![]() |
Этот способ сварки основан на использовании для Нагрева и расплавления свариваемых деталей энергии электронного луча.
Электронный луч представляет собой сжатый поток электронов, перемещающихся с большой скоростью от катода к аноду в сильном электрическом поле. При соударении электронного потока с твердым телом более 99 % кинетической энергии электронов переходит в тепловую, которая расходуется на нагрев этого тела. Температура в месте соударения может достигать 5000…6000 °С.
В установках для электронно-лучевой сварки (рис. 19.29) происходит эмиссия электронов на катоде 1 электронной пушки. Электроны формируются в пучок прикатодным электродом 2, расположенным непосредственно за катодом, и ускоряются под действием разности потенциалов между катодом и анодом 3, составляющей 20…150 кВ и выше. Затем они фокусируются в виде луча и направляются специальной отклоняющей магнитной системой 4 на обрабатываемое изделие 5. Фокусировкой достигается высокая удельная мощность (от 5 до 105 кВт/м2 и выше). Ток электронного луча невелик (от нескольких миллиампер до единиц ампер).
б
![]() |
I V.& .MM |
AJ |
Рис. 19.29. Схема установки (а) и «кинжальное» проплавление(б) при электронно-лучевой сварке(F.lt F2— сечения швов при дуговой и электронно-лучевой сварке) |
При перемещении заготовки под неподвижным лучом образуется сварной шов. Иногда при сварке перемещают сам луч вдоль неподвижных кромок с помощью отклоняющих систем. Отклоняющие системы используют также и для колебаний электронного луча поперек и вдоль шва, что позволяет регулировать тепловое воздействие на металл. Процесс сварки осуществляется в вакуумных камерах.
Параметрами процесса электронно-лучевой сварки являются ускоряющее напряжение Е/уск . сила тока пучка /п . расстояние от пушки до изделияdи до плоскости фокусировки пучка Ь . скорость сварки ися . глубина вакуума р. Изменяя перечисленные параметры процесса сварки, удается в широких пределах изменять форму сварочной ванны.
Сварку тонколистовых металлов (до 1…3 мм) обычно выполняют расфокусированным пучком электронов при небольших значениях удельной мощности в пятне нагрева (рис. 19.30, а). По термодеформационному циклу такая сварка почти не отличается от аргонно-дуговой сварки неплавящимся электродом.
![]() |
При сварке толстолистовых металлов (рис. 19.30, б) используют острофокусные пучки электронов. Процесс сварки толстолистового металла состоит из следующих этапов. Вначале ввиду высокой концентрации энергии в пятне нагрева и высокого температурного градиента происходит преимущественное испарение металла. Далее по мере нагрева металл плавится и образуется сварочная ванна. Потоки паров, истекая в вакуум, силой реакции воздействуют на жидкий металл, вытесняя его из зоны нагрева. При этом оголяемые глубинные слои металла, воспринимая энергию электронов, плавятся, испаряются и вытесняются, пока не наступает динамическое равновесие всех сил, действующих на жидкий металл. В результате в его толще образуется канал с большим отношением глубины к диаметру. Воспринимающая энергию электронного пучка боковая поверхность канала имеет площадь, во много раз превышающую сечение пучка. Канал устойчив, так как при заполнении хотя бы части его жидким металлом резко увеличивается количество поглощаемой этим металлом энергии, он вскипает и испаряется.
Характерной особенностью электронно-лучевой сварки при высокой мощности являются большие скорости переноса жидкого металла из зоны плавления в зону кристаллизации. В верхней части сварочной ванны жидкий металл выносится на поверхность свариваемого изделия и образует усиление, площадь поперечного сечения которого достигает 10…15 % общей площади поперечного сечения сварочной ванны. Электронно-лучевой сварке толстого металла присущи колебания глубины проплав- ления, но при правильной фокусировке и стабильных параметрах пучка они не превышают 5 % общей глубины проплавления.
Применение электронно-лучевой сварки при изготовлении изделий из тугоплавких и химически активных материалов (Мо, W, Nb, Та и др.) позволяет получить сварные соединения с узкой зоной термического влияния и малыми деформациями без обогащения металла шва вредными примесями. При сварке высокотеплопроводных материалов (меди, алюминия и их сплавов) обеспечиваются высокий термический коэффициент плавления и возможность получения узких и глубоких швов при сравнительно малой мощности электронных пучков. При сварке изделий из сталей обеспечивается большая глубина проплавления и, следовательно, высокая производительность процесса при изготовлении конструкций из толстостенных заготовок.
