рулонного материала применяют картон кровельный, стеклоткани, фольгу. На картонной основе производят рубероид, пергамин и толь . на стеклооснове — стеклорубероид и армогидробутил . на основе фольги — фольгоизол и фольгорубероид. Кровельный картон получают из вторичного текстиля, макулатуры и древесного сырья. имеет рыхлую структуру и хорошо впитывает влагу и другие жидкости (в частности, расплавленный битум) Толь — картон, пропитанный и покрытый с двух сторон дегтем (результат сухой перегонки каменного угля, древесины и тд.)Применяется для временных сооружений .Быстро стареет на солнце . Разрушается за 2-3 года. Пергамент –получ пропиткой кров картона расплавл лекгоплавким битумом. Прим для ниж слоёв кровельного крова. Рубероид – многослойный материал, получаемый как и пергамент + с обеих сторон слоя тугоплав битума. Покрывается «бронирующей» посыпкой (песком, слюдой, сланцевой мелочью и т.п.), защищ материал от УФ-излучения. Устройство кровли в зимний период невозможна, из-за хрупкости битумного связующего.Невысокая долговечность- 5-6 лет. Узкий интервал рабочих температур (от 0 до 60-80 ºС)
Штучные материалы. для кровель с большим уклоном(угол наклона 15…60º). Мягкая черепица получ на основе традиционных рулонных материалов, путём вырубки из полотна фигурных полос. Более долговечна, чем рулонные материалы. Волнистые битумно-картонные листы (ондулин) – представляют собой гибкие листы, пропитанные битумом и с лицевой стороны окрашенный атмосферостойкой полимерной краской.
Гидроизоляционные материалыЖидкие гидроизоляционные материалы. Пропиточные материалы – жидкости, проникающие в поры поверхностных слоёв материала и образующие там водопроницаемые барьеры Битумы и дёгти, Битумные эмульсии, Кремний, органические жидкости Инъекционные материалы. Высокая водонепроницаемость Пленкообразующие материалы – вязкожидкие составы, которые после нанесения на поверхность образуют на ней водонепроницаемую пленку. Разжиженные битумы, битумные эмульсии, лаки и эмали. Пастообразные гидроизоляционные материалы Мастики. Получают смешиванием органических вяжущих с минеральными наполнителями и специальными добавками.
Самые распространенные битумные мастики. Выпускаю в двух вариантах: холодные, готовые к употреблению (они содержать растворитель) и горячие, нуждающиеся в нагреве от 160…180 ºС.. Упруго-пластичные гидроизоляционные материалы. Рулонные материалы, аналогичны кровельным. В отличает от кровельных не подвергаются солнечному излучению, но постоянно находятся во влажных условиях. Используют битумные и полимербитумные материалы на негниющих основах. Гидростеклоизол – битумный гидроизоляционный материал, состоящий из стекловолокнистой основы, на которую с двух сторон нанесен слой битумного вяжущего, состоящего из битума, минерального наполнителя (20% от массы вяжущего) и пластификатора-мягчителя. Укрепляется на поверхности путём оплавления пламенем газо-воздушных горелок. Рекомендуемая температура работ не нижу 10 ºС. Предназначен для гидроизоляции тоннелей метрополитена, пролетных строений и путепроводов, бассейнов и тп.
Искусственные каменные материалы на основе гипсовых вяжущих веществ. К этой группе относятся изделия, изготовленные на основе гипсовых и гипсоцементно-пуццолановых вяжущих.Быстрое твердение и хорошие формовочные свойства гипса => .сравнительно просто и в короткие сроки изготавливают различные виды изделий для сборного строительства. Смотри учебник.
Сортамент изделий из стали перечень покатных профилей с указанием формы, размеров, массы едениц и допусков. Наиболее экономичными в нем являются тонкостенные профили. Основные виды прокатных профилей:а) листовая сталь, б,в) уголковые профили, е) швеллер, ж)двутавр, гд) трубы бесшовные и электросварные.
Би́ту́мы (от лат. bitumen — горная смола, нефть) — твёрдые или смолоподобные продукты, представляющие собой смесь углеводородов и их азотистых, кислородистых, сернистых и металлосодержащих производных. Битумы не растворимы в воде, полностью или частично растворимы в бензоле, хлороформе, сероуглероде и др. органических растворителях . плотностью 0,95—1,50 г/см³. Классификация
Природные битумы — полезные ископаемые органического происхождения с первичной углеводородной основой. К ним относятся естественные производные нефти, образующиеся при нарушении консервации её залежей в результате химического и биохимического окисления. По составу, зависящему от состава исходных нефтей и условий их преобразования, условно подразделяются на несколько классов: мальты, асфальты, асфальтиты, кериты и антраксолиты. Добычу проводят главным образом карьерным или шахтным способом (Битуминозные пески).
Искусственные (технические) битумы — это остаточные продукты переработки нефти, каменного угля и сланцев. По составу сходны с природными битумами.
Добыча и переработка природных битумов Процесс добычи и комплексной переработки природных битумов производится в следущей последовательности:
- добыча битумосодержащей породы
- разделение битумосодержащей породы на органическую и минеральные части
- транспортировка битума
- переработка битума
В зависимости от условий залегания и физических свойств сырья разработка месторождений природных битумов осуществляется следующими способами:
- карьерным и шахтным очистным, при которых породу извлекают на поверхность, где из нее экстрагируют битум растворителем или горячей водой с добавкой эмульгирующих составов
- шахтным дренажным, при котором природные битумы добываются в шахте самотеком через систему восходящих дренажных скважин, пробуренных из горных выработок
- скважинным внутрипластовым, при котором природные битумы добываются путем термического или иного воздействия на битумонасыщенные породы через скважины, пробуренные с поверхности
Рудничными (карьерным и шахтным) способами разрабатываются месторождения с битумонасыщенностью вмещающих пород не менее 10 % и глубиной залегания 60 — 90 метров. Коэффициент извлечения битума при этом до 85 — 90 %. Примером такой добычи является Ярегское нефтяное месторождение в Республике Коми.
Скважинными способами разрабатываются месторождения жидких природных битумов (битуминозная нефть) с глубиной залегания, как правило, более 100 метров. При скважинных способах коэффициент нефтеотдачи достигает в среднем 30 %. В Татарии битуминозную сверхвязкую нефть в экпериментально-показательном и пока убыточном проекте добывают на Ашальчинском месторождении. Здесь пробурено несколько пар дугообразных с выходом на дневную поверхность скважин. В паре скважины параллельны, располагаясь друг над другом на расстоянии несколько метров. Одна из скважин предназначена для закачки пара, прогревающего пласт. Другая для откачки нефти, ставшей менее вязкой под воздействием прогрева.
Природные битумы не являются сами по себе товарным продуктом, как нефть или газ. Для получения из них товарного продукта нужны дополнительные технологические процессы. В качестве товарного продукта переработки природных битумов может рассматриваться «синтетическая нефть» — вид сырья, альтернативный природной нефти. Кроме того, являясь многокомпонентным полезным ископаемым, природные битумы помимо углеводородов нередко содержат нафтеновые кислоты, сульфокислоты, простые и сложные эфиры, серу, редкие цветные металлы (ванадий, никель, рений) в кондиционных концентрациях. Минимальная концентрация ванадия в природных битумах, при которой выгодна его промышленная добыча составляет 120 г/т, а никеля — 50 г/т.[1]
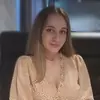