Для электронно-лучевой сварки характерны как обычные типы соединений, так и принципиально новые. Общее требование ко всем типам соединений — точная сборка деталей перед сваркой.
Обычно отклонение оси пучка электронов от сварного стыка в процессе сварки не должно превышать 0,2…0,3 мм. При толщине свариваемых пластин до 5 мм допустимая величина зазора, как правило, не превышает 0,05…0,07 мм. При увеличении толщины пластин до 20 мм допустимая величина зазора возрастает до 0,1 мм, но не более.
Лазерная сварка
В последнее время в сварочной практике находят применение оптические квантовые генераторы (ОКГ), так называемые лазеры. При лазерной сварке нагрев и плавление металла осуществляются мощным световым лучом, получаемым от специальных твердых или газовых излучателей. Для управления сформированным излучателем лучом служат специальные оптические системы. Вакуум при сварке лазером не нужен, и сварка может осуществляться на воздухе даже на значительном расстоянии от генератора.
Лазерная сварка вследствие высоких значений плотности тепловой мощности в облучаемой зоне характеризуется высокой локальностью нагрева. Она позволяет сваривать металлы с различными теплофизическими характеристиками, в труднодоступных местах, поскольку это бесконтактный способ сварки, а также в любой прозрачной для данного излучения атмосфере или среде. В настоящее время для данной сварки применяются импульсные твердотельные лазеры и газовые лазеры непрерывного действия.
19.10. |
Принципиальная схема импульсной сварочной установки показана на рис. 19.31. Стержень активного материала 4 (например, рубина) и импульсная лампа накачки 3 размещены в полости осветителя 2. Электрическая энергия источника питания 1 преобразуется лампой накачки в световую энергию. Под воздействием света активный материал переходит в состояние, в котором он способен усиливать и генерировать свет определенрой длины волны. Чтобы улучшить условия генерации, стержень активного вещества помещают между двумя зеркалами, очень точно отъюстированными по отношению к стержню. Эти два зеркала и стержень активной среды образуют резонатор. Для вывода из-
Лучения из полости резонатора одно из зеркал делают частично прозрачным. Вышедший из резонатора пучок 5 собирается линзой 6, ив плоскости, где размеры пучка наименьшие, а плотность мощности наиболее высокая, располагают свариваемые детали 7.
![]() |
Режим импульсной лазерной сварки определяется вводимой в свариваемые детали энергией лазерного излучения, длительностью импульса и радиусом светового пятна на облучаемой поверхности свариваемых деталей.
При сварке стыковых соединений возможны три технологические схемы нагрева:
1) фокусировка пятна нагрева на стык соединения — применяется при сходных теплофизических свойствах свариваемых металлов. В результате получается практически симметричный сварной шов .
2) смещение пятна нагрева в сторону более тугоплавкого металла — применяется в том случае, когда один из свариваемых металлов значительно более тугоплавкий. При этом происходит преимущественный нагрев и плавление более тугоплавкого металла. Плавление менее тугоплавкого металла осуществляется за счет теплоты, передаваемой его кромке от расплава .
3) сварка с преимущественным нагревом менее тугоплавкого металла. В этом случае сварное соединение образуется в результате процесса сварки-пайки.
Импульсная лазерная сварка стыковых соединений требует тщательной подгонки кромок свариваемых деталей.
Импульсные твердотельные лазеры применяют для сварки деталей в микроэлектронике и приборостроении, где важно получать малоразмерные швы с минимальным разогревом окружающего зону сварки материала. Сварка может вестись как отдельными точками, так и герметичными швами при последовательном наложении точек с их перекрытием.
Мощные газовые лазеры позволяют проплавлять за один проход, как и при электронно-лучевой сварке, значительные толщины.
Так же как и электронно-лучевая сварка, сварка лазером дает узкий шов «кинжального» типа с малыми деформациями свариваемых деталей, что позволяет применять этот способ для соединения окончательно обрабатываемых узлов и деталей-
Лазерную сварку можно с успехом применять для получения различных типов сварных соединений из многих однородных и разнородных металлов.
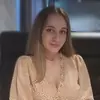